Optimize Bioreactors Quickly with Cloud-based HPC

Engineers use response surface methodology (RSM) to understand bioreactor performance. Image courtesy of ANSYS via UberCloud.
Latest News
October 22, 2018
By Sravan Kumar Nallamothu and Wolfgang Gentzsch
Bioreactors are at the heart of every pharmaceutical manufacturing process. One goal of a bioreactor is to operate at process conditions that provide sufficient oxygen to the suspended cells. Without this, the cells will not be able to perform efficiently.
The performance of a bioreactor is typically characterized by establishing what is called the “design space,”, which defines the relationships between the various input and output parameters of the cell culture. This knowledge is then used to establish and maintain consistent process and product quality during day-to-day operations.
A design of experiments (DOE) approach is recommended to develop a response surface that characterizes the interdependencies between tank design and process operating conditions. This can be an expensive and time-consuming exercise to perform in the lab, especially at manufacturing scale. As such, the pharmaceutical industry has adopted computational fluid dynamics (CFD) modeling as a cost-saving option.
However, the compute resources and simulation time required to explore the relationships between various process parameters can be quite extensive. Therefore, this case study reviews the use of high-performance computing (HPC) to speed up these simulations in a cost-effective manner.
Reduce the Computational Time of Simulation Projects with Cloud Computing
Cloud-based HPC offers the computing power of numerous cores to a simulation project. This will reduce the total time required to execute DOE, as each simulation’s computational time is considerably reduced.
UberCloud offers cloud-based HPC as a Software-as-a-Service (SaaS) that is tailored for computer-aided engineering (CAE) software like ANSYS simulation products.
How to Simulate a Bioreactor in ANSYS Fluent
Engineers can simulate the water and air present in the bioreactor using the Eulerian multiphase model in ANSYS Fluent.
A population balance model with quadrature method of moments (QMOM) simulates bubble coalescence and break up.
Using this approach, the CFD simulations can predict the overall gas distribution and the distribution of bubble sizes throughout the tank, which are key to determining the bioreactor’s mass transfer rate.
The mixing tank simulations were run using the UberCloud platform in the Microsoft Azure cloud data center in Singapore because the engineer, Sravan Kumar, is working in Pune, India. Fluent showed linear scalability on UberCloud throughout the study of the bioreactor.
Each simulation — running on 168 cores in the cloud — took less than an hour to solve (vs. a week on a typical workstation). As a result, the whole design space took less than half a day to compute.
The next step employed ANSYS DesignXplorer to generate the response surface. In this example, the response surface defines the relationship between the mass transfer coefficient, agitation speed, and gas flow rate within the bioreactor.
The results show that combining UberCloud with Fluent and DesignXplorer streamlined the process of characterizing the bioreactor. This setup also reduced simulation time without investing the entire development budget on HPC.
More Simr Coverage
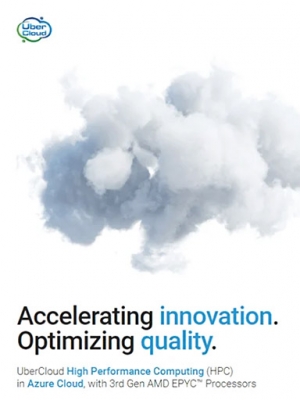
For More Info
To learn more about how UberCloud can speed up ANSYS products, click here. For the complete bioreactor case study, click here.
Sravan Kumar Nallamothu is a senior application engineer at ANSYS. He specializes in modeling mixing in stirred tanks and gas-liquid multiphase flows. Modeling mass transfer in sparged bioreactors and gas-liquid multiphase flow regimes in pipelines and other process equipment are his applications of interest.
Wolfgang Gentzsch is the President and Co-founder of UberCloud, a cloud technology and services provider of fully automated engineering application software containers for any public and private cloud computing resource.
Subscribe to our FREE magazine,
FREE email newsletters or both!Latest News
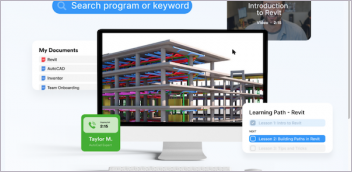

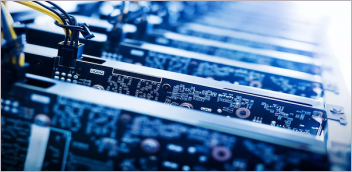
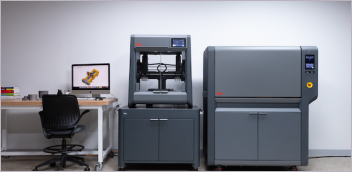