Mentor FloTHERM XT Release Simulates Complex Geometries with Ease
Latest News
May 3, 2017
Mentor, a Siemens business, has released the FloTHERM XT electronics cooling software product with advanced thermal management capabilities. Based on the electronics cooling DNA of the Mentor FloTHERM technology and the FloEFD CAD-centric philosophy, the FloTHERM XT product is an integrated mechanical design automation (MDA) and electronic design automation (EDA) electronics cooling solution. This latest version of the FloTHERM XT product offers functionalities to effectively simulate thermal effects of complex geometries.
Key capabilities in this new FloTHERM XT release include simulation of spinning parts in electronic enclosures; temperature-dependent power simulation; enhanced “Design of Experiments” parametric studies functionality to determine best design coverage; and thermal territory simulation when using various component materials.
The FloTHERM XT product can be used at all stages of the electronic design process, from design concept through manufacturing.
According to Mentor, key features include:
- Explicit Models for Spinning Parts. The new sliding mesh capability easily meshes the rotation region to accurately simulate the effects of spinning parts such as fans and rotors used in electronics enclosures.
- Temperature-Dependent Power Simulation. When attached to an object or planar source, the FloTHERM XT software will use the object’s own average temperature goal to adjust the applied power.
- Thermal Territory Simulation. This new feature is critical for detailed copper “under the component” designs, used to draw heat away from that component.
- Enhanced Parametric Study Functionality. The addition of a “Design of Experiments” scenario table allows users to set up a number of studies to ensure the best coverage of the design field. These scenarios can also be sent to remote machines with more capacity.
- Improved User Interface. Enhancements to the user interface make it easier to set model parameters and find mesh controls for improved thermal design predictability.
- Design Tool Integration. Two approaches are available for tool interoperability in this release. Files can be directly imported through the FloEDA Bridge module with ease-of-use features such as undo/redo, access to power displayed in tree, and the graphical representation of component types. The second approach uses a neutral file format allowing the user to interact with the setup of a model outside of the standard interface.
Sources: Press materials received from the company.
Subscribe to our FREE magazine,
FREE email newsletters or both!Latest News
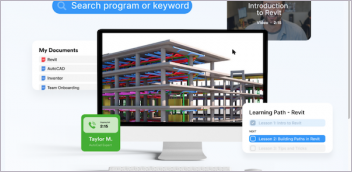

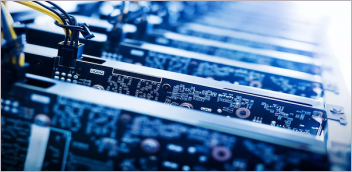
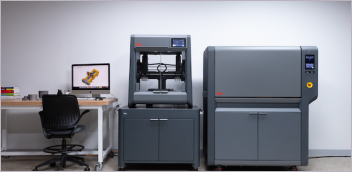