Latest News
July 2, 2012
By Pamela J. Waterman
Fuel cells, human physiology, earthquake prediction, underwater explosions, or simply fluid-structure interactions—whatever complexity your daily projects throw your way, can your design afford to ignore multiphysics effects? If not, how well does your solution environment handle modeling and simulation of two or more interdependent physics effects?
It used to be that this topic was not for the faint of heart. Data, models and software from various engineering or scientific domains needed to be combined in a single environment, and managing the different mesh structures and data transfers was tricky. The push to create more design iterations in less time meant that multiphysics solutions involved a great deal of approximations and assumptions.
![]() |
This titanium speaker cone, surrounded by air and set in an infinite baffle, showcases the new acoustic-shell interaction user interface in COMSOL. The structural vibrations automatically act as a sound source, and the pressure force is coupled back to act on the shell. Applications for this type of simulation range from speakers to ship acoustics. Image courtesy COMSOL. |
Over the past five years, however, both hardware and software offerings have advanced in ways that support solutions of more accurate, tightly coupled problems. While multiphysics takes prominence at COMSOL, ANSYS, ADINA and SIMULIA, software from such major analysis companies as Altair, Autodesk, CD-Adapco, ESI Group, LSTC, MSC Software and Siemens PLM also embrace coupled multiphysics solutions—though each with different subspecialties and approaches.
Bernt Nilsson, senior vice president of marketing at COMSOL, sees continued growth in this field as multiphysics analyses have become easier to conduct.
“Many low-level analysis operations have been made obsolete, such as the programming of material property subroutines, manually joining different mesh types and mesh elements, and the requirement for interfacing tools that shuffle data back and forth between specialized single-physics codes,” he says.
These improvements have moved both major and minor multiphysics effects further upstream in the design process. DE has scoped out a baker’s dozen of vendors in this field to learn how the power (and accuracy) of multiphysics simulations increasingly applies to today’s applications—and when it may be overkill.
Better Resources, Easier Meshing
Vendors agree that compute power for tackling multiphysics problems has increased dramatically. As Bob Williams, Autodesk product marketing manager for simulation, puts it, “The rise of multiple CPUs, more powerful GPUs and even cloud-based simulation has made hardware resources a non-issue.”
The multi-core architecture of microchips supports hybrid implementations of symmetric multi-processing (SMP) and massively parallel processing (MPP) solvers, enabling memory-demanding applications to take advantage of parallel architectures.
A second breakthrough is the widespread use of automated, adaptive meshing, making the task much less of a doctorate-level job. Time was when a solver for one physics type couldn’t use the mesh created for the second domain—for example, the coarse mesh for a structure vs. the fine surface mesh at a fluid’s boundary layer—but software across the board has made strides that reduce this issue to a lesser part of the simulation process.
“Good mapping tools should allow a seamless data transfer from one physics area to another, and automate the mapping between dissimilar meshes,” says Pierre Thieffry, ANSYS product line manager for structural mechanics solutions. “Additional capabilities, such as scaling, unit changes and orientations to match point cloud data to the current model, are required.”
![]() |
ANSYS software analysis of fluid-structure multiphysics interaction in a biomedical valve, taking into account strongly coupled fluid flow and structural deformations. Image courtesy ANSYS. |
In the past, users had to develop their own algorithms to do so. Now, as Williams adds, there’s no need to know exactly what the mesh looks like ahead of time.
“Just worry about the initial state,” he says. “The software looks at what’s happening during the simulation and adjusts accordingly. The whole idea of the mesh needing to be the same (between domains) is gone.”
Marc nonlinear analysis software from MSC Software has, for a long time, had automatic remeshing capabilities to analyze large-strain structural problems. MSC’s senior product marketing manager, Srinivas Reddy, explains that this capability is highly beneficial when material gets distorted under high temperatures or strains in coupled analyses, or when motion and deformation in electrostatic/structural models displace the air surrounding the piece. The software also offloads users from needing to know where and when contacts will occur with automatic contact boundary detection, which is very beneficial in nonlinear analyses.
