Latest News
March 1, 2011
By Kenneth Wong
Asking a small business to adopt a product lifecycle management (PLM) system is like asking a neighborhood baker to install an industrial oven, complete with conveyor belts, control knobs, and a walk-in heat chamber. What he needs is a countertop oven, small enough to fit on the oak table in his kitchen, large enough to churn out several batches of breads and pastries to keep up with morning and lunch rushes. He refuses to read a 2-in.-thick installation manual just to get started. He believes the equipment should be ready once plugged in. As for configurations, he asks for but four settings: On, Off, Temperature and Timer.
![]() SolidWorks n!Fuze, a web-based file sharing and collaboration function from Dassault Systèmes, is aimed at teams as small as two. |
In the late 1980s and early ’90s, PLM projects were often data consolidation initiatives undertaken by the GMs and Boeings of the world. It was assumed—correctly, I might add—that only manufacturing titans of such size and magnitude would engage in parallel product development (subcomponents that must eventually fit together and were in development in different places, overseen by different teams). Only they would need to tackle the complex data-management issues arising from this practice.
Thus, for a time, most PLM technologies were the software equivalent of industrial ovens. Like its equally intimidating cousin enterprise resource planning (ERP), early PLM came with a 2-in.-thick manual, a team of consultants and a hefty price tag.
Arena Solutions, one of the earliest PLM applications delivered in the Software-as-a-Service style, lets you monitor your project status in a dashboard. |
But today, in what New York Times columnist Thomas Friedman calls the “Flat World,” small and midsize businesses (SMBs) can compete with large enterprises in a playing field already leveled by technology. In the era of digitized, wired communication, small manufacturers from Taipei, Pune or Minnesota can bid for the same jobs on which their larger counterparts are bidding.
What is PLM? Ever since its creation in the late 1980s, product lifecycle management (PLM) has had to go through a series of identity crises. Preached by many, yet understood by few, the concept grew more abstract over time. According to CIMdata, an analyst firm, PLM is a strategic business approach that: • applies a consistent set of business solutions that support the collaborative creation, management, dissemination and use of product definition information; • supports the extended enterprise (customers, design and supply partners, etc.); • spans from concept to end of life for a product or plant; and • Integrates people, processes, business systems and information. The same analyst firm warns that “PLM is not a definition of a piece, or pieces, of technology. It is a definition of a business approach to solving the problem of managing the complete set of product definition information—creating that information, managing it through its life, and disseminating and using it throughout the lifecycle of the product.” |
With lower overhead, smaller firms can—and often do—underbid the larger ones. The opportunities once confined to bigger firms are now within their reach. Consequently, so are the product-development complexities once limited solely to bigger firms. The question among progressive SMBs is this: Is there a countertop oven version of PLM?
Getting Your Data House in Order
By its very nature, PLM is an ambitious undertaking, involving concept development, design creation, data management, collaboration, simulation, manufacturing, compliance and—if you choose to extend the lifecycle beyond manufacturing—post-sale maintenance.
With the exception of certain tier-one companies, there aren’t many manufacturers sufficiently resourceful in finance, time and manpower to adopt a series of technologies that address all aspects of PLM in a single shot. Most likely, companies tackle these issues one at a time, or a few at a time, depending on priority and affordable downtime.
“I think that many large enterprises have additional requirements for a PLM system that are needed just due to the size of the company,” says Michael Distler, director of solutions marketing for PLM tool manufacturer PTC. “For example, requirements management for an SMB may be easily managed by one person using a simple vault tool, since there are a fairly finite number of requirements to keep track of. But the large enterprise may have thousands of requirements that would be unwieldy or impossible to effectively manage and cross-reference without a PLM system. Because these additional capabilities result in a larger system that needs to be configured and maintained, the SMB may not have the resources to manage such a large system.”
Many vendors offer software suites—a collection of interoperable, associative software programs—to manage different aspects of the product lifecycle. For PLM beginners, the best place to start may be data management and collaboration.
“I think simply having a single, secure, accessible place to store all product-related files is probably the most important capability for an SMB,” Distler says. “After that, I would say simple change and configuration management, such as keeping track of the latest version, etc. Collaboration would be next, given that many SMBs work with independent contractors for a particular job.”
SaaS-sy PLM
In the last five years, as people have begun to feel more comfortable with the idea of remote software, often called Software-as-a-Service (SaaS), certain PLM programs have sprung up on the same platform. If what you need to manage is the most basic of your manufacturing documents—your bills of materials (BOM)—you could do it for as little as $99 a month. Arena Solutions, founded in 1994, specializes in delivering SaaS BOM management functions. The product, called Arena, was an outcome of the co-founders’ own frustration with their homegrown data-management efforts in Excel spreadsheets in their previous career as manufacturers.
Do You Need PLM? For determining whether a business needs help with product lifecycle management, you should pay less attention to revenues and number of employees, but more to the complexity of the workflow and products involved. • Does the business have a geographically dispersed team and workflow? • Does the business engage in parallel product development activities (in other words, subcomponents that must eventually fit together are in development in different places, overseen by different teams)? • Do project managers have a hard time determining the statuses of different components? • Do engineers and designers have a difficult time locating the files they need? • Does the business risk making costly mistakes resulting from outdated data? If the answer to some, most or all of the questions above is “yes,” the business may benefit from some lifecycle management practices, implemented in conjunction with affordable, low-maintenance PLM software. |
Arena includes features for BOM management, change management and supplier collaboration. SaaS deployment means you don’t need to keep and maintain an IT infrastructure. You access Arena features and your uploaded data from a standard browser.
