
OPEN MIND Technologies has introduced hyperMILL 2020.1 CAD/CAM Suite. Image courtesy of OPEN Mind Technologies.
Latest News
February 21, 2020
OPEN MIND Technologies AG, a developer of CAD/CAM software solutions worldwide, has introduced hyperMILL 2020.1, a new version of its advanced, comprehensive CAD/CAM software suite. In addition to 3D and 5-Axis Machining enhancements for complex part manufacture, the new version increases ease-of-use and overall programming performance, and includes key new automation and additive manufacturing strategies.
“The new version of hyperMILL encompasses a wide range of user friendly enhancements and important new machining strategies, further advancing the capabilities for accurate, efficient 3D and 5-Axis machining,” says Alan Levine, managing director of OPEN MIND Technologies USA, Inc.
For rest material machining, hyperMILL 2020.1 offers new Corner Rest Machining strategies for 3D and five-axis techniques that enhance complex machining applications including mold and die. Enabled by a simple instruction, corners can be machined largely by vertical stroking motions. Then traditional z-level steps can be used to blend with the vertical section and the lower floor area. The top section has an automatic surface extension to enable the production of sharp edges.
hyperMILL 2020.1 features a new five-Axis Blade Tangent Milling strategy, which increases efficiency and improves surface quality when milling with conical barrel cutters that have a large primary angle. As a result, higher feed rates are possible, while avoiding center-cutting. Large stepovers provide a surface finish.
Programming is simplified within the Mill-Turn module by a new Automatic Contour Feature Splitting capability, enabling hyperMILL to automatically determine the area to be machined based on the turning contour. The grooving job will automatically recognize if a contour is a groove, making it faster and easier to program certain areas.
A new hyperMILL Automation Center allows users to automate the job list creation processes in hyperCAD-S, serving as a development and runtime environment. New features also include the ability to select and position the clamping device, as well as define a uniform process for all programmers.
The ADDITIVE Manufacturing process in hyperMILL CAM software supports 3D printing/ additive processes and provides efficient hybrid processing with simultaneous additive manufacturing and subtractive machining on one machine tool. hyperMILL ADDITIVE Manufacturing technology offers flexible strategies for additive material applications, including filling strategies for both planes and free-form shapes, and in 2D and 3D sections.
Improving probing, new hyperMILL CAM software includes Slot-Rib Probing to measure slots and ribs using familiar technology parameters. For high stock removal rates, 3D machining strategies in hyperMILL 2020.1 now include 3D Optimized Roughing in high-performance hyperMILL MAXX Machining mode. The roughing process also offers improved area sorting, resulting in fewer retractions and improved collision checking. In addition, two new user-friendly functions are now available in 3D Profile Finishing including automatic face extension and free tool geometry.
Automatic face extension can be used during programming to extend the circumference of selected milling surfaces, eliminating the need to modify the milling faces in the CAD system beforehand. Free tool geometry enables the use of any tool type for highly detailed programming and collision control.
Sources: Press materials received from the company and additional information gleaned from the company’s website.
Subscribe to our FREE magazine,
FREE email newsletters or both!Latest News
About the Author

DE’s editors contribute news and new product announcements to Digital Engineering.
Press releases may be sent to them via [email protected].
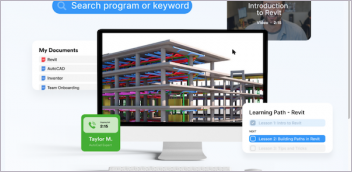

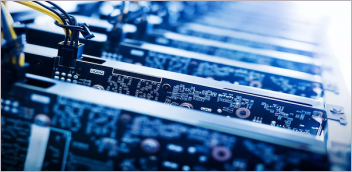
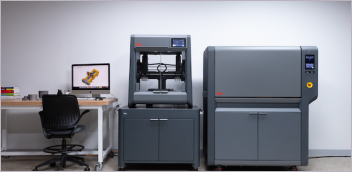