Innovation with the Multiphysics Touch
COMSOL's multiphysics simulation solutions are designed to help engineering organizations grapple with increasing complexity.
Latest News
April 1, 2013
Taking a calculated risk that hardware performance would advance significantly over time, the team set sail with its vision to bring MP to the desktop—despite the skepticism of many in academia who called the marriage improbable, and dismissed the science as far too complex for mainstream use.
![]() COMSOL Multiphysics drove the design of Cochlear Ltd.’s new Codacs direct acoustic cochlear implant system. Image courtesy of Cochlear Ltd. |
“The idea of multiphysics was borderline impossible then, but we made a bet that multiphysics would be possible in the not-too-distant future,” recalls Bjorn Sjodin, Ph.D., vice president of product management of COMSOL Group, the company founded in 1986 by that group of students. “We were laughed at, but the laughter went away as computers became more powerful.”
The core COMSOL team pushed forward, introducing its flagship product in 1998.
Fast-forward 15 years, and MP—and in particular, MP simulation capabilities on the desktop—is the direction in which many simulation vendors have set their sights. As the boundaries of engineering blur, organizations are in need of MP simulation tools to explore the interdependencies among electrical, mechanical and even software-dependent systems, and to do so in a cost-effective and efficient fashion.
The ongoing push for moving analysis further up in the design process is another factor driving demand for MP simulation. Upfront analysis is now widely recognized as a way for engineering organizations to zero in on the optimal design at a point when it is far easier to make changes, rather than the standard way of leveraging simulation at the end of the cycle as a means to prove out the viability of particular designs, experts say.
“If you think about what’s going on with upfront simulation, it’s a multiphysics and systems engineering issue,” notes Keith Meintjes, Ph.D., practice manager for CIMdata. “You’re making decisions about product architecture, and you’re doing tradeoffs among variables like weight, price, etc. The upfront use of simulation drives you immediately to need multiphysics because you’re doing cross-discipline tradeoffs.”
![]() COMSOL also played a role in investigating fatigue related to the actuator, which is one of the core components of the Codacs device. The design is set up to keep the material stress level during operation below the endurance limit. It’s a goal particularly relevant for the thin titanium diaphragm (less than 0.1mm thick), which acts both as a spring and a hermetic sealing. Image courtesy of Cochlear Ltd. |
While most industries face challenges that can only be solved by an MP, systems-engineering approach, Meintjes cites automotive as a sector where the capabilities are especially in high demand; in particular, he says, for innovations that address future fuel economy standards and for engineering the new generation of electric, battery-powered and hybrid vehicles.
Open Architecture Drives Organic Expansion
Case in Point Being able to pick and choose among physics and not have to learn a new simulation package each time has been a huge benefit for Patrik Kennes, Ph.D. Kennes is a CAE engineer at the Cochlear Technology Centre Europe (CTCE), a Mechelen, Belgium-based research arm of Cochlear Ltd., which manufactures hearing implants, among other hearing aid products. He and his team deployed COMSOL Multiphysics from the ground up on the design of Codacs, a new type of implant now in clinical trials, which provides mechanical (acoustic) simulations directly to the cochlea. Kennes says COMSOL was instrumental to optimizing the design of the actuator, an electromagnetic transducer based on the balanced armature principle. Through the use of structural mechanical analysis for various thickness values, his team was able to evaluate the tradeoffs between robustness and stiffness, and COMSOL’s AC/DC Module was employed to calculate the magnetic flux density within the parts. “Without COMSOL, we would have been able to develop the product, but we would have had to do more design iterations—and we probably wouldn’t have come as close to the optimum solution as you can when you have software to support the design,” Kennes reports. “When you have a good correlation between the measurements on the prototypes and what the ]multiphysics] model predicts, you can feel confident that the model is representative of the real world.” —B. Stackpole |
COMSOL has amassed a following in the automotive sector, but its approach has also garnered traction in other industries—from oil and gas to medical device equipment, among many others.
Rather than grow via acquisition, COMSOL has fueled its expansion organically. It’s an approach the company attributes specifically to its software architecture, which is designed to accommodate new physics modules without the need for sophisticated programming—and in lieu of requiring a wholesale software rewrite each time it wants to bring new technologies on board. The software simulates coupled physics effects by solving the underlying mathematical representations based on partial differential equations (PDEs).
With this approach, various physics solvers can be plugged into the primary engine on an as-required basis. An application programming interface (API) component makes it easy to create new physics solvers, whether that is COMSOL expanding its own portfolio of MP modules based on customer demand or individual customers creating their own solvers based on the requirements of their particular design challenge. In addition, many predefined couplings are available, including Joule heating, thermal stress, electrochemical reactions, and fluid structure interaction (FSI). For common MP problems, coupling among the physics is fully automated.
Currently, COMSOL offers 40 physics modules in the categories of electrical, mechanical, fluid, chemical and multipurpose. They cover such design trends as micro-electro-mechanical systems (MEMS) and battery and fuel cell design, with specialized offerings in areas like particle tracing and electrodeposition. The company’s plan is to release seven add-on modules a year based on a combination of customer input and the feasibility of market size, notes Bernt Nilsson, COMSOL’s senior vice president of marketing.
![]() Here is an optimized fluid distribution manifold with a single circular fluid inlet in the center that feeds a number of small peripheral fluid jet outlets. The color surface shows the normalized fluid velocity contours, with larger velocity at higher elevations. The dark edges show the optimal fluid manifold geometry that balances the flow rate to each nozzle while minimizing pressure drop. Image courtesy of the Toyota Research Institute of North America. |
One of the key benefits to COMSOL’s platform-driven MP approach is a higher fidelity model, according to Mark Yeoman, R&D director at Continuum Blue Ltd., a COMSOL Multiphysics certified consultancy.