Arena’s look and feel still reflects its original point of departure, Excel. Rows and columns, an approach that does a fine job managing textual and numeric data, may be sufficient for many, but the new model-driven data-management approach, as exemplified by Siemens HD PLM and Autodesk Vault, shows that a greater integration between product data (part numbers, BOMs, release dates, and so on) and product design (CAD files) could yield PLM insights otherwise unavailable.
Playing Well with Others
“We understand that we’re not going to be the only tool that our customers use,” Chuck Cimalore, CTO of Omnify Software, states. “Where we excel, in addition to the breadth of our functionality, is in our ability to turn around the system—get customers up and running quickly in a very cost-effective package.”
Omnify concentrates on SMBs, from startups to those with $500 million in annual revenues. Its PLM software suite includes BOM management, change management, quality assurance, project management, compliance and more. Omnify’s CAD integration lets you access your product data directly from within your modeling environment in partner products like SolidWorks and PTC’s Creo Elements/Pro (formerly known as Pro/ENGINEER).
Cimalore reveals it often takes new customers only three to four days to be up and running.
The Big Three
The holy trinity of PLM—Dassault Systèmes, PTC and Siemens PLM Software—used to focus on industry titans, with comprehensive software suites like ENVOVIA (Dassault Systèmes), Windchill (PTC), and Teamcenter (Siemens). But the allure of the SMB market beyond tier-one manufacturers proved irresistible.
Dassault Systèmes tackled this segment with SolidWorks Workgroup PDM, offered alongside its midrange CAD program SolidWorks. PTC recently made the decision to reshuffle its products, breaking up Pro/ENGINEER, Windchill and other titles into a series of applications with smaller footprints. Siemens put together its midrange PLM bundle called Velocity Series. At the heart of it was Teamcenter Express, a lighter version of Teamcenter.
Recently, Dassault Systèmes moved further down the SMB market, attempting to capture the smallest of PLM users—teams as small as two—with a web-based file sharing and collaboration plug-in called n!Fuze (see Virtual Desktop, page 9). Though the product is based on its enterprise PLM system ENOVIA, the user interface looks more like an instant messenger window, reinforced by social media-inspired chat-and-comment functions. The plug-in, which appears as an unobtrusive tab in SolidWorks, lets you create a personal workspace where you can upload a design in progress, invite a collaborator, then start a discussion.
“What designers and engineers don’t like,” notes Omnify’s Cimalore, “is for someone to come to them and say, ‘Hey, we’ve implemented this new PLM system, so you’re gonna have to use it.’”
That, perhaps, is a challenge shared by all PLM providers, large and small. The ghost of enterprise software still haunts many. Only a new breed of lightweight, pain-free PLM products can wipe away the memory of implementation horror.
“PLM solutions have historically been notoriously difficult to implement,” he says. “They’re not short-term solutions, not very malleable, so you can’t change them easily. An SMB has limited bandwidth for software maintenance, IT maintenance and customization. So a solution for the SMB has to be easy and practical, with immediate return on investment and a low entry barrier.” It doesn’t necessarily mean low cost, he adds, just that they have to start paying back the investment quickly. Because of their low costs (around $100 per seat per month) and low overhead (little or no IT investment), Software-as-a-Service (SaaS) or web-hosted PLM solutions often strike SMBs as attractive alternatives. Behrens advises buyers to consider certain factors: • How do you get your information in and out? “SaaS gets rid of the IT maintenance burden, but it also brings with it another problem: Transferring information ]in and out of the program] can be quite costly,” he says. Whether delivered online or on the premises, if the PLM software forces you to significantly recalibrate your workflow and practices, it could be an inhibitor to adoption, he cautions. |
More Info:
Arena Solutions
CIMdata
Dassault Systèmes
Omnify:
PTC
Siemens PLM Software
Taxal
Kenneth Wong writes about technology, its innovative use, and its implications. One of DE’s MCAD/PLM experts, he has written for numerous technology magazines and writes DE’s Virtual Desktop blog at deskeng.com/virtual_desktop. You can follow him on Twitter at KennethwongSF, or email him via [email protected].
Subscribe to our FREE magazine,
FREE email newsletters or both!Latest News
About the Author

Kenneth Wong is Digital Engineering’s resident blogger and senior editor. Email him at [email protected] or share your thoughts on this article at digitaleng.news/facebook.
Follow DE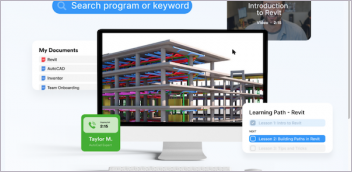

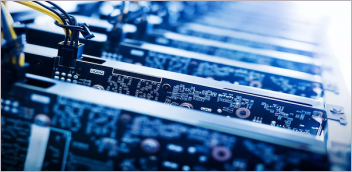
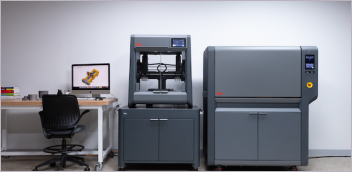