
5-axis enhancements include a new rotary machining strategy to cut parts with cylindrical or conical floors. Image courtesy of Cambrio.
Latest News
October 26, 2021
CAMBRIO, a CAD/CAM innovator in the production machining industry, announces the new release GibbsCAM 2022.
“The latest developments see further emphasis on end-user productivity in all areas of the product,” says GibbsCAM Vice President Nick Spurrett. “GibbsCAM continues to lead the industry in the programming of advanced machining centers and we wanted to focus on absolute product quality and core functionality, while retaining GibbsCAM’s ease of use. Our aim is to always deliver on our promise of 'Powerfully Simple, Simply Powerful.'”
The latest release includes a number of CAD enhancements for solid and surface modeling, which include the ability to extrude multiple bodies with taper, and to create surfaces as a stitched body directly from closed 2D geometry. In addition, users can automatically create trimmed planar surfaces in any orientation at geometry depth instead of the CS plane.
Further developments include new alignment capabilities, which allow straight edges of solid bodies to be easily aligned with the working coordinate system in preparation for machining, and a new sectional view slicing plane, which can be dynamically moved in any direction to easily view and select features within the interior of a solid body.
Among the multiple CAM additions within GibbsCAM 2022, a number of usability enhancements have been included such as automated multi-shape predrilling, and extended control for start / end points of profiling toolpaths. It is now possible to omit radius moves on outside corners of turning operations, which makes it easier for lathe operators to adjust critical diameters and reduce output size of G-code files.
VoluMill has been improved and delivers time savings on calculating rest milling operations on complex geometry. In addition, you can now also control the preferred starting zone for symmetrical cuts to aid chip evacuation and reduce rapid movements for deeper pockets.
Five-axis enhancements include a new rotary machining strategy to cut parts with cylindrical or conical floors such as feed screws or augers. Advanced control of the tool includes off-centerline roughing, and front or back engagement of the tool point with automatic corner offset. New five-axis deburring enhancements include the ability to generate multiple cuts to approximate a chamfer or fillet on an edge beyond traditional edge breaks.
It is also possible to use cylindrical or conical tools for chamfering by selecting a specific contact point to keep a straight tool section. Toolpath quality is also improved for five-axis Geodesic operations in areas where multiple surface normal instances control the toolpath. Other five-axis updates include automatic tilting for collision avoidance for arc leads, the ability to select automatic tilt limits or set a fixed tilt angle relative to a selected surface normal.
In a collision rich environment such as mill/turn or tombstone machining, simulation is a key component. GibbsCAM 2022 introduces a number of enhancements, which include the ability to hide multipart cutting in all simulation modes to reduce the verification time based on the number of components being machined. The use of 3D material only stock generation on multi-spindle machines can increase the simulation time of MTM configurations by up to 25 times. Additionally, a new feature allows the user to start simulation part way through a multi-flow MTM or Swiss program.
Machine support has been significantly improved to include the ability to support multiple kinematic configurations of a CNC machine within a single post package. This provides extended flexibility to support machines that can be configured in multiple ways, such as a three-axis machine with or without a removable rotary table. This technology can also be extended to more complex Swiss configurations to support different parts or tooling arrangements.
“GibbsCAM 2022 provides additional milling and turning capabilities, and extends machine simulation functionality for our customers,” Spurrett says. “This improvement in communication between software and CNC machining centers will help drive productivity while reducing machining time.”
Sources: Press materials received from the company and additional information gleaned from the company’s website.
Subscribe to our FREE magazine,
FREE email newsletters or both!Latest News
About the Author

DE’s editors contribute news and new product announcements to Digital Engineering.
Press releases may be sent to them via [email protected].
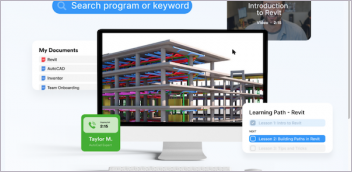

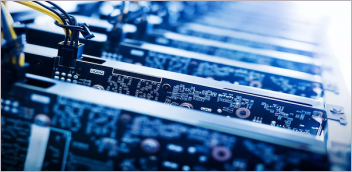
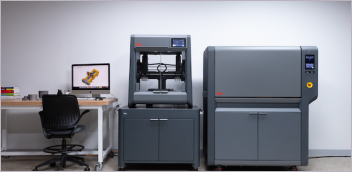