Latest News
August 1, 2006
By Joel Cassola
It’s just a little part that fits in a breadbox. However, about one-third of it consists of complex contoured surfaces that account for the bulk of a 30MB NC (numerical control) program and nearly a million lines of code. It takes around 118 hours to machine just one of these parts from a solid block of 7075 aluminum with a Haas 5-axis milling machine. This part inspired Mike Giboney to change the way his company, Tooling & Assembly Solutions (Simi Valley, CA), programs its NC equipment.
Until he got this job, Giboney was relatively satisfied with an add-on program he used within the CAD environment to generate toolpaths. It did everything he needed it to do, though Giboney suspected it was a little slow. He was planning to do some product comparisons when he could find the time, then he began programming the challenging 5-axis aerospace part.
Overhead Issues
Tooling & Assembly Solutions is a 10-year-old high-tech 8-person shop that specializes primarily in tooling, fixtures, and components for custom automation systems and the aerospace and medical industries. Giboney has made a substantial effort to design and assemble CNC manufacturing equipment and QC automation, which allow not only for high precision and productivity of the individual systems, but rapid transitions from one manufacturing phase to the next.
|
Cutting the toolpaths. |
> > Complex contoured surfaces account for most of the 30MB of machine code generated by Mastercam for cutting this complex aerospace part.
He became frustrated, however, when the transition from design to 5-axis programming for this latest aerospace part ran into a bottleneck. He understood that creating the CNC program for the part’s complex surfaces would be time-consuming. But after spending 40 hours working in the CAD environment to generate his CAM program and completing only three of the part’s 14 operations, Giboney saw he needed a different approach.
“When you start adding a lot of geometry and toolpaths to your model,” he says, “you really increase overhead. The computer starts churning and grinding all these numbers and it slows down, badly.”
Using the same environment for both CAD and CAM seems to compound the problem. “Like a good CAD system, our CAD module spent a lot of time looking for changes and updating toolpaths. It would sometimes take 10 or 15 minutes scanning the file as it was being opened.” Giboney decided that for this type of part the CAD world and the CAM world needed to be in separate environments.
|
Mastercam in operation. |
< < For parts with detailed surface machining, Mastercam’s ability to cleanly import geometry directly from the solid model (in this case SolidWorks) can save hours of programming when compared to other systems.
That was in February of 2004. Giboney talked to a number of vendors and friends in the business before purchasing Mastercam 9 multiaxis software from CNC Software in Tolland, CT. Giboney compared Mastercam to a powerful engine dedicated exclusively to optimizing the productivity of his fabrication environment. For parts with a great deal of surface machining, Mastercam’s ability to import geometry directly from the solid model can save hours of programming when compared to programs that require the creation of sketches to delineate surfaces. He also found that the program was flexible with regard to selecting optimized tool sets for complex parts that require many operations. This can ultimately save many hours of machining per part.
The aerospace part was one of the first Giboney programmed using Mastercam. The SolidWorks model flowed seamlessly into the Mastercam environment. It took Giboney 30 hours to program all 14 operations. When he was done, the software spent seven minutes to generate all of the code for the toolpaths.
|
Finished part. |
> > It took Mike Giboney just 30 hours to generate toolpaths for this heavily contoured aerospace part using Mastercam. Cutting one of these on a five-axis machine took about four times longer than that.
“A file ]like that] would have taken the other software two hours to create,” he said. “Things are getting faster, simpler, less expensive, and easier to use and I think probably some day the design and fabrication world may be combined. But at this stage of the game it is more efficient to keep them separated. Anyway, if you do change something at the machine, it can flow backwards through Mastercam into SolidWorks. It’s all pretty seamless.”
Newfound Productivity
Tooling & Assembly Solutions is now in its third year of using Mastercam. It provides the company with a clean transition from design to manufacturing. Giboney has installed SolidWorks and Mastercam on the same workstation and he spends about half of his time using each of these programs. However, customers send Tooling & Assembly many different file types as CAD models. Mastercam’s library of plug-ins allows the company to import and work with all of them.
“Mastercam does a very nice job importing the geometry and not giving you corrupt data,” Giboney said. “Whether it’s a Pro/E, SolidWorks, or an IGES file, Mastercam gives us a very clean translation. If the source file happens to be corrupt, Mastercam has tools that make it easy to clean up.”
Tooling & Assembly Solutions became a beta site for Mastercam X about six months before its commercial release, and has now been using it for about a year. Giboney thinks the basic functionality of the two versions of Mastercam are nearly the same. However, he was pleased to find that Mastercam X has a layer of artificial intelligence operating in the background to make the things he does routinely faster and easier.
|
The author in a less stressful moment. |
< < Mike Giboney keeps SolidWorks and Mastercam on the same workstation and splits his time evenly between the two.
For example, extend and trim functions have been combined into a single operation. Something he might do 100 times during a complex programming session has been effectively cut in half. The system also automatically remembers the functions he uses most frequently and puts buttons for them on the screen in a place that is readily accessible. If there is no model, quick fabrication features make it easy to perform basic operations, like drilling a few holes, using simple drawing tools to indicate where they should go.
“Mastercam is so simple. I don’t bother doing anything ahead of time anymore. I used to spend Saturdays getting the models ready for programming. I don’t do that any more. Now when it’s time to run, I get out the drawing, open Mastercam and import the model. Or, if I don’t need to have a model—say I’m just drilling holes in a flat plate—I draw my circles on the screen. Then I generate my features, pick my tools, post it, and run it.”
Shop owners used to brag about how many CAM stations they had. Giboney says he brags about how few. “In the old days you would have a programmer who would be given a whole list of drawings and he would program all day long. Today, I do all of the programming for this shop and I also assist with setups. Some days I make 20 programs in Mastercam—20 different operations. I can personally keep four CNCs busy all day long, two shifts, frequently doing five or six setups a day.”
With Mastercam, Tooling & Assembly Solutions has avoided the cost of hiring an additional CAM programmer over the past two years. More importantly, Giboney has maintained hands-on involvement in the operation of his business, allowing him a pivotal role in keeping it operating at peak efficiency.
Joel Cassola is a freelance business feature writer specializing in manufacturing systems and productivity software. He lives in Cranston, Rhode Island. Send your comments about this article through e-mail by clicking here. Please reference “5-Axis Part, September 2006” in your message.
Company Information
Haas Automation, Inc.
Oxnard, CA
Mastercam
CNC Software, Inc.
Tolland, CT
SolidWorks Corp.
Concord, MA
Tooling & Assembly Solutions
Simi Valley, CA
Subscribe to our FREE magazine,
FREE email newsletters or both!Latest News
About the Author

DE’s editors contribute news and new product announcements to Digital Engineering.
Press releases may be sent to them via [email protected].
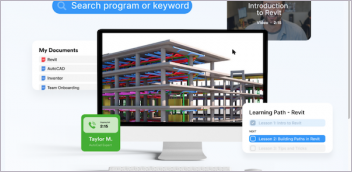

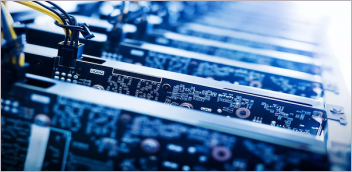
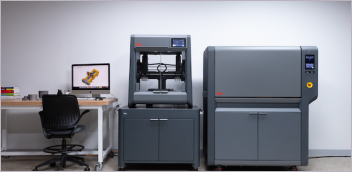