Leading the Way in Aerodynamic Design
Computational fluid dynamics simulation helps reduce drag and improve acoustic performance of GM's electric vehicle.
Latest News
June 1, 2010
By Russell Shuba
In designing its new rechargeable electrical vehicle, the Chevy Volt, General Motors (GM) decided a combination of wind tunnel and computational fluid dynamics (CFD) simulation would reduce the time needed to obtain accurate vehicle drag and cooling airflow analysis results. The process meant the engineering team could use more geometric detail than is practical with a clay model, which enhanced flow visualization capacity around the vehicle for diagnostic purposes. The combination of the wind tunnel testing and ANSYS FLUENT made it feasible to achieve aggressive range and fuel economy targets.
![]() The Chevy Volt’s external aerodynamics simulation was accomplished using ANSYS FLUENT CFD. |
The aerodynamics team starts with concepts and ideas provided by the design studio. The process proceeds with a considerable amount of interaction between the studio and the aerodynamicists. The designers work to preserve the theme of the vehicle, and the aerodynamicists provide feedback on shape changes and modifications that could be used to reduce the vehicle’s drag. The bulk of the wind tunnel testing is performed on a one-third-scale clay model that is continually modified to evaluate various design alternatives.
“While the wind tunnel plays the primary role in the aerodynamic design process, we find ourselves in situations in which wind tunnel testing does not make sense, either because there isn’t enough time to perform tests or because we can’t build a clay model of the geometry to the level of detail that we need,” said Ken Karbon, staff engineer for GM. “In these situations and others, we use ANSYS FLUENT CFD software to simulate aerodynamic performance.”
Karbon added that the team can easily set up an automatic batch run to evaluate several hundred different front-end airflow configurations over a weekend—unattended. Fluid dynamics simulation also provides the ability to model the underhood geometry to a much higher level of detail than is possible with a physical model, and in a reasonable period of time.
Efficient Simulation Process
To reduce the time required to analyze the large number of iterations needed to optimize a design, an efficient simulation process is used to automate a considerable portion of the model setup process and makes it possible to semi-automatically run many test points without user interaction. Engineers wrapped a workflow toolkit around the fluid dynamics software that guides the user through preprocessing, meshing, case preparation, job submission, postprocessing, and reporting. The models generally are submitted to a high-performance computing cluster built around IBM POWER6 blades. Engineers use these capabilities with design of experiments (DOE) or design for six sigma to explore large design spaces and identify the global optimum design.
![]() FLUENT CFD was used extensively to develop the front end cooling airflow characteristics of the new Chevrolet Volt. |
In the case of the Chevy Volt, aerodynamics engineers obtained CAD data from the design studio in Siemens PLM NX format. The team used the CFD software’s preprocessor capabilities to build a tetrahedral or hex-core mesh of the volume surrounding the vehicle’s outer surface with a prism layer next to the body to capture boundary layer gradients. Volumetric refinement was used to capture gradients in other areas of interest, such as the wake and stagnation points. Boundary conditions were defined to match the wind tunnel.
“For the styling surfaces, we applied classic automotive aerodynamics best practices by ensuring smooth continuous airflow around the vehicle,” Karbon said. “We entrained smoke in the wind tunnel to provide a high-level macroscopic picture of flow direction. CFD allows us to see much more than could ever be obtained from physical testing.” Karbon noted examples such as pressure differentials both fore and aft of underbody components. The GM team also pays close attention to large separation points or vortex structures coming off the vehicle because of the potential for resulting in aerodynamic drag. Karbon added that engineers also target “very clean separation from the back of the vehicle.”
Fluid dynamics analysis played the primary role in designing the grill, radiator, and related components to obtain the right amount of airflow through the grill, to direct the airflow to where it is needed, and to minimize cooling drag.
“We looked at the pressure and velocity profiles to understand how the air comes through the grille openings,” said Karbon. “We needed to make sure we were getting enough volume of air to meet the most demanding engine cooling load cases, such as driving the car through the Death Valley desert.”
To solve specific problems, engineers created large arrays consisting of hundreds of design variations and used parallel batch, scheme, and journal processing to quickly analyze all of them. This made it possible to quickly model various design details such as grill openings, grill texture, air dams, heat exchanger size and position, and sealing and baffling underneath the hood.
The engineering team also used FLUENT to mitigate and optimize wind noise associated with the Volt’s wiper blades. Engineers first determined pressure and flow velocity generated by the wipers during the concept design phase. This information was used as input by software developed to predict acoustic performance. The evaluation of wind noise at an early stage of the design process helped avoid later-stage problems that would have been costly to correct.
Fluid dynamics analysis also predicts wind loads on vehicle components such as sunroofs and windows, especially under crosswind conditions. This information is fed into structural analysis programs used to ensure that all components meet high-speed requirements. CFD also estimates the temperature and quality of underhood airflow to the powertrain induction system.
“CFD plays a vital role in aerodynamic and acoustic design by highlighting the areas we need to work on and by providing diagnostic information that we cannot obtain in the wind tunnel,” Karbon said. “The technology also makes it possible to quickly evaluate hundreds of designs in batch processes to explore the complete design space so that we knew we had the best possible design.”
More Info:
ANSYS
Russell Shuba is a freelance writer who lives outside Madison, WI. When he’s not tracking down the details of his latest assignment, he can be found plying the north country’s lakes in a homemade kayak or skiing in the backcountry. To comment on this article, send us an e-mail addressed to [email protected].
Subscribe to our FREE magazine,
FREE email newsletters or both!Latest News
About the Author

DE’s editors contribute news and new product announcements to Digital Engineering.
Press releases may be sent to them via [email protected].
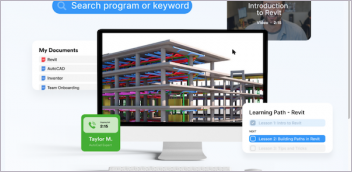

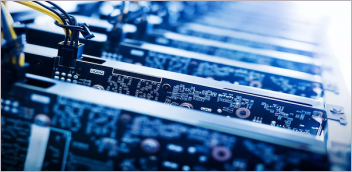
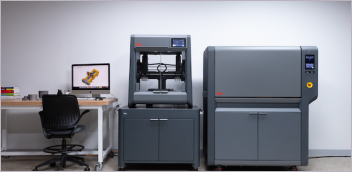