Latest News
July 1, 2010
By Kenneth Wong
![]() Jack and Jill, digital human models that are part of Siemens PLM Software’s Tecnomatix suite, enables automakers like GM to digitally simulate and study the impact of assembly work environments on humans. |
Bob Tilove, a technical fellow at General Motors’ Manufacturing Systems Research Lab, commands a small army of digital humans. Day or night, whenever he wants to find out something about an assembly process or a plant layout, he calls on them to do his bidding. They’re part of his workflow and assembly environment simulation arsenal at GM.
As reliable and sophisticated as they are, Tilove feels it’s time to up the ante, to improve current technologies to enable more advanced simulation exercises. He gave a presentation on the subject at the Congress on the Future of Engineering Software (COFES) 2010 in Scottsdale, AZ. Here, he shares his thoughts about spawning a new generation of digital humans and simulation tools for manufacturers.
Your vision is a little different than Most CAD vendors who promote the idea of “digital prototyping,” using a digital replica in conducting studies in a digital environment. Can you explain?
Tilove: Most people, when they speak of “digital prototyping,” are thinking about the end product or artifact, and how it will work, and whether or not all of the pieces will fit together, or if it will break when you drop it—things like that….
In my area, virtual manufacturing, I’m thinking not so much of the final product, but of the manufacturing process in the factory or the plant for making it. So it’s similar to “digital prototyping,” if you think of the thing that you want to prototype as the manufacturing facility, which means all the parts and sub-assemblies, the work in process, how they flow through the system, plus all the tools and equipment and conveyors and controls involved ... a much bigger scale.
The specific thing you asked me about that I call “virtual simulated work environments” focuses on manufacturing operations involving human assembly workers. In automotive, we call that general or final assembly, where people are installing and connecting hoses, cables, wiring harnesses, instrument panels, seats, carpets, and so forth. And of course, with the focus on human operators, we are concerned about their ergonomics and comfort.
At COFES, you indicated CAD packages are not well-equipped for certain materials and processes you wish to simulate. Can you outline your challenges?
Tilove: As a researcher, my job is to envision what ]simulation] might look like in the future, and try to drag that vision into reality by doing advance R&D projects.… Today’s CAD systems handle rigid, solid objects and mechanisms with rigid links very well, but they do not handle those flexible parts I mentioned before like hoses, cables, wire harnesses, foam, or carpets well.
Today’s systems handle interference detection quite well in packing and motion planning of rigid objects, but they are not able to simulate what happens when a flexible part comes into contact with another flexible or rigid part. For example, if you imagine a hose fitting onto a connector, the connector is bigger than the hose by design. In today’s CAD systems, if you were to run an interference check, it would say, “There’s interference.” We would then say, “OK, that interference is by design, so it’s fine.” But when the hose is actually installed, it doesn’t interfere with the connector. It deforms, and we need to be able to model and simulate that deformation, including the forces that are involved…. What we need to move to is what some people call “physical modeling,” where we’re modeling not only the geometry but also the materials and the physics involved.
What are the shortcomings you’ve noticed in digital human models that come with current PLM systems?
Tilove: We do have digital human models or computer manikins in commercial tools, and we try to use them to assess reach, access, and ergonomics. But the problem is, the digital human models today are not too smart. They’re like those wood human models you may have seen that artists use. You can put its hands somewhere, you may reposition its torso … but you can’t just tell a digital human to reach into a cluttered environment and install a part. That does not just happen automatically. Either a highly skilled ergonomist has to manually adjust the joints in the digital human to get a realistic posture, or, in some cases, companies use motion capture technology ... capture the posture of the human, and use that to program ]the movements of] digital humans. In the future, we need the digital humans to be much more intelligent, to be able to figure out for themselves where to stand, how to grasp, how to reach…. That’s a significant R&D challenge.
What are the risks in applying insights drawn from observing digital workers to real assembly line workers?
Tilove: Let me try to clarify. The digital human is a model. It’s an approximation—we recognize that…. What we’re trying to do is to identify and fix problems before they would otherwise be noticed by the real assembly line worker…. At the end of the day, our objective is to make the best possible work environment for the real assembly line worker ... we would probably find and continue to fix problems later in the process in the real world … but the more we can simulate virtually, the better off we are.
This type of digital human also appears in gaming. Have you explored the idea
of collaborating with game companies?
Tilove: What you’re asking about are interactive computer games with great graphics and intelligent actors in them. One of the things I would say is that the creators of those games are looking for compelling and exciting experiences, not necessarily things that obey the laws of physics or the biomechanical capabilities of real humans. In a way, that’s part of the fun of those games. So far, we have been focusing mostly on getting the physics and human biomechanics right, but when we finally get to virtual simulated work environments, I think they are more likely to be built, from a computer science perspective, like multi-agent, distributed computer games than like today’s manufacturing work cell simulations. At least I think that’s a good possibility.
More Info:
COFES
Subscribe to our FREE magazine,
FREE email newsletters or both!Latest News
About the Author

Kenneth Wong is Digital Engineering’s resident blogger and senior editor. Email him at [email protected] or share your thoughts on this article at digitaleng.news/facebook.
Follow DE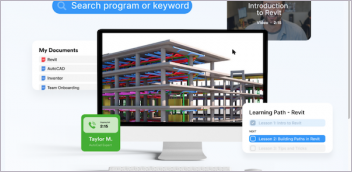

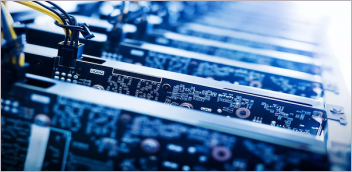
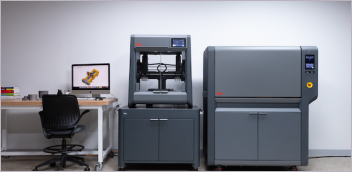