![]() |
A direct coupled fluid-structure interaction simulation of a 100m composite blade, using Altair HyperWorks for calculating turbine blade aeroelasticity. Displayed are flow features at different cut planes. Image courtesy Altair Engineering. |
As if meshing between coarse and fine grids wasn’t enough of a challenge, meshing between structural (finite element, or FE) models and fluid (finite volume) models has traditionally been even harder. One solution comes from Altair, whose computational fluid dynamics (CFD) software, AcuSolve, is based on an exclusive FE approach that fully preserves all physical quantities. The gives the solution the advantage of being insensitive with respect to meshes, so coupling the two FE codes is straightforward. This simplifies, for example, solving a structure/heat-transfer/flow problem.
Coming from the CFD side of the industry, CD-adapco has developed an increasing number of meshing technologies specifically suited to certain structural geometry types. As Jean-Claude Ercollaneli, CD-adapco’s senior vice president of product development, explains, “One example is our thin mesher, which automatically detects objects that are thin in nature,” using sheet-metal frames as an example. “Instead of trying to fill them with polyhedral elements, it creates extruded prisms,” he says. “This means that to adequately capture thermal gradients through the thickness of the object, we don’t require a high cell count.”
![]() |
Multiphysics flow simulation of a medical inhaler, performed with NX CAE software from Siemens PLM Software. Image courtesy Siemens PLM Software. |
Coupled vs. Deeply Coupled
Ultimately, analyzing a multiphysics problem is all about the equations. In COMSOL Multiphysics software, all the partial differential equations (PDEs) are combined in a single matrix and solved simultaneously, converging to a single solution (mathematically, the most stable approach). Other packages generally address each physics environment separately, setting up two or more matrices to solve each set of PDEs independently, then passing the results from one matrix to another for closed-loop iteration.
![]() |
An aircraft crashworthiness simulation with fluid structure interaction performed with MSC Nastran Explicit Solver. External airbags are deployed to dampen the shock waves as a result of the aircraft impact on the water, and to act as a floating device to keep the structure above the water. As the shock wave from impact travels through the airbags and to the aircraft, the structural behavior (and possible failure) can be predicted. Image courtesy MSC Software. |
Multiphysics Modeling, Step by Step One way to gain insight into real-world effects is to start with a simple geometry, says Bernt Nilsson, senior vice president of marketing at COMSOL. Surprisingly, that can mean stepping back from today’s 3D world. |
Detlef Schneider, senior vice president for solver products at Altair, acknowledges that weakly coupled interaction seems less stable in theory. “But in practice, we have developed technologies that give us the stability of the strongly coupled code, without its drawbacks,” he says. “Also, having a coupling strategy rather than integrating in one matrix allows you to implement third-party tools in the process.”
Key issues for deciding among fully, strongly or weakly coupled solutions involve understanding several factors, including:
-
how much the solution stabilityaffects speed and accuracy;
the level of influence orinteraction actually taking place (is it one-way, two-way, weak orstrong); and
whether your company’s currentanalysis package can handle your specific situation.
Regarding the last factor, not all multiphysics software addresses, for example, piezoelectric-mechanical interactions, but may be able to do so with a partnership package.
What considerations help users evaluate their choices? Thieffry offers this thought: “The key factor is how much the various disciplines are influencing each other. For a structure immersed in a fluid, if the structure is very flexible, it will impact the fluid flow as it deforms. If it is stiff, the flow around it won’t change, as the structure will not deform much. For the latter, a simple sequential coupling is enough.”
Ravi Shankar, director of simulation product marketing at Siemens PLM Software, voices a similar thought. “In many cases, there is much more calculation overhead in solving one large matrix vs. two smaller ones. Also, separate solvers can be more attractive because one solver cannot be specialized for all physics, and the features (properties) in FE modeling will not necessarily be common between models.”
SIMULIA takes an open platform approach to working with other analysis packages. Karl D’Souza, SIMULIA lead for multiphysics, says that given the increasing complexity of product design today, innovation often requires the ability to explore and connect many disparate physical domains. So, Abaqus supports coupling various aspects of a workflow across multiple physics, as well as with outside software, using a consistent and scalable coupling paradigm. D’Souza adds that from a user perspective, multiphysics analysis would be easier if a fluid could be treated as just another material, so SIMULIA is also working on simplifying the user experience.
A hybrid approach also works for designers who depend on the NEi Software flavor of Nastran. They can call on Siemens FEMAP pre-processing software to set up solver-independent input for many of the standard multiphysics solvers. They then take the results back into NEi Nastran for structural analysis—and lastly, add coupled convection and fluid flow analysis using the TMG Advanced Thermal module from MAYA HTT.
