Oakley Leverages AM to Reimagine Design Processes
HP Jet Fusion 3D printer promotes greater and faster design iteration, helping Oakley bring new prototypes to life.

Oakley is leveraging the HP Jet Fusion 580 platform to transform its design workflows into a more iterative process. Image courtesy of Oakley.
Latest News
January 31, 2020
Oakley is best known for its vast portfolio of sports gear like sunglasses, googles and helmets not to mention its hip lifestyle brand. What’s less familiar about the high-performance sports equipment manufacturer is its long-time and increasing reliance on 3D printing as a way to accelerate its prototyping process and promote more expansive design iteration.
Although Oakley has been integrating 3D printing into parts of its design workflows for decades, the company took a major leap forward, broadening usage into new print and color technologies that would allow it to produce truly functional parts for improved and faster prototyping. The company expanded its relationship with HP, adopting the Jet Fusion 580 platform for rapid prototyping across multiple product lines, including sunglasses and helmets.
“Today [with 3D printing], our team takes a 2D sketch on paper and makes it reality,” says Jonathan Clingenpeel, Oakley’s design model shop manager. “HP Jet Fusion allows us to make things faster, cheaper, lighter, just better all around.”
Watch this video to learn more about how Oakley is leveraging the HP Jet Fusion 580 platform.
Accelerating time from design to prototype is one of the primary advantages of the HP Jet Fusion technology. What used to take two or three days to produce a prototype part with older AM technologies now takes Oakley less than 24 hours, which helps them visualize the impact of design changes in short order. Getting a part in one day versus as much as three days doesn’t sound like much in terms of time savings, but it adds up, notes Jeff Fawcett, 3D printing product management at HP.
“The build, test, learn, fix cycle is iterative and serial in nature,” explains Fawcett. “If you can save a day or two off of every design cycle, it adds up to make a significant impact in terms of time to market.”
The Jet Fusion 580’s color capabilities are also making a big difference in Oakley’s design process. The team can create detailed models, printing in different colors to break up the materials used in the model and allowing engineers and designers to more clearly see the different design iterations simultaneously. “Evaluating a concept strictly in monochrome parts hinders an ability to judge the design,” Fawcett says. “The value of functional color is they are better able to represent the final product.”
The use of color for parts, coupled with the available materials for the Jet Fusion 580, enable Oakley designers to create lightweight, durable prototypes that replicate production parts. In addition to prototypes, the team is using the HP Jet Fusion 580 printer to create assembly aids such as fixtures and jigs.
Compared to other color AM technologies like binder jetting and material jetting, the breakthrough for the HP Jet Fusion technology is that it’s the first to produce color parts that are truly functional in nature, Fawcett claims. “The nylon material allows Oakley to print parts with close approximation both in terms of strength and mechanical properties that are very representative of the final product,” he says. “That’s a real game changer for a company that has rigorous design cycles.”
More Hewlett Packard Coverage
Subscribe to our FREE magazine,
FREE email newsletters or both!Latest News
About the Author

Beth Stackpole is a contributing editor to Digital Engineering. Send e-mail about this article to [email protected].
Follow DE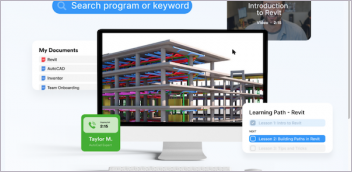

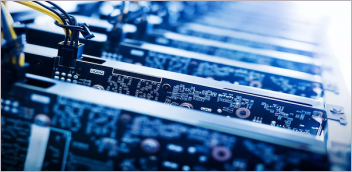
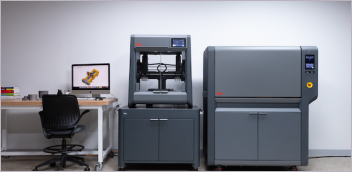