How to Optimize Manufacturing Capacity
Use of virtual manufacturing networks has potential to lead to greater agility and resilience in the long run.

Fig. 1: Virtual manufacturing networks must be built on a solid foundation of digital collaboration tools. Image courtesy of Siemens Digital Industries Software.
Additive Manufacturing News
Additive Manufacturing Resources


Dassault Systemes

Hexagon

Latest News
April 6, 2023
Growing demands for shorter order-completion cycles, greater customization and more small-batch options are compromising small and medium-sized manufacturers’ abilities to accept production orders. To stay competitive and maintain their profitability, companies have started adopting a strategy called virtual manufacturing networks, which has typically been used by larger, more mature industries such as automotive, aerospace, semiconductor and electronics.
This shift is supported by economic necessity and the availability of powerful digital platforms, tools and practices that provide granular visibility throughout machines’ and processes’ lifecycles, across the supply chain. These technologies enable small to mid-sized businesses (SMBs) to implement these networks and clear the way for them to adapt to the new manufacturing landscape by cultivating greater agility and resilience.
Finding Strength in Numbers
The goal of virtual manufacturing networks is to bring together manufacturing enterprises in collaborative alliances that allow each company to leverage the other enterprises’ free production capacity (Fig. 1).
To create such a network, companies must identify each network constituent’s core competencies and capacity. Armed with this knowledge, a company can arrange for alliance members to take over the parts of the manufacturing process that are unfeasible for the larger company. This flexibility promises to help manufacturers to better manage workloads by radically transforming traditional infrastructure to make it more scalable.
The value of this approach is that distributed production processes are performed simultaneously, in parallel with each other. At the prescribed time, the manufacturer that took the original order brings all pieces together. This approach takes less time to build the entire product than a linear process carried out in a single facility. Further, it reduces network constituents’ costs.
“You’re trying to improve your capacity,” says Rahul Garg, vice president of industry machinery and the SMB program at Siemens Digital Industries Software. “You’re trying to offload some of your capital expenses onto those factories. If you have to build everything, then you have to stand up a factory. You have to bring in all of the machines. Whereas, if you outsource the work to a supplier, then they are responsible for doing all that, and all you have to do is worry about getting that one part from the supplier. You just pay them per part.”
Having proven its value in the larger, more mature industrial sectors, this strategy is beginning to gain traction among small and medium-sized manufacturers.
“We are seeing more complex and virtualized manufacturing networks as manufacturers look to increasingly optimize production while balancing their response to demand fluctuations, supply interruptions and rapid onshoring of manufacturing capacity post-COVID,” says Keith Chambers, vice president management software at AVEVA. “In short, agility and resilience are the new imperatives, which are the key to unlocking profitability.”
“In some ways, this is an outgrowth of earlier outsource/contract manufacturing approaches, but now with sufficient granularity of data, it allows not just simple B2B transactions between the elements of the network but also meaningful optimization strategies across different plants, which are owned by different enterprises,” Chambers says.
Along with the strategy’s advantages, however, the manufacturer encounters a new set of challenges. Implementing these collaborative practices adds new layers of complexity for manufacturers doing integrated business planning, along with those running plants that must serve multiple producers at the same time. This is where the digital tools and practices come into play.
Start With a Plan
Contending with this complexity and making virtual manufacturing networks work requires extensive visibility. This means getting the right data at the right time.
This process can begin with the development of a bill of process (BOP), which basically describes how the product will be built and what tools and resources will be required.
To achieve the best results, the BOP requires close collaboration between engineering and manufacturing, as well as among the network constituents. This can be achieved through manufacturing process planning software within the companies’ product lifecycle management (PLM) systems. Manufacturers use the PLM’s workflow, change management and configuration capabilities to create the BOP.
Empowered with the BOP data, the company assigning individual manufacturing tasks can begin to identify the most suitable manufacturers in the network to fabricate the outsourced parts. Plant-specific BOPs also can be created to accommodate special requirements.
