Incus Launches Hammer Pro40 Production Line System
Company to debut the 3D printing system, upscaling lithography-based metal manufacturing technology to target mass manufacturing, at Formnext 2023.

The Hammer Pro40 allows an upgrade of the production capabilities. Image courtesy of Incus.
Latest News
October 17, 2023
Incus, an Austrian 3D printer manufacturer specializing in lithography-based metal manufacturing (LMM), will introduce the new Hammer Pro40 printing solution at the upcoming Formnext 2023 show. The new system was developed to upscale LMM technology targeting mass manufacturing.
“The Hammer Pro40 was strategically developed to fulfill the growing demand for mass manufacturing with AM while still delivering the unique features of our technology,” says Incus CEO Dr. Gerald Mitteramskogler. “This innovation means a leap forward in terms of speed, precision, and cost-effectiveness, but it also opens up new opportunities to leverage the versatility of our manufacturing solution. Within a single print, you can create intricate medical gripping devices, patient-specific dental brackets, personalized jewelry pieces, prototypes for electronic devices, and customized automotive knobs for luxury interior designs—all in quantities ranging from single prototypes to mass manufacturing.”
Building on the principles of the Hammer Lab35 printing system, the Hammer Pro40 allows an upgrade of the production capabilities. The larger build volume is achieved by integrating two moving or scrolling projectors, instead of one stationary projector, without loss of accuracy.
With a platform six times larger than its smaller predecessor, the Hammer Lab35, the Hammer Pro40 bridges the gap to mass manufacturing. With a throughput of up to 700cm³/hour and a resolution with a pixel pitch of 40µm in X/Y, the Hammer Pro40 enables optimized print economics while delivering geometries and surface esthetics of the Incus technology.
The Hammer Pro40 is engineered to manufacture large batches of intricate, specialty parts in applications ranging from dental, medical, automotive, micro-robotics and jewelry. With a remarkable printing speed that is seven times faster than the Hammer Lab35 and a printing cost per cm³ that is four times lower, the new machine delivers unmatched cost efficiency without compromising on quality. With a surface roughness (Ra) of 2 µm after sintering, the Hammer Pro40 eliminates the need for additional surface treatments like polishing or sandblasting. With a high green part strength, the handling of the green parts can easily be automated.
The Hammer Pro40 is designed to operate several jobs without the need for intervention from the operator and includes a feedstock supply for at least 2-3 days. Job preparation, setup and material changeover are streamlined, taking less than 5 minutes.
Sources: Press materials received from the company and additional information gleaned from the company’s website.
Subscribe to our FREE magazine,
FREE email newsletters or both!Latest News
About the Author

DE’s editors contribute news and new product announcements to Digital Engineering.
Press releases may be sent to them via [email protected].
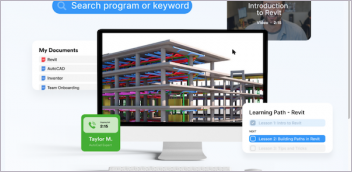

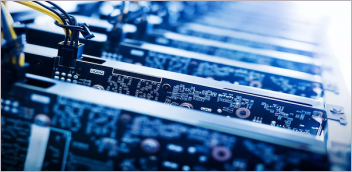
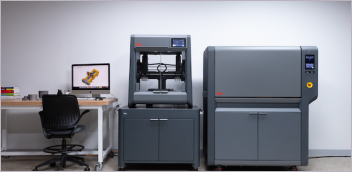