NASA Advances Toward 3D Printed Rocket Engine

NASA test fires 3D printed rocket. Courtesy of NASA.
Latest News
January 4, 2016
One of the perks of additive manufacturing (AM) that has caught the attention of manufacturers is the potential to save money during both the testing and final build phases of developing new parts or equipment. In some cases, the savings are felt through quantity, with AM systems churning out thousands of parts, but generally the savings come as a result of reduced material waste.
NASA is one agency that is certainly interested in saving money. The space exploration agency has been dealt cut after cut by lawmakers over the last 20 years. Anything that offers a way to reduce costs while still allowing NASA to fulfill its mission is bound to garner interest. The potential savings offered by AM has led to NASA conducting a series of tests to determine the potential of building a complete rocket engine using 3D printed parts.

Each stage of the testing process has been a success, with 3D printed parts showing they are rugged enough to handle the extreme temperatures generated by a rocket firing. The latest test featured the most complete rocket yet, and was conducted using cryogenic liquid hydrogen and oxygen to create 20,000 pounds of thrust.
“We manufactured and then tested about 75% of the parts needed to build a 3-D printed rocket engine,” said Elizabeth Robertson, the project manager for the additively manufactured demonstrator engine at NASA’s Marshall Space Flight Center in Huntsville, AL. “By testing the turbopumps, injectors and valves together, we’ve shown that it would be possible to build a 3D printed engine for multiple purposes such as landers, in-space propulsion or rocket engine upper stages.”
In all, seven tests were performed with the longest lasting 10 seconds. During the tests, the 3D printed parts were exposed to the extreme highs and lows of an engine firing. The actual firing produced temperatures in excess of 6,000°F (3,315°C), and the turbopump continued to function as it delivered liquid hydrogen fuel that was cooled below 400°F (-240°C).
Along with the potential for material savings, leveraging AM for the rocket offers NASA engineers freedom of design not possible with more traditional manufacturing methods.
“This new manufacturing process really opened the design space and allowed for part geometries that would be impossible with traditional machining or casting methods,” said David Eddleman, one Marshall’s propulsion designers. “For the valve designs on this engine, we used more efficient structures in the piece parts that resulted in optimized performance.”
Below you’ll find a short video of the rocket test.
Source: NASA
Subscribe to our FREE magazine,
FREE email newsletters or both!Latest News
About the Author
John NewmanJohn Newman is a Digital Engineering contributor who focuses on 3D printing. Contact him via [email protected] and read his posts on Rapid Ready Technology.
Follow DERelated Topics
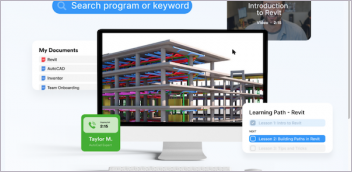

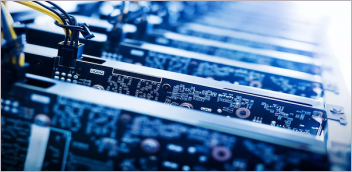
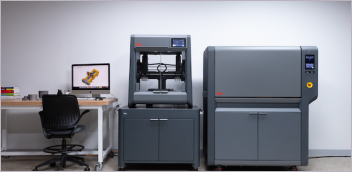