“Siemens can make BOPs specific to different assemblies, different product configurations and different regional needs,” says Siemens’ Garg. “For example, if a tractor must be built in the U.S., the manufacturer may look for the highest possible speed and comfort of the operator. In China, the manufacturer may look for the lowest possible cost. The company may also add variants to the tractor so that it can be built in any of these locations, using a common enterprise bill of process. Then the suppliers, who are feeding into that enterprise BOP, will be able to easily see what the different variants are, and it becomes a lot more efficient for the company to track the manufacturing process and the throughput of your different plans as well.”
For industries in which product complexity is increasing and lot or batch size is decreasing, integrated BOPs have become imperative for cost-competitive manufacturing operations.
Upon the BOP’s completion, the production plan should be communicated with the collaborating companies’ primary manufacturing systems—such as their manufacturing operations management system and the manufacturing execution systems (MES)—to implement the final plan.
Test All of the Variables
The number of variables and the degree of complexity involved in producing a product using a virtual manufacturing network preclude the use of manufacturing tools that rely on manual data collection and analysis. The answer to this dilemma lies in the implementation of digital threads and digital twins.
The digital thread brings together all of the engineering, manufacturing and operational data related to the assets making up the larger model of the plant and manufacturing network, from demand to delivery (Fig. 2).
“The digital thread, shown in Figure 3, provides the data that makes it possible for manufacturers to plan, execute and optimize production, not just across one plant, but across the entire virtualized manufacturing network,” says Chambers.
Chambers goes on to say that this digital thread requires a digital twin that spans the manufacturing network and supply chain. Technologies such as supply chain planning, MES, industrial Internet of Things (IIoT), cloud and artificial intelligence (AI) are critical to planning, execution and optimization.
“The critical enabler is the underlying data platform, which must tie together disparate systems, across multiple vendors and generations of systems, to provide a standard, contextualized view of what is happening across the manufacturing network,” Chambers says.
Combined, the two technologies enable manufacturers to run what-if scenarios, factoring in all variables, to compare different plans for manufacturing parts in the most efficient way, supporting near-real-time, data-driven decision-making.
“The simulation process is essential in the virtualization of manufacturing because it helps manufacturers to ensure that the different parts, regions and collaborating manufacturers that they are trying to get the parts built through will have the capacity and availability that is required,” says Garg. “You will need to model, simulate and verify how this will all get built, based upon certain schedules that you may want to meet.”
By engaging digital twins of the factories, a manufacturer can simulate how that product will be built in each facility, according to Garg. Using each factory’s digital twin, it’s possible to analyze the resources that will be used in the production process, and also to analyze the throughput of each factory.
“What’s more, manufacturers can use predictive simulations to adjust production and capacity to best fit customer demands, changing supplies, or machine or logistics outages,” says Andrew Deeble, Emulate3D engineering lead at Rockwell Automation. “They can also provide an understanding of how and when to redirect parts of the manufacturing process to different facilities or vendors, based on capabilities and capacity constraints.”
Digital twin modeling and simulation capabilities can help manufacturers to identify issues that may hinder or interrupt the network’s production processes and facilitate supply chain logistics restructuring.
“Manufacturers can optimize process performance with alternate product routings to areas in the network with excess capacity,” says Prashanth Mysore, strategic business development and industry marketing director, DELMIA, at Dassault Systèmes. “This level of flexibility can provide vital resilience during times of supply or process disruption. Furthermore, organizations with digital transformation programs can use their virtual twins to identify improvements that can become their standard operations, not just for contingency planning, but also optimizing production flow, throughput, accessibility and safety of workers.”
Digital twins’ ability to promote collaboration dovetails perfectly with virtual manufacturing networks’ requirement for seamless and secure data sharing among the different companies working within the network.
Problems With Data Persist
