Latest News
March 9, 2017
CoreTech System (Moldex3D), provider of plastic injection molding simulation solutions, has introduced the latest release of Moldex3D R15.0. This newest version offers enhanced performance, accuracy and efficiency to streamline simulation workflow and provide faster turnaround times, according to the company.
One significant improvement in Moldex3D R15.0 is the reduction in pre-processing time and effort. The new runner meshing technology enables automatic generation of high-resolution hexahedral meshes and offers various node types for line runner connections to better capture the intended geometric shape of the runner design and deliver more accurate predictions.
Also, the extended nonmatching mesh technology supports the automatic meshing of mold components to be nonmatched, such as the interface between part and part insert/mold base to obtain accurate simulation results with minimal effort.
Moldex3D Studio is an integrated platform that streamlines all phases of the simulation workflow, from pre-processing to post-processing onto one intuitive, ribbon-style interface. The new platform complements the current Moldex3D Designer and Moldex3D Project applications and enables users to display and compare simulation results of multiple designs simultaneously to shorten the product development time.
The fully coupled process simulation is a pioneering breakthrough in Moldex3D R15.0. Users can now take advantage of the new coupling technology, which the company says can simultaneously utilize Flow/Pack/Cool/Warp solvers to obtain optimal accuracy for simulating products of complex geometric designs or advanced manufacturing process like rapid heat cycle molding (RHCM).
Moldex3D R15.0 also provides new simulation capabilities for in-mold decoration (IMD) and polyurethane (PU) chemical foaming process. The boundary condition application in the pre-processor of IMD simulation is made available the first time in commercial mold-filling analysis software to provide a quick and easy approach to meshing the decoration layers for simulation. Moreover, the “wash-out index” feature enables designers to better predict washout of the ink of the decoration film to ensure successful decorative products.
The machine interface is further expanded to include over 15 mainstream injection molding machine manufacturers to shorten the gap between the predicted and real-life parameters.
“Moldex3D is devoted to improving its software’s functionality and simulation accuracy in each release,” said David Hsu, president of product development at Moldex3D. “With the new features and enhancements in Moldex3D R15.0, we aim to provide a high-performing CAE analysis with greater accuracy and efficiency to help users design and manufacture high-quality plastic parts with faster turnaround times which truly gives them an ability to keep an edge over competition and achieve excellent results.”
More information on CoreTech can be found here.
Sources: Press materials received from the company.
Subscribe to our FREE magazine,
FREE email newsletters or both!Latest News
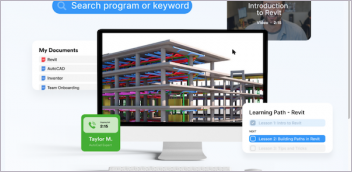

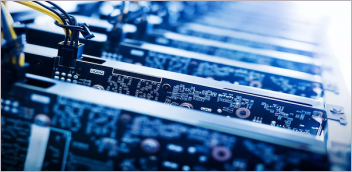
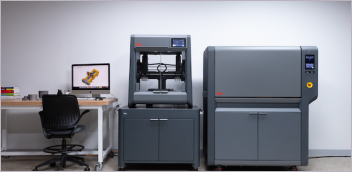