Latest News
January 1, 2006
By Louise Elliott
Manufacturers who are preparing to comply with new environmental regulations face many issues.
This first of two articles discusses the challenges being faced by companies preparing to comply with new European and Asian product substance regulations. Part 2 will explore existing solutions via PLM.—DE
The European Union (EU) is poised to enforce a number of new environmental regulations restricting the use of a variety of hazardous substances and mandating recycling of polluting components in vehicles and electrical and electronic equipment. Japan, Korea, China, and other Asian countries are planning similar directives. All of this means that companies planning to sell or manufacture products in those parts of the world—a substantial portion of the worldwide market—will have to comply.
› › A few mouse clicks from within Dassault Systemes’ ENOVIA V5 design environment brings up sourcing data search parameters, a critical step toward providing RoHS-compliant design capabilities within a PLM environment. Click on image to enlarge.
Manufacturers, regardless of their own locations, face problems in complying with the new regulations because, while they can control the materials they use for their own manufactured parts, they also deal with many outside suppliers. As a result, certain questions need to be answered: Will those suppliers be able to comply by the time enforcement begins? What about old parts that remain in inventory? How can manufacturer and supplier compliance be tracked?
The relevant regulations are new and subject to change. Within the EU, products not only must comply with the overall Union regulations, but also with individual national laws. Here’s a short summary of the overall directives, in order of their effective dates:
2000-2005: The EU directive on end-of-life vehicles (ELV) seeks to reduce or prevent waste produced by vehicles reaching the end of their lifecycles, and to increase recovery and recycling. Targets for reuse, recycling, and recovery will increase between January 2006 and 2015. Similar provisions exist in the United States.
‹‹ MatrixOne simplifies the data exchange and reporting process for supplier and customers. Comparative views, configurable tabular views, and analytic reports can easily be created for supplier management, substance use, substance thresholds, and recycled content. Click on image to enlarge.
February 2003-2006: Waste Electrical and Electronic Equipment (WEEE) aims to minimize the effects of scrapping electrical and electronic equipment containing a range of hazardous substances. It makes producers responsible for product collection, treatment, recycling, and recovery of waste like lead and other toxic materials. The target date for achievement of these goals is December 31, 2006.
July 2006: The Recycling of Hazardous Substances (RoHS) directive comes into effect. This bans EU sales of new electrical and electronic equipment containing more than agreed levels of lead, cadmium, mercury, hexavalent chromium, polybrominated biphenyl (PBB), and polybrominated diphenyl ether (PBDE) flame retardants. Manufacturers will have to ensure that their products—and the components in them—comply, or be barred from sale unless redesigned to comply.
While everyone contacted for this article believes that the environmental regulations are in the public interest, they noted a number of challenges that companies face in efforts to comply with them.
The Agile Product Governance & Compliance interface displays the substance composition of a bill of material as both a list (left) and in the form of a pie chart (right). Click on images to enlarge.
Many companies planned for the regulations by anticipating that they could be dealt with by quality assurance. But QA takes place at the end of the manufacturing cycle, and non-compliant products will lose significant market share and often have to be scrapped after significant investments in money and time. It makes more sense to start the compliance process at the design stage—and that means finding ways to give designers the information necessary to create compliant designs.
Materials ManagementCompanies with worldwide markets, whether OEM or component manufacturers, have no choice but to comply with the new regulations. That means, says Mike Adams-Sampson, VP of product strategy for MatrixOne, that manufacturers now have to manage materials for performance as well as content.
“This requires accounting for the decomposition of parts, including those made by suppliers, and creates very complex reporting needs,” he says. “Almost everything that touches the end product needs to be covered, because parts get re-used in different markets. Companies may have to decide whether to continue or terminate product lines because of substance content.”
›› The Teamcenter Environmental Compliance environment from UGS has a search function that displays different degrees of pass and failure of specific parts with regard to the new RoHS regulations.
Adams-Sampson believes that many companies, especially in the electronics segment will become—if they haven’t already—even more conservative about the substances used in their products than the regulations allow to be certain they can meet increasingly stringent requirements. “The conceptual design phase is the best time to consider substances, because that’s when it’s easiest to make any necessary changes.”
A great many companies started their compliance processes by “tinkering with existing systems to make them handle environmental data,” says Chad Hawkinson, director of high tech market strategies for PTC and the company’s expert in environmental regulations. “That approach may have worked for the preliminary stages of compliance, but such solutions weren’t scalable—and companies need to be able to reuse their data to comply with a variety of different regulations. Environmental compliance is becoming a decision-making factor in choosing PLM.”
On the left, PTC’s Arbortext Dynamic Publishing solution can pull data from Windchill to automatically create compliance documents in a variety of formats. On the right, Windchill Environmental Regulatory Compliance Solution automatically analyzes product structures to determine if they are compliant with a selected regulation, such as RoHS. Click on images to enlarge.
He points out that even manufacturers who started compliance efforts early face some problems. In addition to making sure that parts coming from outside suppliers meet the regulations, companies must plan for being unable to obtain large quantities of compliant parts in the short term. “We’ll see some shortages of parts, which will call for creative strategies in planning assembly and manufacturing. We’ll also see inventory write-offs for non-compliant parts—so that the middle of 2006 may get risky.”