Yeoman cites a customer example: His team was charged with creating an MP model to support research around a biomaterial equivalent for soft tissue mechanics such as arteries and skin. The model exploration would have taken about six to seven months using alternative MP simulation tools, he claims, but with COMSOL, the project took only a matter of days.
![]() This MP model looks at the implantation of a total hip replacement (femur and cup), and assesses the long-term changes in the patient’s bone formation and loss because of the functional demands and changes in mechanical loading. Coupled physics includes structural, bone formation and loss. Image courtesy of Continuum Blue. | ![]() |
“It highlights how easy it is to implement these complex materials inside of COMSOL,” Yeoman continues. “Instead of spending six months to implement an equation, we were able to do the same thing in a fraction of the time—and that’s savings that’s passed on to the client.”
UI Enhancements Fuel Accessibility
Beyond the MP engine platform, COMSOL has poured a lot of R&D energy into refining its user interface over the last few releases to make the software more accessible to both specialists and generalist engineering users.
COMSOL at Work on Hybrids At the Toyota Research Institute of North America, where multiphysics (MP) simulation is a driver for research being conducted in areas like hybrid vehicle power electronics, COMSOL’s intuitive user interface and tightly coupled approach has transformed what has traditionally been a highly complex and iterative process into something far more accessible and streamlined. That’s according to Eric Dede, principal scientist for the group. More complex design problems, including more physical interactions happening in a smaller space, means it’s not always possible to zero in on the right insights simply by building and testing physical prototypes, Dede says. “A modeling tool is critical to understanding what is going on, on a micro scale,” he explains. COMSOL Multiphysics’ tightly coupled approach also has benefits when you’re examining tradeoffs among two, three or even four physics—a scenario that isn’t uncommon for Toyota’s work in hybrid electronic components, including a recent design project for an advanced heat sink that thermally regulates the components. Instead of pouring time and resources into trial-and-error physical prototyping, Dede and his team leveraged numerical simulation and MP topology optimization techniques to design, build and test possible prototypes of a heat sink for a future generation of hybrid vehicles. COMSOL’s computational fluid dynamics (CFD) and heat transfer modules were essential to the numerical simulation piece of the project, Dede reports, while its LiveLink for MATLAB let the team leverage a high-level scripting language to optimize the cold plate’s topology. Prior to a tool like COMSOL, Dede’s team would solve one physics problem, take the results and manually enter the input to frame out the second physics problem, and so on. “It would be sequentially solved, and it required a lot of manual manipulation of data,” which could be subject to mistakes, he says. With COMSOL, the type of coupling is pre-chosen based on the physics selected when you start the analysis, he explains. “As long as you understand the physics problem and how to make it mathematically relevant, then the COMSOL software takes care of the rest of it. It makes life as a designer or analyst easier.” —B. Stackpole |
Prior to a major facelift with the introduction of Version 4.0 in 2010, COMSOL Multiphysics had a pretty rudimentary user interface. Going back to the drawing board, the goal was to design the software with MP in mind, serving up a smorgasbord of possible physics simulations via the COMSOL Desktop, which organizes the tools in a structured way and allows users to drag and drop and arrange the modules in any combination they desire.
“Multiphysics is an enormous field, and means different things for different users,” Sjodin says. “Our platform lets users use the software in the same way no matter what type of physics they’re doing. They could be doing fluid flow one day and thermal transfer the next, and the software will look and feel the same.”
Having an integrated platform for MP simulation also breaks down the silos between different engineering functions, which have traditionally relied on separate tool sets tuned to their needs of their particular function—and which don’t necessarily make it easy to exchange data.
“COMSOL Multiphysics makes it possible to share files between the different areas because they are all the same files,” Sjodin adds. “You can’t work in a vacuum anymore.”
Another major interface improvement was the introduction of the LiveLink modules also unveiled with COMSOL 4.0. These modules deliver bi-directional integration between COMSOL Multiphysics and many of the leading design tools, along with Excel and MATLAB. The LiveLink modules establish associative connectivity between the CAD and simulation applications, so if a change is made to a CAD model, the geometry of the MP model is automatically updated while the physics settings are retained. With LiveLink for MATLAB, users can run COMSOL models from within MATLAB for applications such as MATLAB programs, automatic control, statistics and geometry creation through image data.
Such integration is meant to improve workflow and help eliminate errors that can occur with having to import and export model data to and from different applications.
“This lets engineers stay in their comfortable environment to run the simulation without changing anything in the way they do design,” Sjodin says.
Beth Stackpole is a contributing editor to DE. You can reach her at [email protected].
More Info
Subscribe to our FREE magazine,
FREE email newsletters or both!Latest News
About the Author

Beth Stackpole is a contributing editor to Digital Engineering. Send e-mail about this article to [email protected].
Follow DE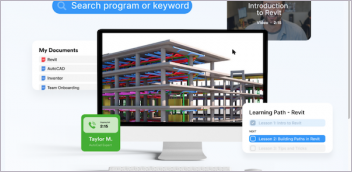

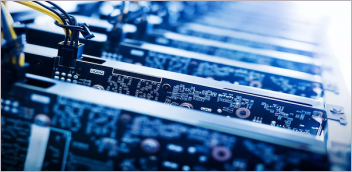
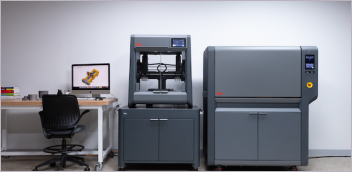