More Options for Metal Injection Molding
Latest News
April 8, 2015

Manufacturing services provider Proto Labs Inc. has announced the availability of three new low-alloy steel material options for its metal injection-molding (MIM) process. Parts made with the new materials, Proto Labs explains, are suitable for prototypes and low-volume production parts and molds.
The MIM manufacturing process can produce metal parts with intricate geometries. Parts manufactured through the MIM process can have complex shapes, present superior surface finishes, possess good strength and provide mechanical properties similar to wrought materials, according to Proto Labs.
The newly announced materials are two nickel steel materials (Catamold FN02 and FN0205) and a chrome-moly material (Catamold 42CrMo4). The latter, Proto Labs states, is the MIM equivalent of 4140 steel. In addition to the new materials, Proto Labs offers clients Catamold 17-4 PH K and Catamold 316L K stainless steel material options.
The new low-alloy steel materials, says the company by way of example, can be used in such applications as automotive engine and transmission components, firearm and archery components as well as in the development of industrial goods, including hand tools, power tools and door and window lock hardware. The company adds that the low-alloy steels create strong, wear-resistant metal parts when heat-treated and that parts can be coated in post-processing for further protection.
At this time, Proto Labs approximates maximum part size limits as 4 x 4 x 4 in. (101 x 101 x 101 mm) and no deeper than 2 in. (51 mm) from any parting line. The maximum projected mold area is 10 sq. in. (6450 sq. mm), and a maximum part volume of less than 1.25 cu. in. (20.48 cc) is specified. Characteristics such as side-actions can affect part size maximums, and, under certain conditions, tradeoffs are possible to achieve sizes that exceed the specified maximums.
“We’ve had tremendous customer demand for stainless steel with MIM last year, and expect the same response to our new low-alloy metals,” says Becky Cater, product manager for MIM at Proto Labs in a press statement. “We offer many different hard and soft metals through our 3D printing and CNC (computer numerically controlled) machining services at Proto Labs, but nickel steel is only produced through metal injection molding. This material boost will inherently let our customers do more things in the realm of low-volume metal manufacturing.”
Proto Labs reports that it can produce from 25 to more than 5,000 metal injection-molded end-use parts within 15 days. To learn more about the metal injection-molding services at Proto Labs, click here.
Access the guidelines on designing for the metal injection-molding (MIM) process.
Sources: Press materials received from the company and additional information gleaned from the company’s website.
Subscribe to our FREE magazine,
FREE email newsletters or both!Latest News
About the Author

Anthony J. Lockwood is Digital Engineering’s founding editor. He is now retired. Contact him via [email protected].
Follow DE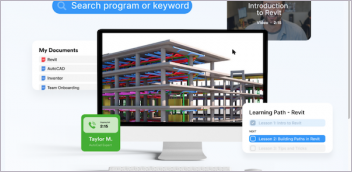

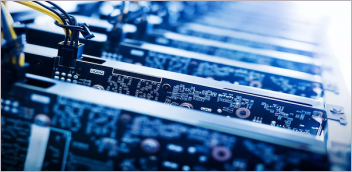
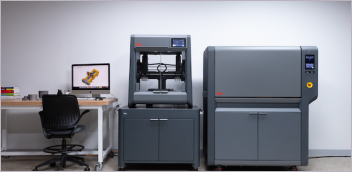