Latest News
September 1, 2005
By Louise Elliott
Although many PLM systems come from companies that started out as CAD developers, others got started with PDM cores or with sourcing and supplier management bases. The design-based systems still include many engineering authoring tools, while the others grew into stand-alone PLM offerings. Two of the best known companies in the latter group are MatrixOne and Agile—both of which have customers who shared some of their PLM experiences for this story.
The two applications offer a study in contrasts regarding PLM needs and uses. One is a very large enterprise—with well established IT—that needed a single tool to unite diverse programs and business processes in 43 worldwide locations. The other is a mid-sized company—well versed in complex electronics but with little IT experience—that needed to blend military and commercial lines of business.
Agilent Technologies
When Hewlett-Packard spun off its test and measurement divisions in 2000, forming Agilent Technologies, the new company undertook many business changes. According to Betty Capozzoli, strategic program manager, “much of the transformation took place around IT.”
Agilent had a great many PDM systems already in place, as well as change management, document management, and several CAD tools (Mentor Graphics for ECAD design, OneSpace Designer for MCAD, and an “in-house solution” for radio frequency and other specialized designs).
The company wanted PLM to replace the multiple PDM systems and interface with the design systems—and to bring in collaboration both internally and with suppliers. Deployment was complicated by the simultaneous implementation of an Oracle ERP system. Together, Agilent wanted the two systems to provide a single enterprise solution for 43 global locations. “We found MatrixOne attractive because it’s CAD-independent, scalable, and has the flexibility to create an integrated system with the many tools we used,” says Capozzoli. “It automates the load of bills of material (BOM) from our non-standard design tools as well as working with standard programs.”
|
This screenshot of an engineering change order is easily accessible from MatrixOne’s Engineering Central. |
Agilent used MatrixOne’s Engineering Central and Supplier Central “out of the box, with very little customization, because we preferred to rework the business processes feeding into the system—something we needed to do anyway,” she says. “We experienced the toughest part of getting up and running in normalizing data—that is, cleaning it up so that everyone used the same nomenclature conventions for the migration.”
Capozzoli explains that Agilent did a phased implementation starting with five key sites over a period of about six months, starting with “current rev, minus one,” and leaving older designs that might be needed again as discrete items in outside archives. At one of the first sites, the MatrixOne implementation replaced five different PDM tools. The implementation today incorporates all 43 sites. The system is centrally located at headquarters in Colorado Springs, with a backup located in another Colorado location. Multiple file collaboration servers around the world connect international employees and suppliers.
“MatrixOne has a central enterprise core with nine or ten application areas, including Engineering Central, Supplier Central, and Sourcing Central,” says Sam Zawaideh, MatrixOne’s senior vice president for product solutions and customer support. “The common components in the core make it easy to integrate the various applications as Agilent has done. The core has an application layer that makes it possible for users to integrate it with CAD, ERP, and so on.”
Zawaideh says that users can either install the system and run it as is, or change the look, feel, and data model to suit themselves. “The core of the system has dynamic modeling capabilities for PLM applications, providing connectivity so that users don’t have to write programs to the APIs,” he says. “Agilent wanted to be able to include suppliers in product development and decision-making processes—and MatrixOne’s flexibility allows suppliers to work directly with the system.”
|
Quality engineers have many viewing options, from reviewing a list of WBS tasks across for supplier-submitted deliverables to reviewing RYG status using various filters. |
The system makes it possible for companies to apply process-specific attributes for vertical industries. For example, a Specification Central is adapted for consumer goods. Managers can access dashboards that let them see what’s happening in their areas. “Over the past three years,” says Zawaideh, “we’ve shifted our focus from providing a customizable toolkit to being an application provider with a system that works like Lego blocks.”
ViaSat Inc.
