Latest News
December 1, 2008
By Pamela J. Waterman
Page 1 | 2 »
![]() Auto fuel spray and combustion sim of a port-injected internal combustion engine using es-ice.Image courtesy CD-adapco |
Last month DE dug into the world of simulation software for analyzing mechanical design challenges in very specific fields. Each approach streamlined the time required to work on tasks with well-defined and repetitive inputs, as compared to finding the same answers with a general-purpose package. This month we describe comparable targeted software solutions that predict behavior in the realms of thermal analysis, fluid flow, fluid-particle interactions, electronics, and microelectromechanical systems.
Understanding Thermal Issues
Within the Siemens PLM Velocity Series is a set of targeted analysis packages that can work both independently and with each other. One example is the Femap Advanced Thermal Solver, an add-on to the basic Femap Thermal Solver. The Advanced version digs deep into thermal analysis, solving complex heat-transfer problems by combining both finite element and finite difference schemes. It also couples to the Femap Flow package for thermo-fluid simulations.
The Femap Advanced Thermal Solver handles fully coupled conduction, convection, and radiation effects; the latter category includes wavelength-dependent optical properties, ray-tracing, and scattering. For example, users can simulate the effects of solar heating, electrical joule heating, and thermal ablation, topics critical to successful spacecraft design. They can also build and investigate heat transfer among part assemblies by defining thermal couplings between unconnected parts, and map the results to a Nastran model for a full thermo-elastic analysis.
A unique approach to managing thermal issues specific to semiconductor design comes from Mentor Graphics’ Mechanical Analysis Division, formerly known as Flomerics. Mentor Graphics offers FloTHERM.PACKSIM, an automated web-based program that helps non-thermal specialists quickly generate accurate package models and compute thermal characterization data.
![]() | ![]() |
3-D views of multi-layered printed circuit board analyzed with ANSYS Icemax, showing optimized meshing (right) for electromagnetic field solutions. Outputs include parasitic parameters forpackage-on-package, package-in-package, and package-on PCB designs. Images courtesy ANSYS |
FloTHERM.PACKSIM interfaces with Cadence Advanced Package Designer (APD) so users can easily import existing designs. More than 40 package models are currently supported, and more are being added. For early-stage analyses, the software’s SmartPart wizard can also generate a representative package model based on standard outlines, pincounts, and power. With just a few clicks, the simulation gives users a complete set of JEDEC thermal data metrics. They can then vary such parameters as die size, power, and lead pitch to evaluate different scenarios. A free one-month trial account is available, and a stand-alone version is in the works.
Page 1 | 2 »
Subscribe to our FREE magazine,
FREE email newsletters or both!Latest News
About the Author

Pamela Waterman worked as Digital Engineering’s contributing editor for two decades. Contact her via .(JavaScript must be enabled to view this email address).
Follow DE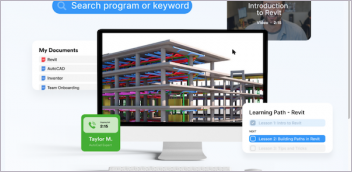

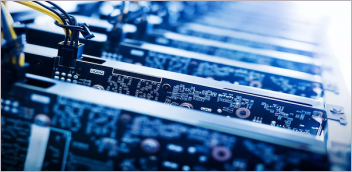
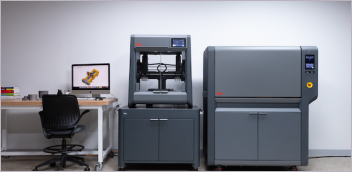