Get the Most from Advanced Materials
The need for composite and customized materials grows within the product engineering realm, but multiscale modeling and simulation software still needs fine tuning.

Fig. 1: Multiscale modeling and simulation tools help engineers to better understand the properties of a broad range of advanced materials. This capability opens the door for development teams to engineer the functionality of the materials to meet the specific requirements of their application. Image courtesy of e-Xstream Engineering.
January 17, 2020
Engineers increasingly turn to advanced materials to achieve the kind of performance demanded by the market. The driving force behind this trend lies in the fact that, in a growing number of use cases, conventional materials simply cannot deliver the physical properties sought by designers for aircraft wing assemblies or electronic devices.
As a result, material science will play a greater role in product development, adding a new dimension to design teams and increasing the impetus to adopt a multidiscipline design approach. It will also require the use of tools and techniques unfamiliar to many engineers.
Two of these technologies—multiscale modeling and simulation—promise to shed light on the properties of a broad array of materials and composites (Fig. 1).
By examining materials over different spatial and temporal scales, design teams can better investigate, test and engineer materials, determining their mechanical responses to production processes and changing environmental conditions (Fig. 2).
Fig. 2: MultiMechanics’ MultiMech 18.1 multiscale material modeling and simulation software supports composite tube and pressure vessel optimization, enabling engineers to predict and mitigate manufacturing-induced variations. Image courtesy of MultiMechanics.
Catalysts for Change
Why are engineers and developers turning to advanced materials, and why have technologies like multiscale modeling and simulation become important? This movement has been percolating for a while, slowly gaining momentum over time.
Once relegated to a few specialized, high-end applications, the drive to use advanced materials and their development technologies is casting a broader shadow over the marketplace.
The root of the movement lies in developers’ desire to enhance product performance by engineering the functionality of the materials from which they are made.
“The primary motivation for developing advanced materials is incorporation of specific material properties for specific applications,” says Ashfaq Adnan, assistant professor of mechanical and aerospace engineering at the University of Texas at Arlington.
A good example of this trend in action is a practice that has taken hold in the aircraft industry. To realize a cost savings of as much as 50%, aerospace companies push their designers to reduce fuel consumption by trimming aircraft weight. In the past, aluminum dominated aircraft construction.
However, designers now increasingly use composites like graphene-gold combinations to deliver high strength and toughness, but low density. This approach to the fuel efficiency issue also holds great relevance in the automobile industry.
Although some design goals can be sector specific, others hold broader applicability. These include enhancing performances of existing materials, improving material adaptability to environmental conditions and boosting durability and resilience. Another goal—currently very much in the spotlight—is the drive to reduce the environmental impact of current materials and material technologies.
Beyond the desire to achieve greater performance, the drive to develop and use advanced materials is also propelled by current and emerging design and manufacturing techniques.
“By using methods such as topology optimization and generative design, engineers come up with designs that would be impractical with traditional manufacturing methods,” says Bjorn Sjodin, vice president of product management at COMSOL.
“In addition, different additive manufacturing processes require new materials and material processes. Such materials need to be engineered not only from a structural perspective but also from the perspective of the materials’ ability to conduct heat so that they can cool efficiently, withstand or absorb electromagnetic fields, or resist fluid flow,” he adds.
Understanding Material Dynamics
Multiscale modeling and simulation help engineers better understand material properties by simultaneously characterizing the material over a range of spatial and temporal scales, accounting for structure-property relationships.
Typically, length-scale analysis covers the range between the atomistic scale [nm] and the continuum scale [mm]. Because most advanced materials have a complex, hierarchical structure, the engineering of a material and its properties becomes impossible without controlling several length scales.
“If we attempt to trace what controls the performance of materials at the macroscopic level, we can observe that properties of materials are largely dictated by the atomic structure, composition, microstructure, defects and interfaces in materials,” says Adnan. “All these features are not present in one length scale. Rather, they span over a broad range of length scales. As such, it is very important to quantitatively understand the mechanics and physics of materials over multiple length scales so that you can quantify how tuning the structure at the atomistic level can lead to achieving desired properties at the macroscopic scale.” (Fig. 3)
Multiscale models set the stage for comprehensive analysis of critical materials features within the context of a specific use case.
“Multiscale modeling enables the user to predict the macroscopic response, based on lower scale inputs, such as the microstructure descriptor and the constituent behavior that is most likely,” says Pierre Savoyat, a product manager for Digimat in the Hexagon Manufacturing Intelligence Division of e-Xstream Engineering. “The key point is that by bridging microscopic information to macroscopic behavior, the composite material’s response is described with greater accuracy.”
