Latest News
June 23, 2017

Commentary by Sandesh Joshi
Historically, computer-aided design (CAD) and computer-aided manufacturing (CAM) have been considered to be two distinct technologies, independent of each other. However, all products that have to be manufactured have to be designed first, resulting in greater accessibility of CAM and more integration of CAD/CAM systems to streamline the process. For example, SOLIDWORKS is planning to integrate CAM into its service offerings, which could be a game changer in the industry. The new system, plus the rise of rapid prototyping, could bring CAM capabilities to virtually every desktop.
Less Human Error
Until recently, integrating CAD/CAM meant simply buying CAD and CAM products separately. Engineers used CAD systems to draw and design pictures of the parts and assembly. The CAM systems helped manufacturers program and create products from these drawings, but this two-part process was subject to a lot of human error. Now, integrated CAD/CAM systems can eliminate this and offer a faster, easier and more cost-effective way to complete projects. CAD and CAM support and complement each other to design and manufacture the product in the shortest possible time. With a fully integrated, knowledge-based technology, engineers can evaluate designs earlier in the process to avoid unexpected costs and delays in finishing products on time. It will reduce error prone, time consuming, repetitive manual steps in the current development process.
Market Poised for New Products
There is a real opportunity now to bring CAM to the market in the same way 3D CAD came on the scene 20 years ago. Getting a 3D CAD license used to be a big deal, but then it became more readily available on PCs and through SOLIDWORKS. Students often learn SOLIDWORKS in school, so having access to CAM early on will help students grow, and will offer opportunities that didn’t exist before.
The integration of CAM will welcome a slew of new product announcements since PCs will be capable of running the same solid modeling technology used in the major workstation CAD products. Not only does solid modeling technology fuel the rapid growth of new products, but it also provides a backbone for seamless data transport between compatible products. Some CAM products have plotted the shortest possible path to a marketing claim of “solid-based solution.” In several cases, this path has led to an inside CAD application version of their product where the product’s CAM capabilities are actually placed within the CAD software. However, this can lead to a more limited set of CAM capabilities than the standalone versions. The other alternative is having the CAD or CAM product based on the same modeler enabling an exchange of data as well as the big workstation systems do, providing a high level of data integration between different brands of products. Today’s technology provides flexible alternatives to the old application approach, as well as big advantages.
Is an Integrated System for You?
Now design engineers have options that give them the ability to understand how CAD features will be manufactured, and how much the process will cost. They now will be able to read tolerances and surface finishes to make decisions about how to manufacture the product. The integrated system will automatically apply best manufacturing strategies that they like to use so that manufacturing processes can be not only faster, but also more standardized. Lastly, engineers can automate quoting and compare it to traditional methods to ensure all aspects or the part are accounted for ahead of time. While there is some cost and risk involved in making the move over to integrated CAD/CAM systems, most experts agree that the investment is well worth it.
Streamlined services and access to the same or similar software that speak the same language is a huge step forward. For a company that’s using SOLIDWORKS, or another CAD system which supports API integrated CAM, an integrated solution might be a fit. If the company has the funds required to purchase an integrated CAD/CAM system, and the time needed to train its staff, it’s strongly advised to make the change. Acting today will help keep companies competitive well into the next decade.
Sandesh Joshi is the president and co-founder of Indovance Inc. Prior to founding Indovance, a CAD and drafting outsourcing service provider, Sandesh worked at SOLIDWORKS as a senior R&D member. He has a bachelor of mechanical engineering from the Indian Institute of Technology, Bombay, India, and a Master of Science from North Carolina State University in Raleigh, NC, with a specialization in CAD.
Subscribe to our FREE magazine,
FREE email newsletters or both!Latest News
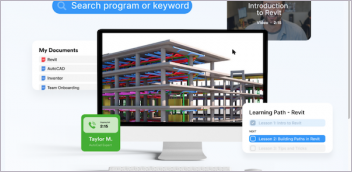

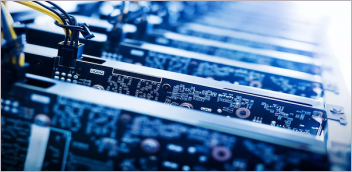
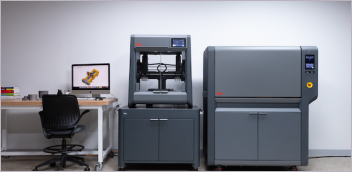