MMX 2023: Additive Manufacturing Has Bright Future
Exploring how government, military, workforce work together to expand use of additive manufacturing.

Tim Sakulich, executive director of the Air Force Research Laboratory, gave a keynote address at the 2023 MMX meeting in Canfield, OH.
August 25, 2023
Collaboration that is done well within the additive manufacturing community can result in a competitive, well-oiled national AM ecosystem. That’s the premise behind the 11th annual America Makes MMX (Members Meeting & Exchange), which took place in mid-August 2023 at Waypoint 4180, an event space overlooking scenic Kensington Golf Club in small-town Canfield, a few miles southwest of Youngstown, OH.
The theme for this year and every year past is always 'member driven,' according to John Wilczynski, executive director, America Makes. “Our goal is to deliver a program that addresses the diverse needs of the America Makes membership by featuring speakers and discussion panels that align to the needs of our stakeholders.”
The event, hosted by America Makes, the public-private partnership for additive manufacturing education and technology, gathered nearly 400 members of the additive manufacturing community, who came from industry, academia, government and the workforce, to convene for two days of panel discussions, keynotes and high-level presentations. Between sessions, guests were welcome to visit the few dozen exhibitors lining the venue hallways.
Wilczynsk said of the 2023 event, “This meeting was designed to focus on the membership. It is the one time each year where bring our membership community together to discuss the successes, ongoing efforts, and needs facing the industry. This year’s event focused on delivering value to the membership while seeking inputs around areas of improvement.
“For me, the major theme that emerged was the expanding mission the membership requires from the Institute,” Wilczynski added. “It is not a question of 'or' but rather the reality of 'and,' which indicates our industry is maturing and the needs of the community are both evolving and expanding.”
A few MMX highlights:
This year’s MMX featured speakers and panels from several government partners, industry members and academia who discussed policy, trends, strategy, challenges and numerous other topics directly aligned to the interests of the attendees.
Timothy J. Sakulich, executive director, AFRL (Air Force Research Labs), gave an opening keynote on how technology goes hand in hand with warfighter capability.
Ryan Dehoff, director, Manufacturing Demonstration Facility, Oak Ridge National Laboratory, discussed AM-specific needs of the Department of Energy.
Stephanie Hoaglin, Director, OIB (Organic Industrial Base) Modernization Task Force, delivered a talk on the U.S. Army’s 15-year, $18 billion plan to accomplish readiness requirements and strategic initiatives.
Expanding the workforce in a way that bolsters and accelerates additive manufacturing technology was the thought behind a Day 2 panel discussion. Panelists included Ohio Manufacturers Association/Mahoning Valley Manufacturers Association; The Lanterman Group; 3Degrees; NAVAIR, RICOH USA, & Edge Factor.
Danielle Miller, director, Policy, Analysis & Transition, shared Department of Defense policy urgencies for the DoD Industrial Base.
And a “best practices” panel explained the initiatives and varied regional approaches of the Defense Manufacturing Community Support Program (DMCSP), that was moderated by Hiwot Gebremariam, program activity lead for DMCSP. Panelists were James Hubbard of VA; Josh Penney, TN; Tulinda Larson, UT; and Aaron Patrick, OH.
The member buzz at the event, according to Wilczynski, was one focused on collaboration. “Attendees commented most frequently on the collaborative spirit inspired at the event. There was also excitement due to the multiple open project call solicitations. The event was an opportunity for the membership to network and develop teams in response to the RFPs,” he said.
Keynote on AM Ecosystem
John Sakulich, AFRL Air Force Materiel Command, Wright-Patterson Air Force Base, opened with a keynote on “The Additive Manufacturing Ecosystem: Department of the Air Force Science & Technology Perspective.” AFRL is the Department of Air Force’s laboratory, supporting two services: U.S. Air Force and U.S. Space Force.
“Our job is really to look to the future and try to anticipate where technology is going. Take technology being developed today and envision how that might be matured in a way that gives us a future military advantage in the battlefield,” Sakulich says. Though he acknowledged, “We hope to never have to go to that [point] and that our capabilities are a sufficient deterrent to protect our nation’s interests but at the same time, every airman and every guardian out there depends on technology to have their back if we ever have to send them into a fight.”
He shared where the Air Force needs to be focused as well as the capabilities this arm of the government is seeking to develop for the future of space, air and cyberapplications.
In today’s world, he says, “It’s all about speed and agility. Move things faster to maintain that competitive edge. We are looking for ways to solve military problems —to change the way we think about design. How do we make it easier to supply parts? We can use additive to make it much easier to supply parts at speed. Additive opens up an ecosystem of opportunity,” Sakulich says.
DoE Additive Engagement
Dehoff of the Department of Energy shared strategies of the departmental efforts at the Manufacturing Demonstration Facility (MDF), including development of an ecosystem where the department could engage industry, other stakeholders, university partners and bring them in for co-development and place-based innovation around technology, as he explains.
The 5-year-old MDF and its 110,000 sq. ft. of floor space is home to hundreds of different additive systems that are all focused on driving technology forward, says Dehoff. In its 5 years of existence, MDF has had 37,000+ visits from industry stakeholders.