Barriers to the use of virtual manufacturing networks for optimization of production capacity revolve around data. Specifically, the problem has been the availability of large-scale, specialized industrial data platforms and the ability to form shared-data communities between businesses. Though industrial cloud platforms designed for the unique requirements of real-time production processes and data sharing are now available, problems with the availability of standardized, usable data persist.
For example, manufacturers often need to combine information technology (IT) data with operational technology (OT) data. This means combining IT data from enterprise resource planning, product lifecycle management, enterprise asset management, computerized maintenance management system, or customer relationship management systems with OT data from IoT devices used on production and material handling machines and production management systems. This is where things get dicey.
“There are certainly mature enough technologies available on the market to fine-tune manufacturing operations to enable greater production capacity, but often these technologies are implemented as individual point solutions, operating in a silo and providing only a minor return on investment,” says Jason Walker, vice president, general manufacturing practice lead, Hexagon Manufacturing Intelligence.
As a result, it can be a struggle to access, combine and analyze the necessary data to understand the overall virtual manufacturing network. The result is that some of the most critical business questions go unanswered, resulting in lost opportunities to improve efficiency and enhance quality.
Further compounding the limited access to necessary data is the fact that the array of software and technology that manufacturers must contend with often use different communication standards that do not translate well between systems.
“To be useful across the manufacturing network the data must be standardized, validated and contextualized,” says Chambers.
Some attempts have been made to address this issue through standards, but gaps in these protocols persist in obstructing resolution of the data issues.
“The ISA-95 was established as a standard for integration of information flows between the shop floor and enterprise applications,” says Mysore. “However, as part of that integration, it is necessary to have consistency within your data model, such as where and how it is stored, as well as where the master data resides. Each of these data modeling components must be addressed as part of establishing an integrated manufacturing enterprise. Incompatibility between legacy machines and newer systems makes this even more difficult.”
That said, software vendors have begun to take additional steps to provide for the necessary data. These include:
- Creating agnostic connections to the underlying data sources.
- Using automated capture and governance of the data to ensure data integrity.
- Using innate contextualization of the data at its point of capture.
The Issue of Cybersecurity
Even as software developers work on developing tailored data curation systems for the manufacturing sector, another data-related problem waits in the wings.
“The challenge, of course, is cybersecurity because virtualization requires the sharing of data between businesses across the internet,” says Chambers. “Cybersecurity is a foundational part of any industrial cloud platform and data community.”
What’s Next?
The use of virtualization to optimize manufacturing capacity will likely increase as companies embark on their digital transformation journeys. The cost benefit far outweighs the initial investment because virtualization will help to raise efficiency, lower IT expenses as well as streamline and optimize processes across facilities.
“Manufacturing companies are facing a growing list of common issues extending throughout their entire value network,” says Mysore. “These can be addressed through virtualization, providing robust methods for achieving effective resource allocation, specifically focusing on problems like resource leveling, sizing of machines and production layouts, cost optimization in scheduling, and implementing standardized, lean and replicable processes.”
Empowered with technologies like digital thread and digital twin, virtual manufacturing networks will be a powerful enabler, performing what-if analysis to mitigate manufacturing capacity challenges and to optimize production capacity.
These advances will open the door for a number of new applications. These may include:
- Assessing new products and evaluating potential changes in production.
- Re-assessing manufacturing strategies and capacity to mitigate shortcomings.
- Reducing waste in resources and productivity via lean manufacturing.
More Dassault Systemes Coverage
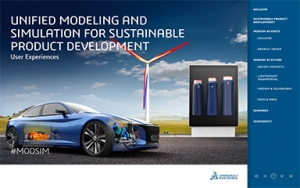
More Hexagon Coverage
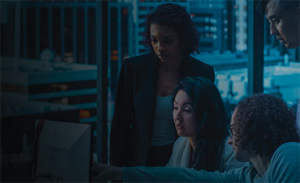
Subscribe to our FREE magazine,
FREE email newsletters or both!Latest News
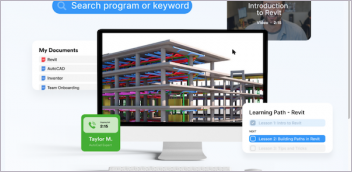

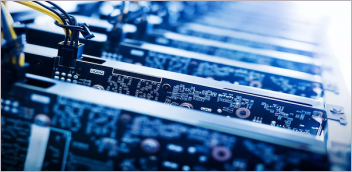
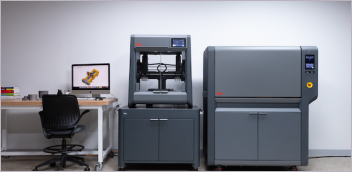