Manufacturing Accelerated

Latest News
December 1, 2016
Design Engineers are constantly called on to speed new products to market. To meet this challenge now and into the future, engineers need suppliers capable of delivering prototypes and parts for those products on time and on budget.
Enter Proto Labs. We are the world’s fastest digital manufacturing source for rapid prototypes and on-demand production parts.
One Company, Three Services
Our global company is well suited to serve as a manufacturing partner with design engineers through our three distinct services that produce custom parts for companies around the world:• 3D Printing (Additive Manufacturing)
• Injection Molding (which also includes Rapid Overmolding)
• CNC Machining (Milling and Turning)
Proprietary software and automated processes drive our rapid prototyping and low- to mid-volume production of metal, plastic, and liquid silicone rubber parts.
Speed to Market
Our rapid manufacturing capabilities start with ProtoQuote, our online, automated quoting and design for manufacturability (DFM) analysis engine. Product developers can upload 3D CAD models online and receive an interactive quote with free design analysis and real-time pricing within hours. The design analysis highlights potential issues and provides immediate solutions. It’s an iterative process that helps design engineers avoid product development speed bumps.
On-Demand Production
Next, we manufacture and ship quickly. How fast? We can deliver one to 50-plus 3D-printed parts in one to seven days. For machining, one to 200-plus CNC-machined parts can be shipped in one to three days. And, 25 to 10,000-plus injection-molded parts can be delivered in one to 15 days. Our on-demand manufacturing capabilities can help companies effectively manage demand volatility and inventory costs, and help reduce overall risk.
Success Stories
We’ve helped thousands of companies work smarter and faster:
• Brunswick Corporation recently turned to our 3D printing and injection molding services for low-volume production parts for its Sea Ray luxury yachts.
• Lockheed Martin used rapid injection molding for parts for a quadcopter drone.
• University of Houston chose quick-turn CNC machining to develop exoskeleton prostheses for paraplegics.
• The Metropolitan Museum of Art used our 3D printing service to build miniature scale models for its exhibit on ancient Egypt.
Subscribe to our FREE magazine,
FREE email newsletters or both!Latest News
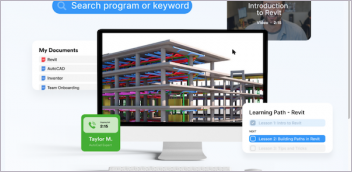

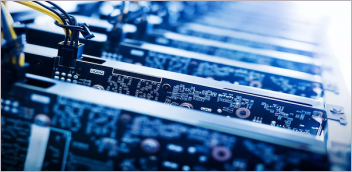
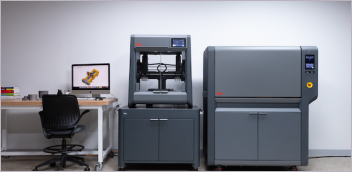