Moldex3D Aims to Speed Gating Iteration by 95% with Latest Release
Moldex3D R16 offers user-friendly interface, enabling users to quickly evaluate different gate designs on L/t results, and then output the mesh.
Latest News
October 25, 2018
Weld line issue is a common surface defect of plastic products. It can affect the structural properties. Other than part design, gate location design is another major factor of weld lines. Take automotive products as an example; they are large thin-shell parts with large L/t ratio, and the gate design mainly dictates the resulting product quality. To simulate the molding process of this automotive part, users traditionally have to set the gate locations based on their experience at the pre-processing stage, and then run filling analysis. The calculation time can be more than 3 hours because the mesh element amount is considerably large for big parts. When the analysis is done, users have to check if the weld line positions are acceptable. If not, they have to repeat the process as mentioned, which can be very exhausting and time-wasting. In today’s industries, the time spent in the product design stages is increasing in importance. A robust and upgraded CAE simulation tool is required.
To attempt to meet these demands, Moldex3d has made many breakthroughs in the latest version, R16. First, the L/t workflow has been improved in the pre-processing tool, Moldex3D Designer. Moldex3D R16 also offers user-friendly interface, enabling users to quickly evaluate different gate designs on L/t results, and then output the mesh. Second, Moldex3D R16 Quick Flow analysis can perform high-speed filling analysis for users to view the weld line results, according to the company. Combining the new L/t workflow in Designer and Quick Flow analysis mentioned can enhance the efficiency of gate position designs, the company notes.
The following figure is a case of an automotive front panel. Users can observe specific L/t value areas in Moldex3D R16, which provides L/t ranges of different polymer types so that users can decide proper gate designs.

As shown in the figure below, Quick Flow Analysis is able to validate the effects of different gate designs toward weld lines in a short time, according to the company. Under the fixed gate criteria, Quick Flow Analysis can also simulate how different valve settings affect the weld lines.

Among the three flow analysis options, Regular Flow analysis costs 2.6 hours, while Quick Flow analysis only costs 10 minutes with 95% calculation time reduced.
Therefore, we can see that the new L/t workflow of Designer and the Quick Flow analysis in Moldex3D R16 can both significantly benefit plastic components with a large surface by providing efficient simulation solutions to shorten gating iteration time from hours to minutes.
Sources: Press materials received from the company.
For More Info
Subscribe to our FREE magazine,
FREE email newsletters or both!Latest News
About the Author

DE’s editors contribute news and new product announcements to Digital Engineering.
Press releases may be sent to them via [email protected].
Related Topics
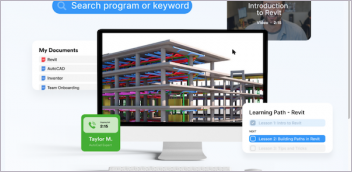

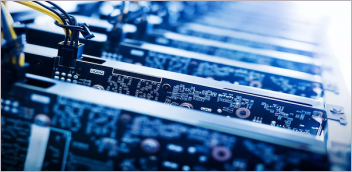
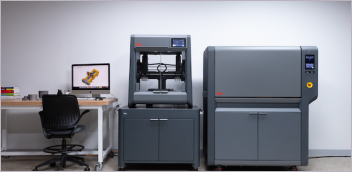