Latest News
October 1, 2014
Automotive and aerospace manufacturers were the first to recognize the economic benefits of lighter designs. Planes and cars that weigh less require less fuel to fly and drive. This fuel economy is an attractive proposition to owners and operators because it yields significant savings over time. However, the strategy to keep the products as light as possible must be carefully weighed against passenger safety, industry mandates and manufacturing cost.
Jerad Stack was founder and CEO of Firehole Composites, acquired by Autodesk last year. He joined Autodesk as a Senior Product Line Manager for Advanced Materials after the acquisition. In an interview with DE, Jerad discusses the challenges with lightweighting.
Desktop Engineering: What is the role of advanced materials in lightweighting?
Jerad Stack: Advanced materials—specifically, composite materials—have been around for some time. For example, the use of carbon fiber in automotive is not new. But now the manufacturing techniques and cost have gotten to the point where they can be used more widely. With lightweighting, people usually use carbon fiber composites—thin pieces of carbon fiber held together by plastic or epoxy. They’re as strong as metallic materials, but significantly lighter. So if you figure out how to build the chassis of your car using this type of material, for example, you could reduce as much as 75% of the chassis’ weight.
DE: Are current digital prototyping software programs capable of replicating the behaviors and characteristics of composite materials?
JS: Five or ten years ago, they could not. But we have since made great strides in understanding the physics of these materials. Autodesk is making internal investments and acquisitions in this area so you can have as much confidence in simulating them as you do with traditional manufacturing materials.
DE: What products are applicable to lightweighting projects?
JS: The first one is our Moldflow product line. Its legacy is in injection molding, and the molding of glass fiber-reinforced plastic composite parts is everyday business. There is more and more interest in the stronger carbon fiber-filled materials because they reduce weight further. With our Moldflow simulation products, orientation of the fibers as a result of the manufacturing process can be calculated, and the effect on form, fit and function can be calculated. The other one is the Simulation Composite product line. The key product is Simulation Composite Analysis. Whether you’re designing an airplane wing or the bumper of a car, this allows you to make reliable stiffness and strength predictions.
DE:What do manufacturers simulate in lightweighting projects?
JS: It’s a little different from what you might with, say, stress analysis of traditional materials. Because composite materials are more advanced, they require different manufacturing techniques. You can’t cut them out like sheet metals. So you’re trying to find out (1) if you can manufacture the composite materials you need; and (2) how to optimize the manufacturing process. Say you’re thinking of using compression molding to produce them. You’d want to know, what are the pressures you need to put on it, and what size mold should you build? Moldflow can help answer these questions. Just like you’d want to find out if a cellphone might shatter when dropped from a certain height, you’d want to find out how many cycles your composite part can operate before it starts to show cracks. They behave very differently, so you need a specialized tool, like our Composite Analysis package.
DE:Are the composite simulation products preloaded with properties of composite materials?
JS: Material properties without consideration of the material orientation of the glass or carbon fibers is almost meaningless. The Moldflow products come with a material database of over 9,500 plastics to calculate the actual as manufactured properties, accounting for the fiber orientation. Our Composites Design products include a database of 300 standard composites, and within the product the direction, ply thickness and ply build up can be optimized for optimal strength.
For more on Autodesk composite solutions, visit:
This content is sponsored by Autodesk.
Subscribe to our FREE magazine,
FREE email newsletters or both!Latest News
About the Author

DE’s editors contribute news and new product announcements to Digital Engineering.
Press releases may be sent to them via [email protected].
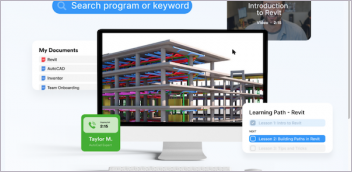

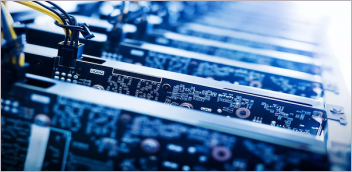
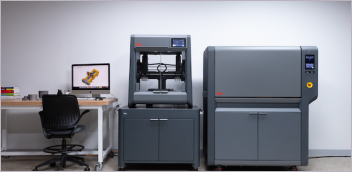