Icepak Saves Radio Manufacturer Big Time and Money, 2 in a Series
ANSYS thermal simulation is credited with helping put Datron ahead by millions by getting a new military radio to market faster.
Latest News
February 1, 2009
By Patrick Weber
« Page 1 |2
Beginning Thermal Simulation Early
Datron engineers begin the thermal modeling early in the design process. Radios can typically generate 125 watts output and dissipate approximately 220 watts inside a 15 in. x 15 in. x 5.5 in. box. Initial thermal models are developed based on very limited information, such as the size of the chassis, the RF output power, and the expected efficiency of the radio. Engineers select primitive objects, such as cubes, as building blocks and parametrically assign dimensions and material properties. Surface properties are assigned to the outside surface of the enclosure to represent the olive paint that is typically used on the final product. In the early design stages, the internal components are approximated by a single component that dissipates the total amount of heat in the radio.
As the design progresses, more detailed information on the PCBs becomes available. Mechanical engineers model the different PCBs and components within the chassis and evaluate the thermal performance. ANSYS Icepak macros are used to quickly generate models of standard packages, such as TO229. Other macros are used to generate heat fins from parameters such as the number of fins, fin width, fin spacing, etc. The model is kept to approximately 1 million cells by meshing smaller boxes around hot spots at higher densities. The early models show that junction temperatures exceed the typical maximum of 180 degrees C.
The original design could specify ferrite core filters, which are relatively light but have a very low thermal conductance. The simulation shows that the devices heat up the surrounding air to the point of overheating neighboring devices. Based on this insight, engineers replace the ferrite filters with airfoil filters that have a higher thermal conductance. This design change is key to significantly reduced junction temperatures of high power-dissipation components. Once a working design is obtained, parametric modeling was used to optimize thermal management and acoustics. Ranges are selected for several different design variables and a series of runs is set up with the software to optimize key performance parameters.
![]() | ![]() |
Figures 4a and 4b: These images show the relationship of air speed to chassis temperature. |
Using this approach, Datron engineers improve the performance of the software prototype until it meets thermal requirements within the required margin of safety. Only at this point do they order the first thermal hardware prototype. Testing shows that the thermal prototype closely matches the simulation predictions and also meets all of the thermal design specifications. As a result, no additional hardware prototypes need to be built and the radio is brought to market substantially earlier than if the previous build-and-test method had driven the design process.
In other recent thermal design projects, the simulation shows that several power transistors exceeded the junction-temperature specification. Knowing this early in the design process makes it possible to substitute these with components having lower thermal resistances that still meet the needs of the application. If this problem were not discovered until after the detailed design process, it would require a considerable amount of time and work to correct. By finding it early, it is possible to easily substitute other components without any major impact on project time or cost. With this change, engineers found they could decrease the number of cooling fins needed, in turn leaving more room on the rear panel of the enclosure. This made it possible to reduce the overall size and weight of the radio.
Thermal simulation has helped Datron achieve major improvements in military communications systems performance and thermal management. Using traditional build-and-test methods, engineers often face major design changes once prototypes are built and tested — mostly due to thermal issues. Today, thermal simulation makes it possible to validate and optimize designs much earlier, thus saving large amounts of time and money. Thermal simulation substantially reduces the time required to bring new, improved communications technology to the marketplace.
More Info:
ANSYS, Inc.
Canonsburg, PA
Datron World Communications
Vista, CA
Patrick Weber is a mechanical engineer with Datron World Communications. To comment on this article, send e-mail to [email protected].
« Page 1 |2
Subscribe to our FREE magazine,
FREE email newsletters or both!Latest News
About the Author

DE’s editors contribute news and new product announcements to Digital Engineering.
Press releases may be sent to them via [email protected].
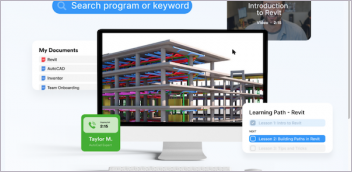

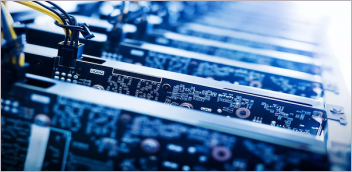
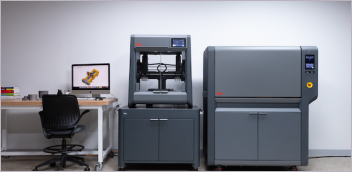