Materialise Takes the Pain Out of Support Generation for Metal 3D Printing

Materialise e-Stage for Metal facilitated powder removal for this drone’s support structure. Image Courtesy of Materialise.
Latest News
November 28, 2017
Optimizing the design and removal of support structures is one of the biggest challenges for all 3D printing technologies, but has been less addressed in the metals world compared to the more entrenched sterolithography (SLA) and other plastics methods.
Materialise, which launched software to tackle the problem for SLA 3D printing, is now expanding its technology to facilitate the design of metal 3D parts. 3D printing metals has taken off the last few years thanks to a variety of factors, including lower printer prices, faster build speeds, and new materials. At the same time, momentum behind Industry 4.0-inspired manufacturing initiatives shift the emphasis to complex designs, bespoke products, simplified assembly production, weight reduction, and overall part efficiencies—all objectives well served by 3D metals printing. As a result, market research firm IDTechEx forecasts the global market for 3D printing metals to reach $12 billion by 2028.
The new Materialise e-Stage for Metal software aims to drive this market growth by automating the support generation, removal and part finishing processes for titanium, aluminum and stainless steel parts. Currently, support generation for 3D metals printing requires expert operators who are well versed in the processes and understand part geometries. While Materialise offers software as part of its Magics suite to help users design supports, the current software still requires them to have knowledge of where to place supports and how many are required.

“Manual support generation takes a lot of effort in the total 3D printing process and needs to be fully automated to comply with the fast growth of metal additive manufacturing (AM) as a mainstream production process,” says Stefaan Motte, vice president and general manager, Materialise Software. Unlike plastic 3D printing processes, it’s far more difficult to create metal 3D printed support structures that avoid shape deformation due to internal residual stress during the build process. “Inadequate support structures often result in scrap by part deformation, breaking of support structures, and building clash,” Motte explains.
Based on advanced algorithms encapsulating Materialise’s almost three decades in the 3D printing industry, e-Stage for Metal is a one-click-solution that automatically generates a fully appropriate support structure for a specific part and materials. Materialise claims use of the software will deliver significant time savings—up to 90% for support design, 50% for support removal, and up to 20% for part finishing. The software also ensures that nearly all of the metal powder trapped in support structures can be reclaimed for further use, and the automated process limits exposure to human error and related build crashes, officials said.

With the introduction of software that streamlines processes and brings added efficiency to metals 3D printing, Materialise is hoping for a game changer that will continue to fuel growth in this rapidly emerging market.
“Traditionally, production set-up comes down to trial and error—printing a lot of variations and converging on what works,” Motte says. “A fully automated process will have a major impact on ensuring a scalable process to push mainstream adoption of AM technology.”
To get a look at how Materialise e-Stage for Metal works, check out this video.
Subscribe to our FREE magazine,
FREE email newsletters or both!Latest News
About the Author

Beth Stackpole is a contributing editor to Digital Engineering. Send e-mail about this article to [email protected].
Follow DE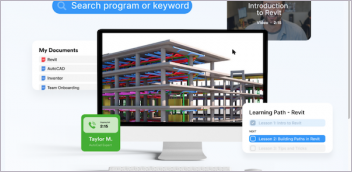

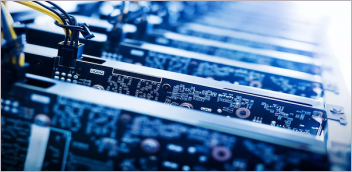
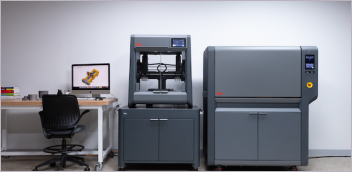