Intelligent Layering Puts 3DEO on Fast 3D-Print Track

Sample metal parts 3D-printed on 3DEO’s industrial AM system. All parts are 17-4PH stainless steel, shown directly out of the machine with no post-processing; the largest is about 2 inches diameter. (Image courtesy 3DEO)
November 10, 2017
Packed in with the other 5,000 (well, maybe 500) products featured at last May’s high energy RAPID+TCT 2017 exhibit was a new metal additive manufacturing (AM) approach from 3DEO (Los Angeles). Termed Intelligent Layering, the process combines layer-by-layer micro-end-mill cutting with a bulk sintering approach to produce metal parts with a superb surface finish.

3DEO’s vision is to provide low-cost, high-volume, high-quality metal AM part production and services. To that end, now, six months later, the company has already moved into a 13,000-sq.-ft. facility, expanded from three to eight beta-stage machines, and offers such secondary operations as heat treating, vibratory-deburring, machining and a range of quality control and metallurgical inspection tasks. That’s a big jump—and it’s not slowing down.
Aiming Directly at High-Volume Manufacturing

At the RAPID+TCT event, the big-picture to-do list identified in a keynote panel by 3D Systems president Vyomesh Joshi included productivity, repeatability, durability and how to achieve those tasks cost-effectively in the realm of AM. 3DEO has taken these goals to heart.
Matt Sand, president of 3DEO, says, “Our level of ambition is to be doing 20,000 pieces a day as a high-volume metal manufacturer. Others (service bureaus) with five machines are not even doing 1,000 parts a month.” Sand notes that already with their eight systems, they have transitioned from doing customer R&D work to actual production.
3DEO’s Intelligent Layering AM process is based on the repetition of three basic steps: it first spreads a thin layer of standard metal-injection-molding (MIM) metal powder; then it applies a binder to the entire layer (unlike binder jetting which precisely deposits binder just in the region of the part itself); and lastly it uses a 250-micron end-mill to shape the part at each layer. It can “cut” in three dimensions, eliminating stair-stepping, and all cut-away material is recycled and reused.

The complete process creates parts that meet the Metal Powder Industries Federation standard for quality in metal injection molding, MPIF Standard 35, providing a level of materials confidence that is a first in the field of AM. Also, the layer-by-layer milling step is so exact that Sand quotes AM industry expert Todd Grimm as saying 3DEO offers the best as-built surface finish in the industry.
Theoretical maximum part size is a 6-in. cube, but 3DEO is currently focused on smaller parts of 3x3x1 in. tall. The company’s goal is to go after small-part, high-volume production. After parts are built, they are moved to a standard MIM-sintering furnace large enough to handle the throughput of 25+ AM machines. The binder content used is much less by volume than that for other AM binder-based systems, which means the de-bind step prior to sintering is significantly faster and easier than with other technologies: one more factor in support of low-cost production.
Popular Metal Materials
Currently 3DEO is manufacturing with 17-4PH (precipitation hardened) and 316L stainless steel powders. Other materials such as tungsten, bronze, cobalt chrome and Inconel are under development, but Sand observes that 17-4 works particularly well for a large segment of the markets in which his company is involved, such as automotive, the power industries and consumer electronics.The company is working on a number of updates: the next system will offer significantly larger part size, as well as improvements in the Intelligent Layering software controls and each detail of the overall process. “One of the biggest changes since RAPID+TCT is that we are now achieving part densities of 99%,” says Sand. “This is a direct result of using ultra-fine powders.”
In Q4 2017, 3DEO will have completed ISO 9000 certification, and by the end of 2018 will have qualified its facility and processes to AS9100 and ISO 13485, according to the company. These steps will support 3DEO’s expansion into aerospace and medical manufacturing, respectively.
3DEO already offers secondary operations such as heat treating, sizing and steam treating, as well as a range of in-house quality control capabilities (e.g., optical metallographic equipment, CMM, optical comparator, micro-hardness and apparent hardness testers, surface roughness testers and humidity chamber). The company will do one-offs and small batches if requested, but the business goal is to manufacture parts in quantities of 100 to 10,000. With plans to have 50 machines up and running in the next few years, this group is poised to hit the sweet-spot for low-cost, high quality AM metal production.
Subscribe to our FREE magazine,
FREE email newsletters or both!About the Author

Pamela Waterman worked as Digital Engineering’s contributing editor for two decades. Contact her via .(JavaScript must be enabled to view this email address).
Follow DE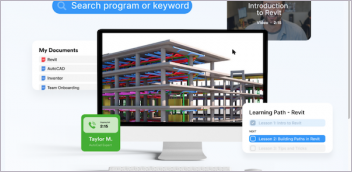

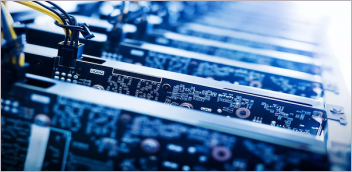
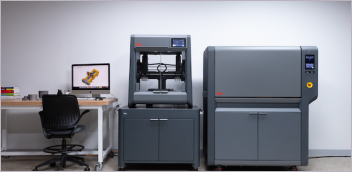