Latest News
November 29, 2007
By DE Editors
Moldflow Corporation (Framingham, MA) released Moldflow Plastics Advisers (MPA) 8.1, an easy-to-use plastics simulation software that allows part and mold designers to quickly evaluate the manufacturability of their designs so they can achieve the highest quality at the lowest cost in the shortest time to market.
MPA 8.1 helps users analyze a broader range of parts with 3D technology with a redesigned user interface, and shorten analysis preparation time using flexible modeling tools. Results can be interpreted more efficiently using results visualization options, and collaboration can be increased with expanded communication capabilities.
MPA 8.1 features 3D analysis capability for the simulation of parts with thick, solid regions, or variations in wall thickness. As plastics part geometry becomes increasingly more complex, the 3D technology in MPA allows customers to predict and avoid manufacturing defects before a mold is ever made, saving them costly and time-consuming production delays.
Other improvements of MPA 8.1 include a new panel-based user interface that streamlines workflow, provides uninterrupted access to models, and increases user productivity; flexible modeling tools like runner and cooling channel layouts to import from CAD systems or created using new modeling planes, snap tools, and visual cues to aid in precise positioning; intuitive results interpretation and visualization options allow for the comparison of results from multiple analysis iterations to realize design improvements and better understand plastics material behavior. Dynamic Help also allows users to quickly understand those results that have the greatest impact on optimizing their part and mold designs.
The Increased Collaboration leads to Enhanced report generation to automatically generate reports in Microsoft Word or PowerPoint formats in addition to HTML and enhanced smart tools that include a redesigned Cost Adviser for detailed part cost analysis and better planning; a Job Manager to take maximum advantage of available CPU resources and free engineers for other tasks; and a tool for comparing material properties to aid in selecting the best material for a given application.
For details, go to Moldflow.
Sources: Press materials received from the company and additional information gleaned from the company’s website.
Subscribe to our FREE magazine,
FREE email newsletters or both!Latest News
About the Author

DE’s editors contribute news and new product announcements to Digital Engineering.
Press releases may be sent to them via [email protected].
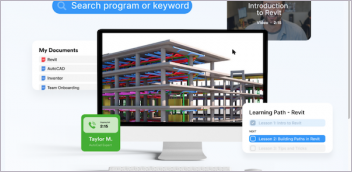

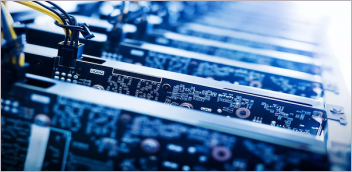
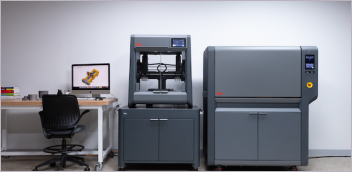