Latest News
May 1, 2012
By Pamela J. Waterman
Good. Better. Best. You often see these terms on product families ranging from carpeting to computers. The choices span options including price, performance, durability and visual appeal. But in many ways, this phraseology also captures the vision of a typical engineering design sequence—except that the process generally stops at “better.”
Product R&D schedules leave little time for finding the design that goes beyond “better” to “best.” Robert Ryan, president and CEO at Red Cedar Technology (developers of HEEDS MDO optimization software), says that typically, “with CAE models, once you prove they’re pretty good, you tweak the design within the design space near what you’ve already done, and do a little better. Rarely have designers gone for dramatic improvement.”
![]() |
Workflow example for VisualDOC multidisciplinary optimization software, showing graphical user interface to set up, execute and automate a design optimization process. Image courtesy of Vanderplaats Research & Development. |
To do so requires a methodical optimization process that searches among alternative designs, but a manual approach is time consuming and even an automated design-of-experiment (DOE) approach may miss an opportunity in the big picture.
Garret Vanderplaats, founder and CEO of Vanderplaats Research & Development (VR&D), an optimization software company, says that DOE tends to focus on individual parameters—yet valid design explorations require a systematic search process that emphasizes promising regions in the design space.
Designers often strive to tweak a design to give the best performance for a few critical conditions, ignoring the issues of real-world manufacturing variation (such as geometric variation) and operational variation (such as temperature variation).
“Today, the challenge is not so much finding the global optimum, but the robust global optimum,” notes Alex Van der Velden, director of Design Automation Products at SIMULIA. “Many optimization methods push the design against the failure limits, so even small operational variations would lead to failure. If a product design is based on a robust global optimum, such a product is insensitive to variations. This is the definition of product quality.”
Optimizing, say, just for structure gives different answers than optimizing a part for cost. Tackling this multi-faceted problem demands software for multidisciplinary optimization (MDO), whose beauty comes from the ability to automatically evaluate hundreds—or thousands—of design combinations.
Many finite element analysis (FEA) and computational fluid dynamics (CFD) analysis packages offer some type of optimization tool, such as in MSC.Software’s MSC Nastran; the Design Study Environment in Autodesk Simulation CFD (formerly known as CFdesign); and the NISAOPT module for NISA Mechanical design/analysis software. However, the past several decades have also witnessed the development of generalized, standalone optimization packages.
These tools apply optimization to the design parameters and functional results of pretty much any analysis software—whether structural, fluid dynamics, chemical or financial—as well as to any task, from minimizing weight to maximizing cooling, to predicting the probability of part failure. Much of the power of these standalone solutions lies in their ability to link together multiple analysis tools for a single product design, and optimize the product across broad performance characteristics.
Power Players
Part of the reason optimization is not done more often is that few people teach it in the first place. Even so, according to Vanderplaats, it tends to be taught as applied math, not engineering design, and then only at the graduate level.
Vanderplaats certainly knows his field: In the early 1970s, he developed an optimization code, CONMIN, that is still widely used. In the late 1980s, his company developed the optimization capability for MSC Nastran. And in the early 1990s, VR&D wrote its own GENESIS software that was “a little FEA and lots of optimization,” but today is quite a bit of both. Along the way, he created a general-purpose, multidisciplinary optimization product, COPES, which is now a VR&D package called VisualDOC.
![]() |
Safety-design optimization of side impact for an automotive passenger compartment, performed with HEEDS MDO software. The HEEDS optimized design met all constraints—while reducing the mass of the safety cage by 23%. Image courtesy of Red Cedar Technology. |
VisualDOC’s capabilities include optimization, DOE, response surface approximations and probabilistic (robust and reliability-based) optimization. It can be used to add these capabilities to almost any analysis program. Its optimizers are also used by GENESIS, and can handle more than 2 million variables. GENESIS includes second-generation, physics-based approximations that are more accurate than gradient linearization—and generate an optimum structural design for the cost of about 20 FEAs.
SIMULIA, the Dassault Systemes brand for realistic simulation products, markets both Abaqus nonlinear analysis software and Isight design optimization and process automation software. Since its acquisition in 2008 from Engineous, Isight has been continually enhanced (now at version 5.6), and offers direct interfaces that support more than 30 FEA and CFD applications, along with Excel and ASCII files. Much of the user interface is visual drag-and-drop, and results can be viewed in real time.
Van der Velden says that Isight gets designers out of their “thought-ruts. It doesn’t ‘know’ you’re designing an airfoil or a beam,” he says. “It just takes the inputs it’s given, and drives a solution toward the objectives of the design challenge. Because an optimization algorithm has no preconceptions about results, it may very well give you answers—like an unexpected shape or thickness—that are completely different from what you envision. And they just may be better answers.”
Van der Velden recommends using Isight to automate DOE first because it’s a simple way to get a handle on understanding what’s important in the problem. To find the best dimensions for a part, for instance, Isight can combine and extrapolate results from 50 Abaqus runs to create a curve between the points, filling in expected response values for additional input values. Users can employ graphic “sliders” to see, in real time, the effects of changing up to eight dimensions at once. Isight will then perform a Six Sigma optimization to predict the probability of meeting a certain value (stress, for example), given variations in another factor (material thickness, for example).
