Latest News
December 1, 2011
By Brian Shepherd
Editor’s note: This commentary was sponsored as part of DE’s Visionary Voices section.
Assuring product quality, reliability, and safety is an integral part of product development. Yet many manufacturers perform quality checks too late in their process to be effective. A clearly defined method to track a product’s quality against its requirements throughout the development cycle can help manufacturers avoid shipping faulty or unsafe products as well as budget-busting expenses such as scrap, rework, postponed product launches, or, worse, mid-project cancellations. Quality Lifecycle Management (QLM), an emerging enterprise-wide solution, provides manufacturers a formalized system to manage product quality, reliability, and risk from the onset of product development throughout each successive stage of a product’s lifecycle. But just what does QLM entail?
QLM is a cross-functional solution that integrates quality and reliability analyses, risk planning, field use data, and even customer complaint tracking/resolution into every facet of product development from concept to management. It makes product quality data readily accessible to all stakeholders, whether their job is planning, design, testing, manufacture, service, or oversight. QLM helps manufacturers align functional needs from every potential source with requirements by systematically tracking a product’s characteristics at every lifecycle stage. It ensures that a product’s characteristics match its requirements and arms manufacturers with the data needed to address quality issues proactively before failures manifest themselves.
A Unified Platform
A successful QLM solution seamlessly integrates analysis methodologies to enable cross-functional quality activities, enterprise-level accessibility in support of personnel collaboration, and structured workflow tools to implement closed-loop quality processes. To accomplish all this, QLM unifies within a single database platform several methodologies commonly used to fulfill quality, reliability, and safety-related analyses throughout the product development lifecycle. Among these are predictive analysis to calculate the probable failure rates of components and systems; fault-tree analyses to quantify system risk and reliability; failure mode and effects analysis; failure reporting, analysis, and corrective action; nonconformance handling; and customer feedback tracking and reporting.
In practice, what this means is that QLM organizes a workflow in which everyone is in the know. Design engineers know the precise criteria defining the parts they select in support of functional requirements. Test engineers know exactly what characteristics to examine and what their minimum performance specs need to be. Manufacturing knows what attributes require intense control during production to achieve product safety and performance benchmarks, while service technicians know where to focus during routine maintenance or repairs. Planning knows what’s right and wrong with the current iteration of a product. Management knows that its visibility into product performance at every lifecycle stage is complete.
Collaboration and Correlation
Collaborative methodologies are a key attribute of QLM. They make certain that quality information garnered in one lifecycle stage is communicated in a timely and accurate manner to the relevant processes in all other lifecycle stages. For example, one of the central functions of QLM is to investigate any correlation between field failures and manufacturing, component, or design defects. QLM maintains a closed loop system that relays quality issues experienced during service and use back to quality planning, design, testing, and manufacture. This enables manufacturers not only to record, disseminate, and react to lessons learned—but to retrieve and apply those lessons in next-generation products.
Too often, manufacturers short-shift product quality checks for reasons ranging from time to market to coping with globally disbursed workforces and supplier networks. Too often, the result is disastrous. QLM enables manufacturers to leverage quality control as an everyday component of their product development process.
Brian Shepherd is Executive Vice President, Product Development, PTC.
Subscribe to our FREE magazine,
FREE email newsletters or both!Latest News
About the Author

DE’s editors contribute news and new product announcements to Digital Engineering.
Press releases may be sent to them via [email protected].
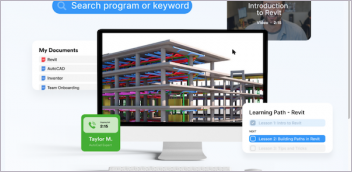

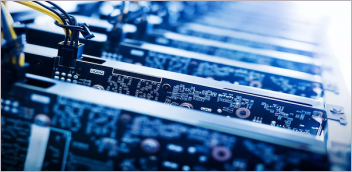
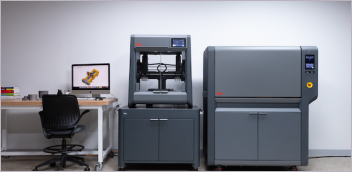