Latest News
September 1, 2004
By Nick Dewhurst
Remember Japan? In the fall of 1989, both Business Week and Industry Week broke stories about a new approach to product design that promised to make U.S. manufacturing more competitive with our upstart neighbor to the east.
The stories reported how Ford, General Motors, IBM, NCR, Texas Instruments, and a host of other engineering companies were racking up spectacular cost savings on their products by focusing on manufacturability. Ford even named a figure, boldly stating that a disciplined approach to design for manufacturability had helped save more than $1.2 billion.
Major Design for Manufacture and Assembly (DFMA) software goals at Dell Inc. (Round Rock, TX; dell.com) are improved design efficiency and increased factory throughput. Assembly innovations such as pushbutton releases for its Optiframe computer chassis helped the company avoid construction of a new factory and saved an estimated $60 million in labor, material, and supply chain costs.
What a difference a decade and a half makes. These stories seem oddly prophetic now, given the claims and counterclaims being made everywhere from union halls to the halls of Congress about the U.S. business phenomenon of industrial outsourcing. Whether outsourcing will improve U.S. competitiveness is yet to be seen. Nonetheless, the stampede is on to relocate manufacturing to overseas markets with lower labor costs.
The thing iswhat everyone knew by 1989 but has since forgottenlabor has a relatively small influence on total product cost. By the time you hire someone to manufacture your product, you have already designed in 70 percent or more of the cost. In other words, if you really want to cut product costs, do your cutting during design. U.S. manufacturers learned this lesson in the 1980s to rousing success and are still taking advantage of it today.
Below: MDS SCIEX (Ontario, Canada) uses DFMA principles to spur team brainstorming and provide a quantitative basis for making design decisions. With the company’s QSTAR triple quadrupole mass spectrometer, engineers saved significant costs over previous products by optimizing the design of modular components, achieving new standards for assembly, serviceability, and shipping.
So, if we’ve been here before, why haven’t we been able to keep our good design habits? Not every organizational culture is healthy enough to handle the demands that arise from an ongoing focus on manufacturability. The entire enterprise must stay committed, especially leaders at the top. Collaboration and information sharing across functional areas must deepen. For innovation to continue, everyone needs to agree on the occasional sacrifice of protected territories and sacred cows.
Success may even play a role here. When you have already saved hundreds of thousands of dollars, year after year, by applying a rigorous process to product design (as many companies have reported doing), you might start taking shortcuts through the process. You might begin to imagine you can somehow do design for manufacturability without explicitly following the process that saved you all that money in the first place. But it isn’t magic that keeps your product development team from going to pieces at the sight of a market deadline. It is your disciplined design process.
Luckily, the tried-and-true principles of design for manufacture and assembly are evergreen and widely available. Make them work for you.
Design Reviews: The Earlier, the BetterNew product development is a creative activity. Give your organization enough time for its best ideas to hatch. The design review process that most companies practice today is too hurried and lacks structure. Product development stage gates are often perceived as hoops to jump through the second before the buzzer sounds. If your design reviews tend to take place the same week you have to release the design, the review is functioning only to rubberstamp the design, not to rethink it. Call it a design analysis instead of a design review. Have more than one.
Devise a structure for your meetings that encourages attendees to participate. A design review should be an opportunity for active and concrete feedback, not a time to defend the citadel. You want to facilitate collaborative analysis of a product design. A focus on manufacturability leads to group discussion and questioning of design assumptions. Do these parts really need to be made of different materials? Is every part in the design absolutely necessary, or can we combine parts to simplify the product?
Figure 1 (left): Delphi (Troy, MI) applied DFMA software in three stages to the modular evolution of its door systems. This figure shows an exploded view of an early modular door. At this stage the water barrier and latch system are separate, and the wiring system is not yet fully integrated. Compared to a conventional door, however, this design cut the number of components from 16 to 9 and reduced assembly time from 12 minutes to 9.4 minutes. | |
Figure 2 (right): The next stage of design analysis led to Delphi’s SuperPlug Module Door System. This system incorporated all interior door hardware, but the water barrier and latch system still remained separate. The number of components was reduced from 9 to 8, and assembly time was further reduced to 8 minutes. | ![]() |
Figure 3 ( left): Exploded view of the Wet/Dry Module Door System. In its third redesign of the door module, Delphi engineers fully incorporated the water barrier, wiring harness, and latch system. The number of components is now just 4, and assembly time is 6.6 minutes. The project underscored the strength of Delphi’s overall strategy of modularization, establishing a baseline for lean design initiatives. |
If you have no corporate strategy for should-costing, you have essentially issued your product developers a blank check. Engineers are responsible for understanding and controlling product development costs, but a strategic emphasis on should-costing has to come from corporate-level leadership. Once corporate management grasps the concept that cost is a design issue, revolutions happen in product development.