Tom Maurer, director of industry marketing for high tech and electronics for UGS, agrees that many companies have put in stopgap reporting solutions for compliance certification. “But what they really need is a lifecycle strategy that includes product decomposition at the end of life. Some companies think of regulatory compliance as an ERP ]enterprise resource planning] issue, but if so, they’ve missed the opportunity to build compliance into the design cycle. Those who see compliance as an ERP matter try to fix problems with change orders, but that’s too late.”
›› Arena Solutions offers mid-size and smaller companies the ability to manage regulatory compliance without enterprise-level investments. The program describes the current regulations and offers instructions on assuring certificates of compliance exist for certain projects and parts.
He says that high-tech component manufacturers who already find early obsolescence an issue need to consider “end of life up-front and build compliance into the product structure.”
Lack of ready data about suppliers and their ability to respond to the new environmental regulations is a problem in itself, says Fabien Fedida, strategies director for Dassault Systemes. “Different manufacturers in different geographical locations may find it difficult to meet materials requirements in other locations. Because OEMs need to be able to manage the engineering lifecycle, including obsolescence dates for old parts, the PLM and sourcing vaults need to be brought together. This is probably most essential for complying with WEEE regulations, because products need to be returned to the OEM, who then has to send the parts back to their original manufacturers.”
Ideally, he says, product designers should be able to enter the attributes of non-compliant materials and filter them out of manufacturing at the design stage.
“The impact of environmental regulations is blind to company size,” says Eric Larkin, CTO and co-founder of Arena Solutions. Mid-size and smaller companies, which often make components for OEMs in addition to their own products, can’t usually afford enterprise-level PLM, but still need to manage regulatory compliance. Larkin thinks that such companies need to design products to comply from the ground up.
Describing the current regulations as merely a harbinger of a basic shift in the regulatory environment for manufacturers, Larkin says, “Mid-size companies need a broad understanding of the need for recycling electronic and other materials, to accept that regulating the contents of products is in the public interest, and use tools to make it happen.”
Manufacturing companies currently using the EU regulations as a standard for manufacturing also have to consider upcoming Asian regulations, says Ray Hein, vice president of product strategy for Agile. He points to a Chinese requirement as an example: The place of origin must be stated on manufacturing equipment, along with recycling data.
To meet the various requirements, companies need to be able to evaluate all the substances used in their products, and to break out hazardous substances in parts per million (a RoHS requirement). “They need to be able to evaluate such data against the various regulations and report on compliance,” Hein says. “Nowadays, most manufacturers aim to meet a single standard that’s compliant with all regulations. It’s been a challenge for them to understand that it’s easier and less costly to comply than to pay fines.”
Contributing Editor Louise Elliott is a freelance writer based in California. Offer Louise your feedback on this article by clicking here. Please reference “Compliance, January 2006” in your message.
National Instruments (NI) makes control and monitoring instruments that fall more under the WEEE regulations than RoHS—giving the company a little extra time to use up old components in inventory before the WEEE recycling regulations come into effect late in 2006. Stefanie Breyer, RoHS program manager for NI, heads a group that has been working actively for about 18 months.
“Compliance means recreating some manufacturing processes,” she says. “We use some PLM tools and have also developed some of our own for tracking compliance—particularly of parts from suppliers. We can now see which are compliant at the component raw material level.”
NI has already marked its products for WEEE recycling requirements, and has set up re-take and made recycling arrangements. Breyer says that recycling will be handled by outside contractors all over the world.
“WEEE rules vary by country, while RoHS is pretty much the same everywhere. Enforcement may vary, and if current customers resell older, non-compliant equipment, it could create complex problems,” Breyer says. “Where our customers require RoHS compliance by July, we work with them on an individual basis ]to meet that need].”—LE
Company Information
Agile Software Corp.
San Jose, CA
Arena Solutions, Inc.
Menlo Park, CA
Dassault Systemes
Paris, France
MatrixOne, Inc.
Westford, MA
National Instruments
Austin, TX
Subscribe to our FREE magazine,
FREE email newsletters or both!Latest News
About the Author

DE’s editors contribute news and new product announcements to Digital Engineering.
Press releases may be sent to them via [email protected].
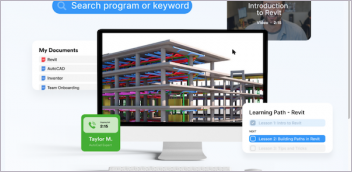

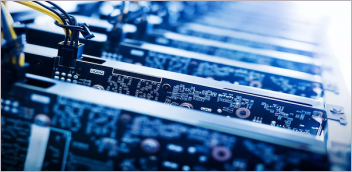
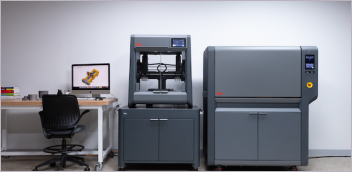