Latest News
March 1, 2005
By DE Editors
Editor’s Pick of the Week: March 30, 2005
No Limit to File Conversions
Bluebeam Conversion Server converts unlimited number of MCAD files for archiving and sharingNewly released, Bluebeam Conversion Server from Bluebeam Software (Pasadena, CA) provides engineering firms an enterprise-wide server solution to handle MCAD-to-PDF conversions painlessly. Leveraging Bluebeam’s Pushbutton conversion technology, this new solution creates a centrally managed server environment for the automatic conversion and disbursal of an unlimited number of MCAD and Windows files to PDF or ten other file formats.
![]() |
The Bluebeam Conversion Server allows your company to set up an unlimited number of watched directories - each with a unique configuration for document control |
Editor’s Pick of the Week: March 23, 2005
UGS Launches Solid Edge 17New massive assembly support and direct editing capabilities essential ingredients in this major upgrade
UGS (Plano, TX) has launched Solid Edge Version 17. Major enhancements include a new Direct Editing capability and massive assembly support functionality. V17 also expands upon the company’s “Evolve to 3D” approach, making the migration from 2D to 3D smoother and easier for holdouts.Solid Edge 17, according to UGS, is the sole major MCAD application to offer direct editing of models without the need to edit the history tree. Direct Editing allows the editing of native complex parametric models “after the fact” without the need to retrace steps in the history tree. Direct Editing also allows the editing of imported 3D geometry from any source, without the need to import features and parameters. With Direct Editing, Solid Edge offers greater interoperability with the company’s NX software, and it helps users to either co-exist with, or migrate from, competitive systems such as Pro/Engineer, Autodesk Inventor, or SolidWorks.Solid Edge’s new massive assembly support capability allows engineers to work on large volumes of data, which, in turn, enables them to create complete digital mock-ups of their largest assemblies. Solid Edge 17 adds a new simplified assembly capability that uses a proprietary algorithm to automatically determine which external faces need to be displayed to give an accurate representation of an assembly. Additionally, a new complementary “structure only” navigation capability lets every engineer use the top-level assembly file as their main point of entry and specifically choose when they want to select the detail of a part or entire subassembly.Solid Edge 17 continues to deliver on the company’s Design with Insight vision and to help users evolve to 3D. For example, it delivers new capabilities to optimize the design of complex products in a hybrid 2D/3D environment; all under the control of the built-in insight for design management. Solid Edge’s four-step “Evolve to 3D” approach is designed to help users migrate 3D in a smooth, efficient, nondisruptive manner; allowing them to get their job done now while learning 3D as they go, mixing and matching techniques in a highly productive hybrid 2D/3D environment.
Version 16 improved Solid Edge’s capability for hybrid 2D/3D design by introducing the “Zero D” capability that allows the definition of product structure before you commit any geometry to paper. Version 17 enhances this capability to include new workflows that allow users to convert existing 3D parts into 2D profiles for efficient 2D design layout, thus allowing streamlined incorporation of existing parts into the hybrid 2D/3D workflow.Solid Edge 17 introduces a new CATIA V4 Translator, a new batch Inventor migration tool, and a third-party ME10 translator from Voyager Partner PROCIM. It already provides translation tools for Pro/Engineer, Mechanical Desktop, and AutoCAD, as well as neutral files like IGES, STEP, and DXF.In addition to these new features, Solid Edge also delivers UGS XpresReview software, a new e-mail-driven solution for design review to complement the existing fully managed collaboration workflow capability of Insight and Insight Connect.UGS expects Solid Edge 17 to begin shipping in April. For complete details, click here. To go directly to a set of online demos, click here.Editor’s Pick of the Week: March 16, 2005
Power Visualization Tool for CATIA nPower’s Power
CatiaToMax for 3ds Max and VIZ makes quick work of once arduous data conversion. Power CatiaToMax for 3ds Max/VIZ improves your design visualization workflow efficiency by importing native CATIA V4/V5 models directly into the advanced 3D modeling and rendering environments of Discreet‘s 3ds Max and Autodesk‘s VIZ without intermediate formats and without losing precision. What this really means is that you no longer have to spend days translating high-quality surface models into imprecise polygonal models or some middleman format, just to spend a few more days struggling to generate high-quality renderings. Developed jointly by the nPower Software division of IntegrityWare and Datakit, Power CatiaToMax uses a precise NURBS-based boundary representation object for accurate modeling. Thus, instead of importing imprecise polygonal approximations, Power CatiaToMax uses a precise representation to generate smooth, crack-free renderings without polygonal artifacts. Power CatiaToMax can handle the large data sets typical of MCAD models, and it offers you detailed control over the tessellation quality, including control over the level of detail, the maximum edge length, arc length, and so forth. Power CatiaToMax performs dynamic tessellation at render time to generate a render mesh with the appropriate level of detail based on the size of the object in the view, eliminating the need for multiple levels of detail. Power CatiaToMax contains a variety of tools to clean up, prepare, and render CATIA models. Among these are automatic and manual sewing tools, tools to quickly orient surfaces, trim and un-trim surfaces, and snap to imported objects. To speed up data translation further, its tessellation engine can leverage multiple processors by dividing up the work into separate processes. Tessellation performance will scale with the number of processors available for optimal performance results. The result is a performance improvement of about 2X for dual processors, and about 4X for quad processors. Power CatiaToMax for 3ds Max/VIZ costs $2,995. It can be purchased through the nPower website, where you can also arrange for a free 30-day evaluation version.