ViaSat, an 19-year-old company headquartered in Carlsbad, CA, started out by building very complex satellite communications systems for the military. It later expanded into commercial applications and products, acquired three other companies in that arena, and today its products, from compact data controllers for office networking to military aircraft tracking systems, are evenly divided between the two markets.
|
Agile’s hosted PLM system aims to track the entire enterprise product record, depending on a customer’s wishes. |
Although the company does some product assembly in Carlsbad and Atlanta, it relies primarily on more than 50 contract manufacturers scattered around the US for actual manufacturing. When ViaSat wanted to grow the company and extend its ability to work collaboratively with its network of contract manufacturers, it went looking for a tool that would make it easier for the various divisions and their manufacturing contractors to work together as well.
ViaSat chose an Agile-hosted PLM solution with local file servers in each of its four primary locations. Brandon Johnson, director of engineering services, says, “The central hub includes a component database that makes it possible for our electrical engineers to select components and drop them directly into their schematics. It also includes all change management and document management functions.”
The company was up to speed in three and half months, with a few training sessions, he says, suffering pain only from adjusting to a new system. “We now have 750 users, including more than 50 contractors. We use Agile Product Collaboration for better visibility and control of the product record across the lifecycle. We are installing Agile’s closed loop corrective action system to help drive product quality and its product governance and compliance system to automate Recycling of Hazardous Substances (RoHS),” Johnson says.
|
Agile’s BOM and Documents tracker allows users to review data of individual parts as well as the entire history of the project’s workflow. |
He also reports that within six months, ViaSat experienced a 44% gain in efficiency from the initial design to completion of a product prototype, a 20% improvement in engineering change orders, and a 30% improvement in overall organizational efficiency.
Agile believes scalability to be one of its greatest strengths, says Ray Hein, vice president of product strategy. “ViaSat’s application is typical of medium size business PLM needs. Agile can provide systems, whether hosted or enterprise-based, from just a few to 10,000 seats.”
A basic differentiation point for Agile is its intent to be a provider of an enterprise business process, and in fact, the company calls the overall system the Enterprise Product Record. It can include tools for concept, design, sourcing, manufacturing, selling, service, and disposal, with executive dashboards for the various capabilities, starting with portfolio management.
PLM analytics play a part in the Agile offerings, says Hein. “These include project and program on-track and off-track analysis; particularly as pertains to tracking goals and dates, so that users can see where the project is.”
As Johnson of ViaSat mentioned, another analytical tool is quality analytics linked to customer support and service. “We call this Product Service Improvement, or PSI, and it brings problems detected by users into PLM so that the company can access and determine where the problem occurred—in manufacturing or in outsourced parts, for example—see trends regarding quality issues, and fix them within today’s compressed design cycles.”
From these applications and application-provider input, it appears that as interest in PLM grows, suppliers of the technologies involved are making the systems easier, faster, and more beneficial to deploy.
Contributing Editor Louise Elliott is a freelance writer based in California. Offer Louise your feedback on this article through e-mail by clicking here.
Product Information
Agilent Technologies
Colorado Springs, CO
Agile
San Jose, CA
MatrixOne Inc.
Westford, MA
ViaSat
Carlsbad, CA
Subscribe to our FREE magazine,
FREE email newsletters or both!Latest News
About the Author

DE’s editors contribute news and new product announcements to Digital Engineering.
Press releases may be sent to them via [email protected].
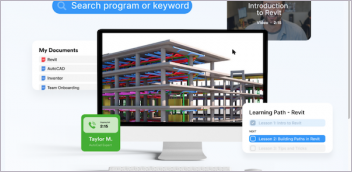

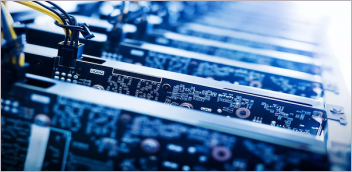
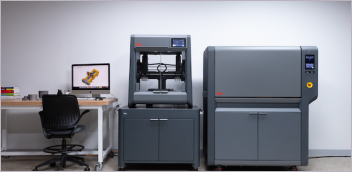