Latest News
January 28, 2013
![]() |
Today’s read at the other end of the Check It Out link is an absolute hoot. More importantly, it’s also something for you people in the shop wanting to do your own thing or expand your service offerings to seriously consider.
The plot is that a marine biologist named Greg Marshall saw a fish snatching a ride on a shark’s gut and figured that he should develop an underwater camera so that he could see the world from a shark’s point of view. But of course, right?
So, he did it. And it works great. National Geographic then comes along with some project funding. And before you know it, researchers have Crittercams clipped on penguins, sharks, sea turtles, and other sea and forest friends all over the place.
To get a Crittercam on a shark you use a 7-foot-long aluminum pole to drop it onto the shark’s dorsal fin. Now, a pole to affix a video and data logging system on a shark’s dorsal is not something you order from Sharper Image. You custom make it. A typical assembly has about 17 specialized machined parts, and a big order might be five poles—always on short notice, naturally. Ergo, no machine shop wanted to deal with it cost-effectively.
Here comes Frank Borke, aka Master Pattern of Lafayette, CO. His specialty is machining small-scale short-runs, prototypes, and custom jobs that other shops can’t afford to do. He machines all non-stock parts for Crittercam poles.
Borke’s workhorse is a Tormach personal CNC mill, the PCNC-1100 model equipped with a fourth-axis rotary table and duality lathe. Think of “personal” as in personal computer. That means easy to use, simple to deploy, and affordable. Borke says that his PCNC-1100 with options ran him about $16,000. That’s key to how he’s making it happen with his custom machining business. You can’t afford to have a machine two or three times more expensive doing five tiny runs of 17 or so parts. The PCNC-1100, however, makes it possible.
The PCNC-1100 cuts pretty much any material, not only the 6061 aluminum for the Crittercam pole. It meets ±0.001-in. tolerances, and it uses single-phase power. That power requirement is important to Borke because it let him move his shop to a building that he plans to wire up for solar power. In a nutshell, Borke’s investment in a personal CNC has empowered him to establish and grow his business.
Click the link up there to read about the Crittercam and Frank Borke’s role in making it happen. Hint: click on the pictures on the right-hand side for larger images.
Thanks, Pal. – Lockwood
Anthony J. Lockwood
Editor at Large, Desktop Engineering
National Geographic’s Crittercam: Using CNC to Study Shark Behavior
Subscribe to our FREE magazine,
FREE email newsletters or both!Latest News
About the Author

Anthony J. Lockwood is Digital Engineering’s founding editor. He is now retired. Contact him via [email protected].
Follow DE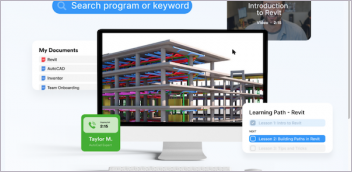

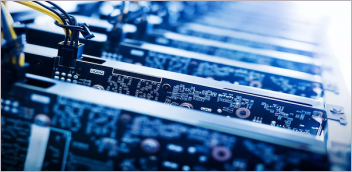
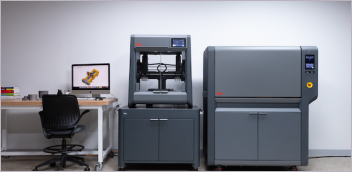