“In terms of strategy [at DoE] what we have seen is similar to DoD on the pandemic side. DoE had received an executive order looking at criticalities in the supply chain and disruptions that occurred due to COVID-19.”
DoE did some extensive roadmaps with three focus points: “Number one, secure the U.S. supply chain and understand how to do this from an energy perspective,” Dehoff explains. “Also, address affordability of clean air technologies if adopting those as a country, and continue what additive is well known for—improving energy efficiency in use and manufacture of components.”
Dehoff explains that DoE is evaluating different platform technologies, recognizing additive as one such example of a platform technology. “We’re looking at applying those platform technologies to energy-based applications,” he says.
“Our success is really based on industry success. Industry is a big part of what we do. Industry is responsible for 80%-90% of our success. If we cannot help industry in the U.S. be successful and if we can’t help industry maintain or onshore technology, we view that as not a success,” Dehoff says. “We are trying to bring resources that industry is challenged with that Oak Ridge could help solve.”
Panel Chatter
An afternoon panel session, “Transitioning Competencies and Skillsets into the Workforce Panel,” was moderated by Josh Cramer, education and workforce development director, America Makes. Panel speakers were Jessica Borza, Ohio Manufacturers Association/Mahoning Valley Manufacturers Association; Nick Bush, The Lanterman Group; Mike Vazquez, 3Degrees; Michael Pecota, NAVAIR; and Robert Wesley of Ricoh USA.
As Borza sees it, “Workforce development is a multifaceted challenge. It’s important to understand the demographics of the workplace. As for building the workforce of tomorrow, Borza invites the audience to take action now. She says it’s time to do things different. Go into coffeeshops, barbershops, to the football games to talk about the amazing careers in manufacturing. Bridge those conversations to the first level, entry level career.” Borza shares how her association has created a bootcamp program to give individuals fundamentals to be successful. “Manufacturers are then committed to hiring individuals who successfully come out of these programs,” she says. She also shares how the association recently partnered with America Makes to recruit a cohort made of women.
The topics of education and workforce development and ecosystem were two of the focus areas where America Makes received a great deal of feedback both during and after the event, according to Wilczynski. “Therefore, it is obvious that industry is working to adopt AM as a technology for productio,” he says. “These areas of interest are key as the community matures and expands to address the rigor required in most industrial sectors.”
Moving on to another panel in day 2, The Defense Manufacturing Community Support Program Best Practices panel invited leaders from regional DMCSPs to the stage to discuss how the program takes action in various parts of the country. Panelists were: Tulinda Larsen, Utah DMCSP; Josh Penney, Tennessee DMCSP; Aaron Patrick, OH DMCSP; James Hubbard, Virginia DMCSP; and Yittayih Zelalem, Illinois DMCSP; and moderator was Hiwot Gebremariam, Program lead, DMCSP.
The DMCSP was created to “support long-term community investments that strengthen national security innovation and expand the capabilities of the defense manufacturing industrial ecosystem,” according to the U.S. DoD’s Office of Local Defense Community Cooperation website.
Hubbard, of VA’s DMCSP, shared their state’s critical strategy, “We are building a talent pipeline through exposure starting in 6th to 8th grade programs and maintaining a consistent pipeline that leads through tech schools after high school and onto college,” he explains. “DMCSP helps support this strategy. From 6th to 8th grade we want to expose middle schoolers to CNC machining, additive, metrology, and so on. Increasing awareness and exposure is key to widening funnel.”
By high school, students can have a specific skillset, such as CNC or welding. “At that point students can have dual enrollment programs at high school/community college and can knock out the first year of two-year programs at a tech school,” he says.
At present the same VA DMCSP is also working with Patrick Henry College in state to build out a manufacturing technology degree. “A goal is to have a pipeline to move from 6th to 8th all the way into a career serving maritime and naval needs,” he explains. “If you have an educated workforce, it will bring technology in. It’s about getting right people to the table. Remember, industry is the customer. It’s about obeying the demand signal and being adapt to that.”
Penney of the Tennessee DMCSP says his region is focused on advancement of machine tools—machining technologies and automation—to address workforce needs. “We want to bring technology to companies to help implement their use in manufacturing processes. We have three main areas of focus: 1) Develop—work at the university level to develop new technologies across different departments at the university, making sure companies get support they need to advance technology. 2) Training the workforce; and 3) Connecting by hosting monthly webinars.”
Overall, Sakulich may have summed this year’s MMX up most succinctly: “We want to fully exploit the potential of additive. Our job is really to lead, to discover, to delve and mature, but really to deliver. It’s all good if it’s just technology, but it’s not good enough until it makes it into the hands of an application.”
As for future in-person activities, “Regarding future events, members expressed interest in better understanding the technoeconomic impacts of additive manufacturing, as well as how to generate improved market analysis,” Wilczynski said.
More America Makes Coverage
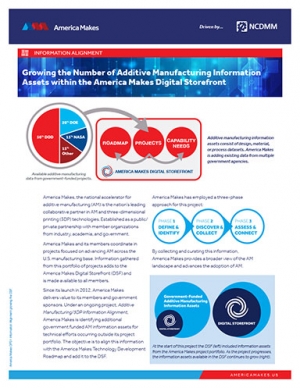
Subscribe to our FREE magazine,
FREE email newsletters or both!About the Author

Stephanie is the Associate Editor of Digital Engineering.
Follow DE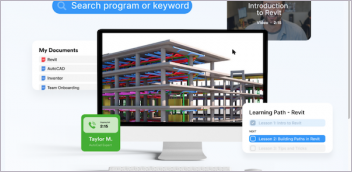

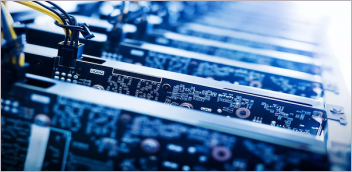
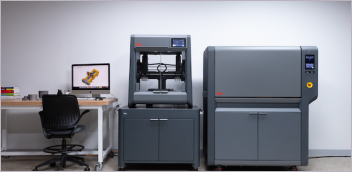