Hexagon ICME Solution Integrates Advanced Materials Into Design
ICME is a technique that ensures optimal combination of materials and manufacturing processes to innovate and maximize performance.
Latest News
April 22, 2020
e-Xstream engineering, part of Hexagon’s Manufacturing Intelligence division, has unveiled a new 10X Integrated Computational Material Engineering (ICME) Solution that applies academic research with software and inspection solutions to accelerate innovation by enabling manufacturers to design, engineer and test components virtually through simulation.
ICME is a technique that ensures optimal combination of materials and manufacturing processes to innovate and maximize performance, resulting in reduced costs and lead time, according to Hexagon.
10X ICME from Hexagon offers an integrated solution portfolio to leverage the full potential of ICME. By integrating design, engineering and testing, manufacturers can make informed choices early in product development to improve quality or reduce waste and also harness data to devise more efficient, connected design and engineering workflows.
ICME enables advanced materials such as carbon fiber composites to be selected and applied to their full potential by improving the accuracy of, and trust in, material simulations with better data and modeling. Using 10X ICME, it is now possible to predict how combinations of advanced materials such as composites and manufacturing methods from injection molding to 3D printing will affect everything from the speed to the sustainability of future aircraft and cars.
It reduces the amount of materials testing required and correlates measurement with simulation so manufacturers can more easily validate simulations. In addition, because materials data is made readily available, engineers can apply accurate values to make optimal designs rather than relying on approximations.
The digital integration of end-to-end supply chains will also cut material waste by significantly reducing dependence on extensive real-world prototyping and over-design. A single material-centric ‘digital twin’ of the entire manufacturing line from material development to final part performance will enable organizations to predict the performance of end products at concept stage. It also presents opportunities for data-driven customization of advanced materials for specific purposes such as recyclability or energy efficiency.
10X ICME lower barriers to innovation by enabling new technologies such as lightweight blended wing airliners or ultra-quiet electric vehicles to be developed much faster than today. The solution is already being used by a major aerospace and automotive original equipment manufacturers (OEMs) to accelerate the rate at which new designs can be brought from concept to reality. Initial customer projects using this new approach are being completed in half the time and at a third of the cost.
Sources: Press materials received from the company and additional information gleaned from the company’s website.
More Hexagon Manufacturing Intelligence Coverage
Subscribe to our FREE magazine,
FREE email newsletters or both!Latest News
About the Author

DE’s editors contribute news and new product announcements to Digital Engineering.
Press releases may be sent to them via [email protected].
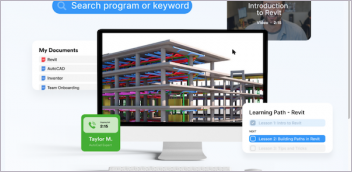

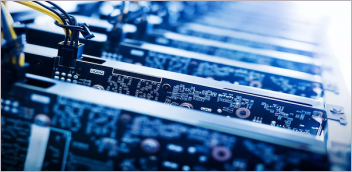
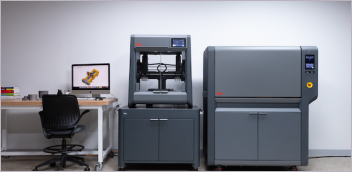