Making Sense of Industrial Connectivity Trends
Today, the industry sees M2M as a set of technologies that connect machines, devices and objects in a way that helps them exchange information without human intervention.
Latest News
November 1, 2019
The industrial arena has witnessed a constant drive toward greater connectivity. The 1980s and 1990s saw the sector come to terms with fieldbus technology. In the early 2000s, machine to machine (M2M) communications took root. Today, concepts like Industry 4.0 and the Industrial Internet of Things (IIoT) have taken center stage.
If you stop and consider the larger picture, many questions arise. For example, are Industry 4.0 and IIoT just new names for M2M communications, or are these distinctively different concepts? If they have different meanings, how will these trends affect future industrial ecosystems?
Basic Concepts
Today, the industry sees M2M as a set of technologies that connect machines, devices and objects in a way that helps them exchange information and perform actions without human intervention. Essentially, M2M allows almost any sensor to communicate with another system. This lets systems monitor themselves and automatically respond to changes in machine health or ambient operating conditions, with a much reduced need for human involvement.
In the industrial context, M2M promises to reduce costs by optimizing maintenance and minimizing machine downtime. This opens the door for improved customer service by avoiding equipment failure through proactive monitoring and servicing of production resources.
Although M2M is closely related to IIoT, the two are not synonymous. At its core, IIoT connects plant floor equipment and business systems, creating cyber-physical systems that provide new ways of generating, collecting and analyzing relevant data throughout the industrial space. IIoT focuses on providing visibility down to the lowest points of the production floor, enabling predictive maintenance and big data analytics.
The biggest difference between M2M and IIoT is scale. M2M is often more localized, integrating machines in one or a few facilities. IIoT is horizontal, combining production and business systems on a global scale, with an eye toward improving overall equipment effectiveness and providing new business insights.
Industry 4.0 builds on M2M and IIoT, viewing connectivity and operational efficiency on a grander scale. This concept blends digitalization, advanced technology and new business practices in the hope of dramatically changing how companies manufacture products.
Similarities and Differences
The M2M and IIoT concepts relate to connected device communication, but M2M systems are often isolated, stand-alone networked equipment. IoT systems, on the other hand, take M2M to the next level, bringing together broadly distributed, disparate systems into one large, connected ecosystem.
Other distinctions also come into play. M2M, for example, takes the form of closed, hardware-based systems that use non-IP protocols for communication. These systems often rely on point-to-point communications to link embedded systems in vertical applications, using structured data to perform control and service management functions.
IIoT systems, on the other hand, are software-based, horizontal applications that communicate via IP protocols. IIoT systems use structured and unstructured data to perform multiple, multi-level applications, and support almost unlimited integration options.
The distinction between IIoT and Industry 4.0 lies in the difference between the physical and the theoretical. Proponents see IIoT as a set of existing enabling technologies for digital transformation.
Industry 4.0, on the other hand, embodies a theoretical description of future manufacturing, focusing on enterprise-wide business process automation, with the aim of creating new models that may lead to new interactions across the supply chain.
Just Getting Started
M2M technology has already established itself in the industrial sector. IIoT and Industry 4.0, however, have only just started to find their footing, with proponents and technology providers still defining future manufacturing ecosystems. Each concept provides its own unique perspective on smart connectivity, and each will play a role in shaping future industrial ecosystems.
Subscribe to our FREE magazine,
FREE email newsletters or both!Latest News
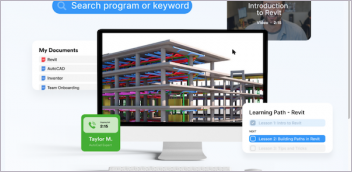

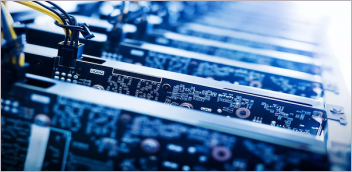
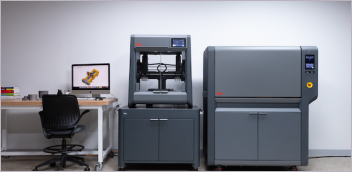