Latest News
October 18, 2013
Makino released the newest addition to its family of 5-axis vertical machining centers, the D800Z. Joining the Makino D-Series (D300 and D500), the D800Z is designed for high-performance job shops, precision parts machining, die/mold and aerospace applications. According to the company, it offers easy access to the spindle and table, a highly rigid structure for responsive cutting, improved surface finishes and optional automation devices. Workpieces of up to 1,000 mm in diameter and 1,200 kg in weight can be machined in five axes.
“Large-part 5-axis machining presents numerous challenges, due to the size, weight and range of features found on large components,” said Bill Howard, VMC product line manager at Makino. “The D800Z 5-axis machine provides new levels of sustained dynamic accuracy, achieved through technologies that are very productive, yet minimize thermal influences and maximize volumetric accuracy.”
The 5-axis capability of the D800Z can be utilized in five-face milling mode to minimize setup, maximizing access to complex, multisided parts and reducing cycle times, or to address the demanding angular, blending, matching, fine-surface finishes and 3D accuracy requirements of die-and-mold components, the company says.
The “Z” shape of the tilt-trunnion table ensures that the center of gravity of the table and work are always captured within the center of rotation of the B- and C-axes. Large-diameter bearings minimize table deflection and provide stiffness and rigidity, regardless of the angular and rotary position of the work. The direct-drive motor design provides the speed for productivity and precision for tight-tolerance work.
Also featured on the D800Z is Makino’s proprietary Super Geometric Intelligence (SGI.4) software, developed specifically for high-feedrate, tight-tolerance machining of complex 3D, contoured shapes involving continuous tiny blocks of NC data.
The unit is equipped with a number of 5-axis features, including Tool Center Point (TCP) control, which permits programming based on the tool tip, so that tool compensation features can be applied.
To save energy costs, the D800Z features an eco mode, which turns off peripheral devices when they are not needed. The energy-saving coolant system comes with an inverter-driven coolant pump that supplies precisely the required flow rate and timing for each function. The hydraulic unit, with its accumulator, ensures zero power consumption when the pump is idle.
For more information, visit Makino.
Sources: Press materials received from the company and additional information gleaned from the company’s website.
Subscribe to our FREE magazine,
FREE email newsletters or both!Latest News
About the Author

DE’s editors contribute news and new product announcements to Digital Engineering.
Press releases may be sent to them via [email protected].
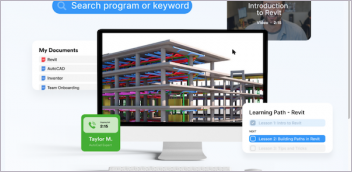

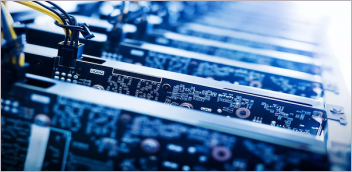
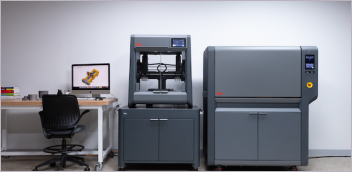