Let’s say your standard corporate requirement is a 6 percent annual reduction in production costs. Each year the organization achieves that goal, and everyone pats themselves on the back and goes home happy. But what if the product that everyone is so happy about is actually costing the organization 30 percent more than it would if it were redesigned? How would you know if you could save costs by simplifying the assembly and reducing the part count? The fact is, you wouldn’t, unless you had thoroughly examined the product design from a should-cost perspective.
Let’s be honest. Any product developer would love to be the one who finds a 30 percent reduction in cost. Corporate leadership ought to help them do it. Start by requesting more time for design reviews, more support for questioning and debate. Enlist suppliers in a conversation about component costs and cost drivers instead of price.
Metrics Are NecessaryPeople can debate all night about the appropriate metrics for measuring product development. Astonishingly, though, many organizations continue to use historical costing to estimate costs for new products. If you can survive in your market by making only small incremental changes to products, historical costing is probably good enough. But if you have to continually innovate to stay alive, you may as well throw historical cost metrics out the window.
How can historical costs quantify something you’ve never made before? Let’s say you’re considering using an injection-molded enclosure for a product that has gone through multiple generations in a sheet metal housing. To determine whether injection molding is the way to go, you need to know more than what you spent on sheet metal last quarter; you need to understand where the cost trade-offs lie. Considering the potential increase in manufacturing costs, will an injection-molded design with fewer separate parts cost less than the sheet metal design? Well-researched metrics will help you decide.
Product development is an investment activity. Organizations that are committed to innovation must be able to quantify the cost impact of dramatic changes to products. Applying a rigorous metric approach to design analysis will help you understand the cost drivers for your products and will give you a quantifiable basis for deciding which designs deserve investment.
Dialogue Is InevitableThe biggest innovation yet to occur in U.S. manufacturing culture isn’t about measuring materials cost or assembly operations. It’s about encouraging open, ongoing, multidisciplinary communication and the sharing of knowledge across the enterprise. Despite the revelations of the 1980s, the “throw it over the wall” phenomenon is still at work. The silos persist. Many U.S. companies still fail to recognize the direct relationship between product manufacturability and concurrent engineering. Many companies still underutilize the rich expertise in their own organizations, allowing barriers to dialogue between functional departments, or between engineers and suppliers, to remain in place. The barriers have to goand they will. Years of case study evidence from leading developers of automotive, aerospace, medical, and consumer products have shown that cross-functional dialogue during design improves manufacturability. In the end, wherever the labor force is located, U.S. manufacturers who solve these types of management issues will thrive.
Nicholas Dewhurst is executive vice president at Boothroyd Dewhurst, Inc., a developer of tools and technologies that provides manufacturing assembly knowledge to the product design process. Send your comments about this article to Desktop Engineering Feedback.Company and Product Information
Design for Manufacture and Assembly
Boothroyd Dewhurst, Inc.
Wakefield, RI
dfma.com
Subscribe to our FREE magazine,
FREE email newsletters or both!Latest News
About the Author

DE’s editors contribute news and new product announcements to Digital Engineering.
Press releases may be sent to them via [email protected].
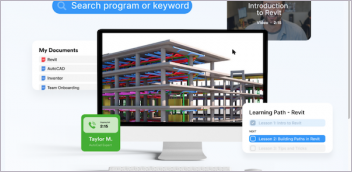

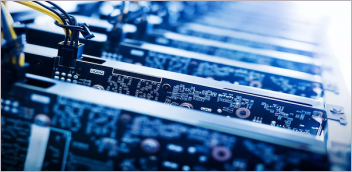
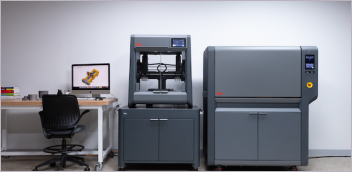