Latest News
December 1, 2012
By Tim Caffrey and Terry Wohlers
![]() | ![]() |
Tim Caffrey (left) and Terry Wohlers |
Our first resolution for 2013 is to use the terms 3D printing and additive manufacturing (AM) interchangeably. Many from the scientific and technical communities prefer AM, especially for industrial systems. About everyone else, including bloggers, the investment community and the mainstream press, prefer 3D printing. There’s no going back to the old definition of 3D printing, which once meant an AM process that jetted material through an inkjet print head.
In a perfect world, manufacturing processes would use 100% of raw materials in finished products. As we head into 2013, we still don’t live in a perfect world, but AM can get us closer. AM processes yield near net shape products with relatively little waste.
One glaring exception, however, is the recyclability—or lack thereof—of polyamide powders used in powder bed fusion processes. Currently, more than a third of the unused powder in a build cannot be reused. In 2013, we’d like to see process and material improvements that make unsintered nylon powder 100% recyclable, build after build after build.
Also, material used to support parts as they are built also becomes waste. Optimizing the support material helps, but they still have an impact on cost, build time and the amount of scrap.
Shedding Weight
One of the most common New Year’s resolutions is to go on a diet. There are ways for AM parts to shed some weight, too, yet still maintain their strength and functionality. Topology optimization software uses algorithms to produce a design that satisfies strength and stiffness requirements while minimizing the amount of material used. Mathematics decides where to put the material.
“TopOp” often results in an organic form that mimics the shapes found in the natural world. And, with AM’s inherent ability to build any shape or geometric feature that can be modeled digitally, TopOp is an ideal “dietary supplement.”
Lattice and mesh structures are another great way to drop a few pounds. Software, such as Within Enhance, netfabb’s Selective Space Structures, and 3D Systems’ Conformal Lattice Structures, reduces a part’s weight by transforming solid areas into surface skins with interior volumes composed of lattices with open spaces, while maintaining requisite strength and stiffness.
What’s so great about weight loss? A “ton” of things. Less raw material is consumed, and that saves money. The strength-to-weight ratio of parts is optimized. The build is faster because less material needs to be processed. Plus, lighter weight parts reduce fuel consumption and transportation costs.
Complexity Is Simple
Topology optimization and lattice structures are great theoretical concepts. And that’s what they were—theoretical—until AM came along. Conventional manufacturing can’t produce convoluted features or encapsulated lattices, at least not affordably.
Herein lies AM’s ultimate optimization advantage. Designers are no longer constrained by design-to-manufacture issues like undercuts in molded parts or multiple setups in CNC machined parts. Almost anything a designer can create using design software can be manufactured by AM.
As we enter 2013, our educational systems must catch up to this new reality. Curricula should not only add 3D printing to manufacturing process options, they should also teach students that AM processes provide design freedom, liberated from the shackles of 20th-century manufacturing.
AM offers the opportunity to reduce material use and waste, optimize the strength-to-weight ratio, and provide radically new designs. It is our hope that engineers and designers, young and old, will embrace this new way of thinking—and explore what could become the most important and popular method of manufacturing in the future.
Tim Caffrey is associate consultant at Wohlers Associates. Terry Wohlers is principal consultant and president of the consulting firm. Send e-mail about this article to [email protected].
Subscribe to our FREE magazine,
FREE email newsletters or both!Latest News
About the Author

DE’s editors contribute news and new product announcements to Digital Engineering.
Press releases may be sent to them via [email protected].
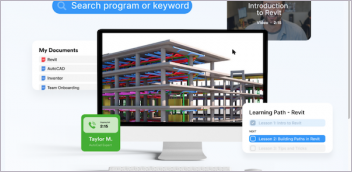

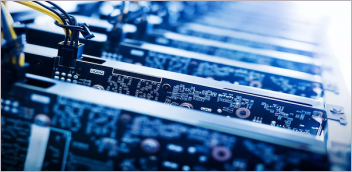
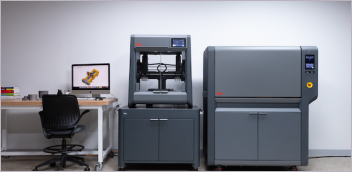