NASA Tests Microgravity Printed Objects

Latest News
March 5, 2015
The wrenches that astronauts printed on the International Space Station (ISS) are back on Earth and ready for testing.
The SpaceX Dragon brought back the 3D printed tools during a re-supply mission on Feb. 10. NASA scientists will examine the wrenches to see if they meet the same standards as manufactured tools, and if the printers used to create them can be approved for future Mars manned missions.
The printer on the ISS was specifically designed for microgravity use by Made in Space. As we wrote about earlier, Europe’s space agency will send its own 3D printer to the space station this year. The Europeans are launching the POP3D printer made by Altran.
“For the printer’s final test in this phase of operations, NASA wanted to validate the process for printing on demand, which will be critical on longer journeys to Mars,” explained Niki Werkheiser, the space station 3-D printer program manager at NASA’s Marshall Space Flight Center in Huntsville, AL. Insight from demonstrations in microgravity also may help improve 3D printing technology on Earth.
The first ratchet wrench was printed on the Made in Space printer back in November 2014. NASA e-mailed the design to the ISS, and scientists there printed the wrench along with multiple replacement parts. The wrench was created in Autodesk Inventor and converted to G-code.
Other objects were pre-programmed into the printer before launch. NASA will compare the printed objects to those made on Earth using the same printer to explore the effects of microgravity on the printing process and finished parts.
If 3D printing proves viable, it would make it easier for scientists on the ISS to obtain parts and other items without waiting on costly re-supply missions. The technology will also make it easier to supply missions beyond Earth’s orbit.
Source: NASA
Subscribe to our FREE magazine,
FREE email newsletters or both!Latest News
About the Author

Brian Albright is the editorial director of Digital Engineering. Contact him at [email protected].
Follow DE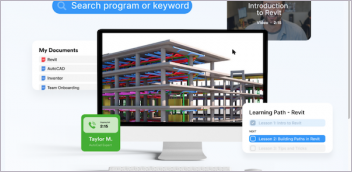

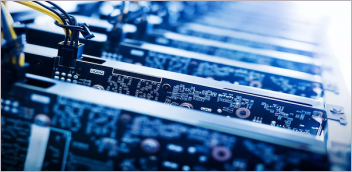
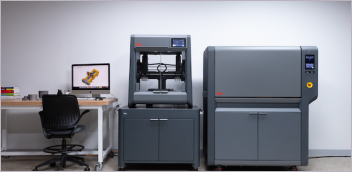