Red Cedar Technology’s HEEDS MDO software also performs process automation, design optimization, DOE and robustness/reliability calculations. Ryan notes that optimization tools have traditionally asked users to choose one of a dozen optimization algorithms, plus dozens of tuning parameters—tasks that generally required a doctorate to successfully complete.
HEEDS MDO eliminates this complexity by providing a default search method called SHERPA. This hybrid process uses multiple search strategies simultaneously, and dynamically adapts to the problem as it learns about the design space. Users define the objective of the study, then just specify the parameters to be varied, the fixed constraints and the number of desired iterations. HEEDS does the rest.
Because automation can have its dark side, Red Cedar Technology has made sure that its optimization process is not a “black box.” Users are encouraged to view a run’s progress and results, and change the direction in real time if the engineer’s intuition prompts a move in a different direction as results unfold. The software offers direct input/output portals for Abaqus, Adams, ANSYS Workbench, Nastran, LS-DYNA, Moldflow, SolidWorks, Excel and NX (input only). Generic interface links also connect to any ASCII format file.
Collier Research HyperSizer software applies optimization techniques to metal and composite structures for weight, strength and durability, with strong support for certification procedures. The software targets designs for aerospace, wind blades, commercial and military aircraft, high-speed rail and ship-building, and creates what company president Craig Collier calls “a level playing field for all the possible design candidates.”
HyperSizer Pro imports FE models as well as FEA-computed loads. Using non-FEA failure methods, the software analyzes and quantifies safety factors, and eliminates negative margins of safety for thousands of mechanical and thermal load sets. It then optimizes to determine the lightest weight combination of material systems, cross-sectional dimensions, and ply layups for all panels and beams in the structure, and automatically iterates with FEA for load convergence.
“What industry wants,” says Collier, “is not necessarily to let (the optimizer) run overnight, and come back in the morning. The software needs to expose what’s going on and be interactive.”
He says a critical aspect for today’s large designs is that teams work independently, but must be able to bring all the subsystem designs together and have them be manageable for evaluating throughout the design process.
Next month, in part two of DE’s design optimization coverage, we’ll explore other contributors to this field, including Sigma Technology, ESTECO Phoenix Integration, Optimal Solutions Software and Openeering.
Contributing Editor Pamela Waterman, DE’s simulation expert, is an electrical engineer and freelance technical writer based in Arizona. You can send her e-mail to [email protected].
Design Optimization 101 Designers can apply optimization techniques to a single discipline (structures or aerodynamics, for example) or a multidisciplinary problem (structures plus aerodynamics plus propulsion plus control-theory plus economics, for example). A good introduction to the subject can be found in a presentation by Il Yong Kim of the Department of Mechanical and Materials Engineering, Queen’s University, Ontario, Canada, at The process requires formulating the problem, then choosing and implementing a computational solution. Here are some of the general components involved: Simulation process flow: User-defined workflow of simulations and analyses to be performed, including task order, software tool selection and data transfer. Models: Each analysis in the process flow requires a specific analytical or empirical model and representation. These models connect inputs, such as design variables and parameters, with output variables representing some measure of system performance. Random variables: Parameters that are subject to variations due to chance, including manufacturing variation, material variation and operational variations such as the ambient temperature of an electrical circuit or the wind loads on a vehicle. Design variables: Specifications the designer can control, including physical dimensions, material choice, and parameters such as the number of blades in a turbine. Design objectives: User-defined performance characteristics to be maximized or minimized, such as fuel efficiency or mass. Constraints: Typically, these are performance characteristic levels that need not be maximized or minimized, but must be kept above or below a certain level. Solutions: Optimization algorithms combine the design variables, constraints, objectives and models to find possible sets of values that satisfy the defined problem. The software automatically feeds these values back to the appropriate analysis software packages for a new round of evaluation. Users choose the number of iterations to try, and specify what conditions define convergence. The different optimization solutions fall into several categories (listed with a sample type): gradient-based (feasible directions), gradient-free (Hooke-Jeeves pattern search), population-based (genetic) and various others (simulated annealing and indirect optimization based on self-organization, or IOSO). Some work better than others on certain applications, and different packages may use different subsets. Improvements in HPC resources have definitely helped speed up calculations—and opened the door to parallelized functions.—PJW |
MORE INFO
Autodesk
Collier Research
MSC.Software
ESTECO
NISA Software
Openeering
Optimal Solutions
Phoenix Integration
Red Cedar Technology
Sigma Technology
SIMULIA
Vanderplaats Research & Development
Subscribe to our FREE magazine,
FREE email newsletters or both!Latest News
About the Author

Pamela Waterman worked as Digital Engineering’s contributing editor for two decades. Contact her via .(JavaScript must be enabled to view this email address).
Follow DE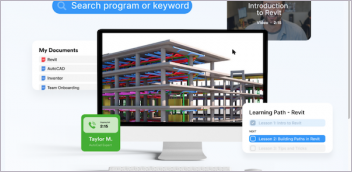

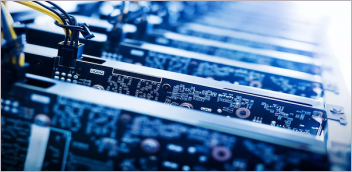
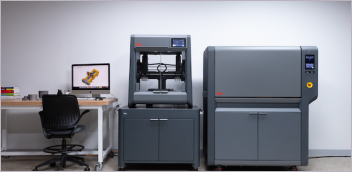