Editor’s Pick of the Week: March 9, 2005
Build Libraries of Your Best Practices
EASA simplifies enterprise access to technical software expertise
EASA (Enterprise Accessible Software Applications) software from EASA Software and Services division of AEA Technology is both a methodology and a toolkit for building applications libraries of your in-house expertise that are accessible across your enterprise. EASA enables engineering and manufacturing organizations to quickly create vertical applications that drive their existing complex software, such as CFD, FEA, process simulation, or homebrewed codes, yet mask that complexity from nonexpert users.EASA provides a Web-based environment to drive complex applications, and, being Web-centric, it minimizes deployment hassles. Its tools allow engineers to capture their experience and knowledge as they apply complex software. What this means is that EASA guides your, say, ANSYS expert setting up an intricate analysis. From this data, EASA builds an application that is less awesome on its surface, yet equally as powerful in fact because it is running the high-powered ANSYS analysis. Thus, nonexpert users can use this vertical application to run complex analyses that would normally be over their heads.The net result is that EASA ups productivity because the expert is freed to do other more demanding analyses and projects are not placed on hold waiting for the expert’s attention. Further, your company’s software investments are more thoroughly maximized.The EASA applications builder offers tab-based, tree-based, or wizard-based interfaces that lead the users through the application without requiring any code writing. EASA offers connectivity to common relational databases as well as a suite of security features.EASA runs on a Windows 2000, NT, XP or Linux servers. Your application library and results are stored on the server. Users communicate with the EASA server via their Web browsers. EASA drives the underlying software application wherever it resides, and it supports communications with applications running on Windows, UNIX, or Linux.See DE‘s November 2004 Web Exclusive “Automate Your Analysis” for a more complete discussion of EASA. For additional details or to request a free demo CD, go to the EASA Software and Services website.
Editor’s Pick of the Week: March 2, 2005 Publisher Makes Design Communication Automatic Actify also plans “significant announcements” at National Manufacturing WeekActify Inc. (San Francisco, CA) last week made digital design communication across the enterprise and supply chain easier when it announced Actify Publisher 2005, an automatic batch publishing application that converts native MCAD files into company’s .3D file format. In a related news item, Actify has said that it plans to make two significant industry announcements at the National Manufacturing Week show in Chicago next week. Actify Publisher 2005 lets you define and manage all aspects of the digital design publishing process, including which source MCAD files to automatically publish, where to post the newly published files, and who to notify of the completed process. When combined with SpinFire Professional, SpinFire Reader, and Actify Server, Actify Publisher enables secure distribution of multiple 2D and 3D MCAD file formats throughout enterprises and supply chains, without requiring all users to have access to native MCAD systems.
Actify Publisher enables you to create a job that defines your unique set of rules for .3D file publishing, such as which files to publish, when to publish them, and where the published files should be posted. With it you can quickly and automatically publish a large archive of native MCAD files through a single central source.Once you automate the Actify Publisher process, you have created a consistent, consistently accurate, and repeatable process. The process guarantees publication of all files, and the automated publishing process ensures the timeliness of conversions. All this, in turn, lowers your MCAD data management costs and eliminates time spent manually publishing files one by one. According to Actify, another benefit of Actify Publisher 2005 is the software’s ability to centralize all importers to one computer, which reduces software and maintenance costs from many computer users to a single system. Actify Publisher 2005 integrates within current, standard network file systems and within current network share permissions. No new setup is necessary. In Chicago next week (March 7-10) during National Manufacturing Week, Actify said it will make two “significant industry announcements” that demonstrate how its suite of products make 2D and 3D data more broadly available to information users. “Our goal is to give everyone, both technical and non-technical workers, the ability to view whatever CAD files they want, whenever they want, regardless of the format the document is created in,” said Randy Ochs, President and CEO. “Actify’s announcements next week will significantly alter how the information workers are able to use 3D and 2D design data in an easy, more flexible software environment.“You can visit the company in its booth, number 4218, or in the Microsoft booth, number 4811, while at National Manufacturing Week. If you cannot make it to Chicago next week, you can find full details on Actify’s digital design communications product portfolio on the company’s website.
Subscribe to our FREE magazine,
FREE email newsletters or both!Latest News
About the Author

DE’s editors contribute news and new product announcements to Digital Engineering.
Press releases may be sent to them via [email protected].
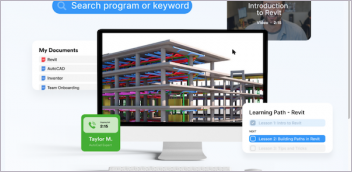

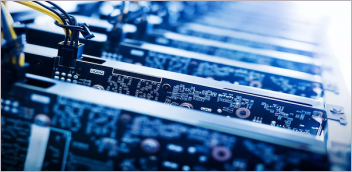
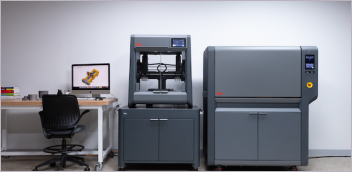