Latest News
August 15, 2012
By DE Editors
OPEN MIND Technologies has released a new version of its hyperMILL CAM solution. Highlights of the 2012 version include automatic programming options for rectangular pockets, optimizations for 3D roughing and new strategies for 5-axis machining of impellers and blisks. Other changes improve calculation times and programming times, the company says.
The new adaptive pocket machining mode allows for automatic programming of rectangular pockets. Within a machining job, classification occurs automatically in closed and open pockets and rectangular levels. According to the various accessibility conditions for the tool and relative sizes of the tool and pocket, hyperMILL automatically selects the most suitable machining method: spiral, contour-parallel or peeling.
During 5-axis shape offset machining with hyperMILL, users now avoid redundant movements thanks to the new axial sorting option that makes it possible to divide machining by area. This allows corners or pockets, for example, to be machined individually one after another. The user can decide whether to create toolpaths with offset level sorting or axial sorting.
There are also several new features for roughing in the 5-axis impeller and blisk package. For machining of impellers, it is now possible to divide the machining region into a left and right pocket between the main blade and the splitter. This new option means that these areas can now be machined with different tools in a targeted manner.
The flank mode during roughing enables swarf cutting near blade surfaces. The user can decide whether to use the swarf mode for every step or just for the last step. This extension results in a consistent stock allowance for finishing. Production time can also be reduced here as preliminary finishing can be skipped.
hyperMILL 2012 supports tapered tools for 3D ISO machining, including automatic collision avoidance. In the process, the entire tool is checked for collisions against the model.
For more information, visit OPEN MIND Technologies.
Sources: Press materials received from the company and additional information gleaned from the company’s website.
Subscribe to our FREE magazine,
FREE email newsletters or both!Latest News
About the Author

DE’s editors contribute news and new product announcements to Digital Engineering.
Press releases may be sent to them via [email protected].
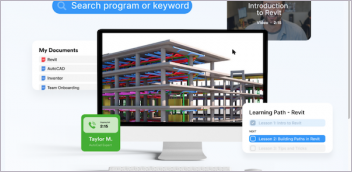

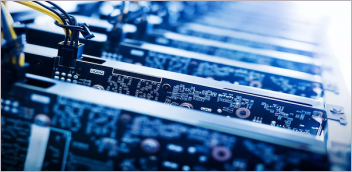
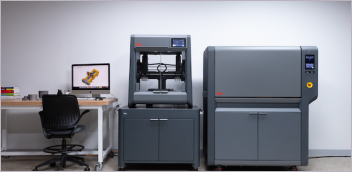