HP Targets Production-Scale Metal 3D Printing
Metal Jet S100 leverages HP’s binder jetting and printhead advantages to economically print metal parts at scale.

The HP Metal Jet S100’s modular system and integrated workflow is designed for mass production in a factory setting. Image Courtesy of HP
Latest News
September 19, 2022
HP has a strong track record of breaking new printing ground, from the Thermal Inkjet printer which made a mark on conventional printing to the HP Multi Jet Fusion, which drove innovation in plastics additive manufacturing (AM).
HP is now setting its sights on the metal 3D printing space with its latest HP Metal Jet S100 platform, which combines many of its proven assets in a modular system designed for mass production at scale. The Metal Jet S100 comprises four integrated stations—powder management, print, curing, and powder removal—which enables manufacturers to continually run production at scale for mass metals output, according to Ramon Pastor, global head and general manager of 3D Metals of HP. The platform creates an end-to-end supply chain solution, he explained, incorporating integrated workflows, automation capabilities, subscription, and service offerings to help organizations run operations at scale for mass metals production, officials said.
The last few years of chip shortages, sourcing challenges, and COVID disruptions have done a number on modern supply chains, underscoring the need for economically-sound alternatives to traditional production and sourcing strategies. Adoption of Industry 4.0 practices, including 3D printing, holds the promise to digitally transform manufacturing and supply chain practices. Yet scalability challenges and poor economics have slowed technologies like metal 3D printing from gaining significant traction beyond early adopter segments such as the aerospace and medical device industries.
“Chips shortages, COVID, and the traditional supply and demand channels have been disrupted,” Pastor said in a news conference announcing the new Metal Jet S100. “Setting up a modern supply chain is not only driven by costs, but by operational agility and resiliency with a focus on innovation. To achieve this, metal 3D printing is important.”
The HP Metal Jet S100 end-to-end solution delivers:
- HP Metal Jet software that ensures efficient operation enabled by digital insight monitoring for system maintenance.
- An industrial-grade 3D printing system designed for 24/7 manufacturing conditions and maximum system uptime.
- An array of automation capabilities, including the HP Metal Jet Powder Removal Station, which automates removal and recovery of loose powder as well as build unit cleaning, and the HP Metal Jet Powder Management Station, which automatically mixes, sieves, and loads powder to the build unit. The HP Metal Jet API enables the digital orchestration of the production workflow for automated scheduling, routing, and job monitoring.
HP has also focused on improving customer economics with the new HP Metal Jet S100 offering. The modular and integrated stations ensures that the process steps needed to create parts are streamlined while also reducing manual labor and print complexity, Pastor said. HP’s expansive intellectual property and past printing technologies also offer a leg up over traditional laser-based metal 3D printers. The company touts printhead advantages thanks to innovations related to the HP Thermal Inkjet IP in addition to stronger binder strength borrowing from its latex IP.
The company has developed the HP Metal Jet end-to-end solution to be fully characterized for 316L and 17-4PH stainless steel materials.
As part of its announcement, HP showcased Schneider Electric as an early customer. Working with partners HP and GKN, a multinational automotive and aerospace components company, Schneider Electric produced an air filter that required highly complex lattice geometry that was expensive and labor intensive to produce with traditional metal mesh manufacturing as well as with powder bed fusion technology.
Using HP Metal Jet S100, the partners were able to develop a cost-effective metal air filter for 690V circuit breakers designed for oil and gas, railway, and marine projects. Schneider Electric officials said they were able to achieve a more efficient and sustainable product while achieving a 20% reduction in the switchboard’s footprint.
To learn more about the HP Metal Jet S100 technology, check out this video.
More Hewlett Packard Coverage
Subscribe to our FREE magazine,
FREE email newsletters or both!Latest News
About the Author

Beth Stackpole is a contributing editor to Digital Engineering. Send e-mail about this article to [email protected].
Follow DE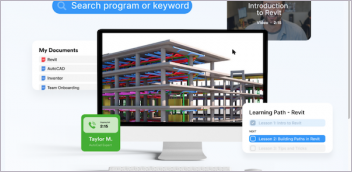

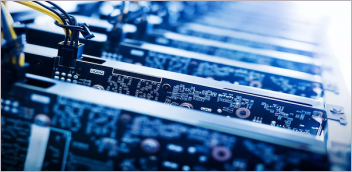
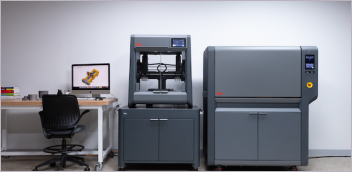