Latest News
September 30, 2011
By DE Editors
nCode has announced new solutions for thermo-mechanical fatigue calculations will be available in the next release of nCode DesignLife software. The company says it will enable a range of high temperature durability simulations. It will be available at the release of nCode version 8.
nCode DesignLife uses stress and temperature results from finite element software and provides CAE durability simulation to estimate component life in these extreme operating conditions. Building upon previous projects with industry partners investigating available thermo-mechanical fatigue (TMF) methods, this commercial software implementation in nCode DesignLife 8 is designed to provide tools that can be used to solve real-world design problems.
Components in high temperature operating environments such as engine manifolds, pistons and exhaust systems can suffer from complex failure modes. At temperatures above 30% of the melting point, the steels and alloys used in these cases can “creep,” causing a progressive stretching (increasing strain) of the component under constant load. Other complicating effects include the oxidation of the metal, which also affects the operational strength of the material.
The implemented methods include the Larson-Miller creep model and Chaboche methods for creep and fatigue, and also combined creep-fatigue interaction. The required materials data can be provided through a Materials Testing service available from HBM-nCode at their ISO9001 certified laboratory in Derbyshire, UK.
For more information, visit nCode.
Sources: Press materials received from the company and additional information gleaned from the company’s website.
Subscribe to our FREE magazine,
FREE email newsletters or both!Latest News
About the Author

DE’s editors contribute news and new product announcements to Digital Engineering.
Press releases may be sent to them via [email protected].
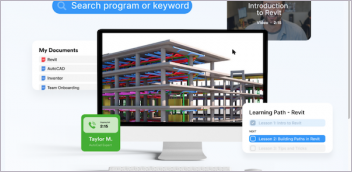

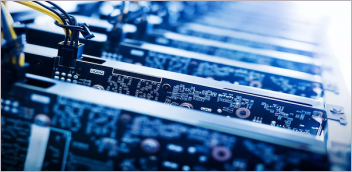
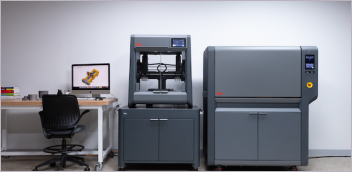