Latest News
June 19, 2017
The latest release of VISI, Vero Software’s specialist mold and die solution, delivers various user experience enhancements and addresses an issue that is often neglected, Vero Software reports.
When the sheet metal part is removed from the die, and the forming forces released, material elasticity will cause the part geometry to experience springback. The new springback prediction functionality in VISI 2017 R2 is designed to reduce the time and cost of a typical trial-and-error approach to solving this industry issue, the company notes.
“Springback can make it difficult to control the part’s final dimensions,” VISI Brand Manager Massimo Vergerio says. “The new prediction tool starts from the nominal part, material data and blank calculation, generating a second mesh of the product’s geometry after springback. The designer can then achieve a morphing on the surface with the relative compensation tool, which generates the required compensated surface, producing the accurate die faces for the required sheet metal part.”
When a designer is validating the part for formability, a new graphical analysis representation mode will subdivide the results into six possible zones that occur during the forming process:
- Strong Wrinkle Tendency: slight stretch in one direction, and compensation in the other, with material thickening
- Wrinkling Tendency: stretch in one direction, and compression in the other, with slight material thickening, which may cause wrinkles to occur
- Low Strain: minimal stretch or compression in either the major or minor directions
- Safe: area below the Forming Limit Curve where failure is unlikely to occur
- Marginal: the area between the safe and fail zones, where the forming process is marginally safe
- Fail: the area above the Forming Limit Curve where splitting and localised thinning is likely to occur.
High speed machining can now be achieved with the new 2.5-Axis Waveform Strategy (previously available in 3D roughing), which maintains constant tool cutting load, constant cutting feed rate, and a smooth toolpath.
Based on the Pocketing technology, the new Remachining Strategy inherits the same enhancements and advantages. Rest area recognition is achieved automatically, based on the reference operations. A new residual stock algorithm is used for both 2D and 3D operations and the Dynamic Incremental Stock command.
The new Electrode machining module automates the electrode design-to-manufacturing process. It benefits from all the relevant electrode data added by the operator during the electrode creation phase, while also removing the potential risk of possible input error.
Where a substantial number of electrodes need to be machined, the new module automates the process.
Other important enhancements introduced include the following: New Product Launcher, a customizable software starting window that provides access to the complete suite of installed VISI applications; improved wire EDM technology and software fixes and updated CAD translators.
For more info, visit Vero Software.
Sources: Press materials received from the company.
Subscribe to our FREE magazine,
FREE email newsletters or both!Latest News
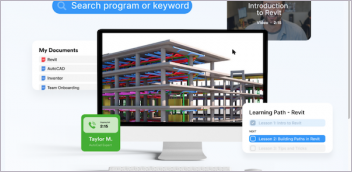

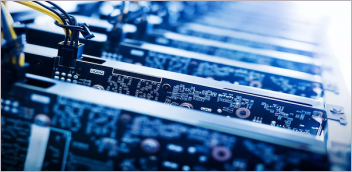
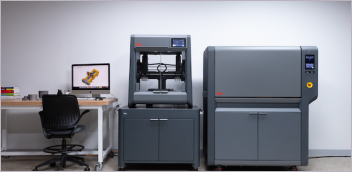