Optimize Sheet Metal Forming
Latest News
September 22, 2015
Dear Desktop Engineering Reader:
If you're a do-bee in industries like automotive, aerospace, consumer electronics, appliances and renewable resources, you likely know or use one or all of the applications in ETA's (Engineering Technology Associates) Inventium Suite of modeling and post-processing software. A key member of the applications suite, the DYNAFORM die system simulation analysis solution is now out in release 5.9.2.1. Today's Check it Out link takes you to a landing page on DYNAFORM and details on a fascinating new module called the Optimization Platform (OP). More on OP in a minute.
DYNAFORM simulations help you predict die-forming details during the design stage. This can be material usage, scrap and piece price as well as cracking, wrinkling and spring-back. This newest release offers new add-ons for trim line development, rotary tube bending design and analysis, hot forming and die structure cooling. Also included are two new modules, D-Eval (Die Evaluation) for analyzing CAD-based engineering designs and OP.
Enhanced with Red Cedar Technology's HEEDS/Sherpa optimization search engine, the OP module brings DYNAFORM functionality for optimizing sheet metal forming. So, what's in it for you?
First, using OP means that your metal-stamping analyses do more than identify problem areas. OP simulations search for the best possible solution to problem areas. What that means is you use your production constraints as guidelines to find the ideal values for specified variables. OP takes this data, optimizes drawbead rates and updates the database automatically.
Second, OP-extended DYNAFORM should help you improve performance and quality by reducing effects like wrinkling, thinning and tearing. It should also streamline your die design process by enabling you to make parts formable quickly and efficiently, which should cut down on manufacturing times and costs.

Almost a year ago to date, this column looked at ETA's optimization led and performance-driven design process called ACP (Accelerated Concept to Product). As much a philosophy as it is a process, ACP unites CAD, CAE and computer-aided optimization to determine the most efficient design solution for some object under development, be that a lone component, subsystem assembly or something as large as a full vehicle. OP technology extends the ACP methodology for sheet metal manufacturing optimization.
To learn more about DYNAFORM and download a complimentary evaluation copy, hit today's Check it Out link. When you land there, scroll down to the bottom of the landing page and hit the Optimization Platform link. Fascinating stuff.
Thanks, Pal. – Lockwood
Anthony J. Lockwood
Editor at Large, Desktop Engineering
Subscribe to our FREE magazine,
FREE email newsletters or both!Latest News
About the Author

Anthony J. Lockwood is Digital Engineering’s founding editor. He is now retired. Contact him via [email protected].
Follow DE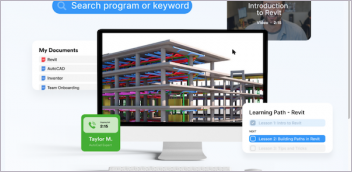

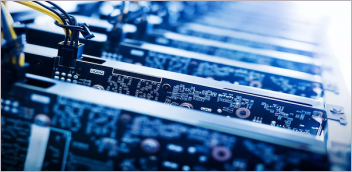
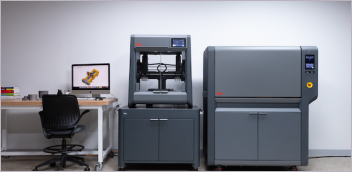