What Do You Really Need?
Adding multiphysics analysis can certainly improve designs, but good engineers learn when to use it and how much.
“I believe one of the biggest advances of the past few years is the awareness that multiphysics is a difficult subject that still presents large limitations in some areas, and that models have to be carefully designed to obtain realistic answers,” says Livermore Software Technology Corp. (LSTC) scientist Facundo Del Pin. “Solving a monolithic system of linear equations that contains all the physics is definitely the most robust way, but sometimes it could be like using a sledgehammer to crack a nut.”
Vipul Kinariwala, Cranes Software NISA product manager, sees a frequent need for working with two coupled fields such as EM-heat transfer, thermal-mechanical and fluid-structure, but not so much call for three-way combined physics.
“In the real world, you can get away with a lot even if you don’t do a fully coupled ]two-way] analysis,” he says. “Take the two extreme conditions, apply them to your mechanical model and use your engineering knowledge and experience. For most cases, this is good enough.”
In other words, don’t do analysis for the sake of analysis.
Pushing New Limits
The multiphysics capabilities of these vendors continue to evolve to more accurately model coupled physics, whether applied to microfluidics, micro-electro-mechanical systems (MEMS) devices or rotating machinery. Check out Altair HyperWork’s use of extended finite elements (X-FEM) (good for modeling windshield cracking) and CD-adapco’s expansion of its CFD analysis capabilities into a full CAE tool. An example of the latter is the integration of discrete element modeling (DEM) into CD-adapco’s STAR-CCM+ package. This combination lets users study solve both the fluid behavior and DEM fields of, for example, a “stream” of pills, corn kernels and even tumbling gummy bears in a manufacturing/processing environment.
![]() |
Dynamics of a re-entry vehicle impacting water at 30 ft./sec. The simulation consists of one structure (the capsule) and two fluids (air and water) whose interactions are captured in a single Abaqus FE model using the Coupled Eulerian-Lagrangian (CEL) technique to handle the highly discontinuous contact and free surface conditions. Image courtesy SIMULIA. |
Siemens PLM offers examples of acoustic structure modeling and smoke (multi-species dispersion) simulation. ESI Group has spent years working on fuel cell design capabilities in its CFD-ACE+ multiphysics suite, and COMSOL recently added a corrosion module to its primary analysis package.
NAFEMS 2012 North America Conference NAFEMS 2012, “Engineering Simulation: A 2020 Vision of the Future,” takes place Sept. 11-12 in Washington, DC. Learn more. |
MSC Software makes a strong case for the multiphysics power of MSC Nastran for modeling tire hydroplaning (involving nonlinear tire material, steel belts and a thin film of water). And ADINA Multiphysics can analyze the coupling between pore pressure and deformation of a porous material comprising bone, muscular tissue and fluids.
All this expanded power has convinced more engineers to apply multiphysics analysis to even more problems. A recent posting on LinkedIn’s CFD Group asked for advice about simulating the heating, mass transfer and shrinkage of food cooking in a microwave oven—a task requiring a solution that handles a moving mesh. That designer is fortunate to have a wealth of choices for everyday multiphysics solutions; you may find it’s time to join the crowd, too.
Contributing Editor Pamela Waterman, DE’s simulation expert, is an electrical engineer and freelance technical writer based in Arizona. You can send her e-mail to [email protected].
More info
More Livermore Software Technology Corporation Coverage
Subscribe to our FREE magazine,
FREE email newsletters or both!Latest News
About the Author

Pamela Waterman worked as Digital Engineering’s contributing editor for two decades. Contact her via .(JavaScript must be enabled to view this email address).
Follow DE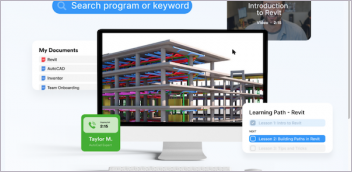

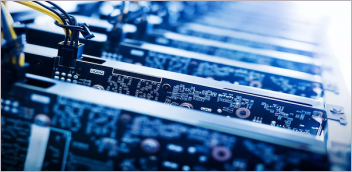
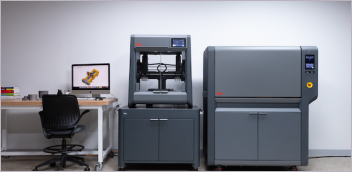