Nano Dimension Collaborates with Harris Corporation for Space Project
Nano Dimension and Harris Corporation receive grant approval to create hardware to fly on the International Space Station.
Latest News
May 31, 2019
Nano Dimension Ltd., an additive electronics provider, has received a grant approval from the Israel Innovation Authority for developing hardware, in cooperation with Harris Corporation, that will fly on the International Space Station (ISS) and communicate with Harris’ ground-based satellite tracking station in Florida. This project will provide a systematic analysis of 3D printed materials for radio frequency (RF) space systems, especially for nanosatellites.
The total approved budget for the Israeli portion of this project is approximately $416,000, of which the Israel Innovation Authority will finance 40%. According to the terms of the grant, Nano Dimension will pay royalties on future sales up to the full grant amount.
This project is being conducted in collaboration with Harris Corporation, a technology innovator that provides solutions that connect, inform and protect its clients. The Harris portion of the project is sponsored by a grant from Space Florida. During this one-year project, both companies will optimize the designs of the 3D printing process and RF components and prepare a system for the flight studies at the ISS.
This project has been selected by the Center for the Advancement of Science in Space, the manager of the ISS U.S. National Laboratory, to fly the space flight experiment on the ISS, using the team’s 3D printed materials and circuits. In this project, the companies will pioneer the first-of-a-kind space flight experiment, that will fly in space at low earthorbit for one year on the ISS, helping to understanding how 3D printed circuits, systems and materials will endure in various space environments.
This project will demonstrate innovative methods for manufacturing new RF systems. Until now, manufacturing of RF systems has remained static for the last 30 years with each circuit in its own “gold box/boxes” interconnected with cables and connectors. With 3D printing, the industry can explore a new manufacturing paradigm, that eliminates manual labor and streamlines production. Another benefit to this technology is a reduction/elimination of wasted material.
Sources: Press materials received from the company and additional information gleaned from the company’s website.
Subscribe to our FREE magazine,
FREE email newsletters or both!Latest News
About the Author

DE’s editors contribute news and new product announcements to Digital Engineering.
Press releases may be sent to them via [email protected].
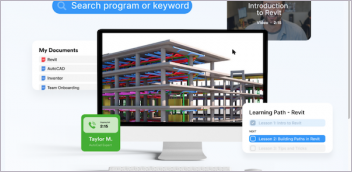

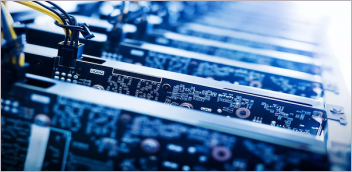
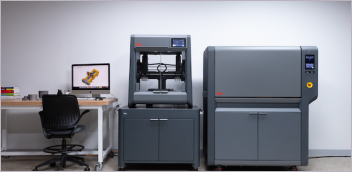