Fig. 3: This overview of a workflow for creating anisotropic material models shows how a “local macroscopic” behavior can be calculated from constituents’ properties for various performances. Image courtesy of e-Xstream Engineering.
Modeling multiple spatial and temporal scales and bridging data from the individual scales to create a more holistic picture represents a complex and daunting task. In fact, efforts to perfect these processes remain works in progress.
“Bridging length scales and time scales via a unique method or approach is usually not possible for materials with sufficient complexity, and multiscale modeling can only be achieved by combining different approaches—each designed specifically for a specific set of length scales—and passing the necessary information from one level of description to the next,” says Emanuela Del Gado, Provost’s distinguished associate professor, department of physics, Institute for Soft Matter Synthesis and Metrology, Georgetown University.
“This bridging therefore requires a considerable effort and is still being tested and investigated,” Del Gado adds. “Approaches that try to use the smallest possible scale description—say atomistic—and apply it to increasingly larger length scales, relying on increasing computational capabilities, typically fail. A true understanding of the different structural motifs and dynamic processes emerging at different length scales is needed.”
Multiscale Insights
For an idea of the value provided by multiscale modeling and simulation, step back and consider the larger picture. From the 61 commercially available elements in the periodic table, an engineer or scientist could theoretically create 36,000 alloys containing three elements. More than 90% of these alloys remain unexplored. Furthermore, within each one, there is a multitude of compositions, most of which will be of little interest.
“Identifying the compositions of interest through experimentation would be far too time consuming,” says Jim Goddin, manager of strategic relationships at ANSYS Granta. “Exploring these through modeling or simulation, however, promises to be more realistic.”
Thus, these technologies have the potential to help scientists and engineers identify new and promising research areas and provide insights into the fundamental nature of the materials in question.
“The insights and types of information provided by these tools go from chemical compositions and microstructural development to mechanical performances,” says Del Gado. “The chemical composition can allow for specific material functions, such as magnetic properties. But then the microstructural development—such as the development of pores and structural heterogeneities, including anisotropy—will play a role in the mechanical and dynamic properties and in the interaction with the environment or processing conditions.”
Multiscale modeling can provide unique details regarding where and why failure starts at the microscale, such as the primary mode of failure for specific loadings (Fig. 4). It could also be fiber break, matrix microcracking or fiber-matrix debonding.
Fig. 4: This simulation shows stress analysis of a laminated fiber composite cylinder. Modeling individual fibers in every layer of the laminate is not feasible. Instead, the software uses a simplified micromechanics model of a single carbon fiber in epoxy to estimate the elastic properties of a single layer in a separate analysis. Image courtesy of COMSOL.
“Concurrent multiscale modeling techniques—which have actual microstructural models being solved concurrently with the macroscopic part-level simulation—can provide a great deal of information, including stress and strain fields at lower scales,” says Flavio Souza, founder, president and CTO of MultiMechanics.
“With such additional insight and information, engineers can tweak the microstructural design variables to mitigate failure in specific applications, as well as optimize both part and material-level designs to meet specific requirements,” Souza adds.
These tools also let engineers gain crucial information on the material evolution while in use or during various aspects of the processing. By identifying and disentangling fundamental ingredients, multiscale modeling and simulation can transfer knowledge developed for one material class to another, and to export and extend functioning principles, a feature crucial to developing novel technologies.
Each step in the multiscale analysis process gives the engineer a richer pool of data from which to work.
“By iterating between the small and large scale, engineers build intuition for how the microstructure manifests itself at the macro scale,” says Sjodin. “Changing the design at the microscopic level may very well go hand in hand with changing the design at the macro level. You couldn’t do one without the other.”
Problems with Data
A core capability of multiscale modeling and simulation revolves around the generation of data that can readily be validated and applied to product development. Unfortunately, considering the current crop of tools, this is where problems can arise.
“Results must be comparable to the experiment and in a format that enables them to be successfully applied within the relevant engineering domain,” says ANSYS’ Goddin. “Many modeling efforts lack uniformity or comparability, meaning that the results, while interesting, require expert interpretation. This is one of the core drivers for materials information management efforts—capturing all relevant data in one place and in standard formats, enabling much easier comparison and analysis.”
This problem is compounded by the fact that engineers and scientists must merge analysis data from multiple spatial scales. As mentioned, this is where bridging capabilities become important.
“The crucial part is the capability to bridge information gleaned from across multiple length scales,” says Del Gado. “This is still a matter of research and work in progress. There is no automated way of doing this or optimized methods that work for all. Existing modeling and simulation techniques are useful and successful in some cases, but new approaches and techniques should also be developed. Building on machine learning capabilities to help devise such advanced methods could be helpful to design optimized bridging procedures.”
In addition to the problems arising from data incompatibility, engineers using multiscale modeling and simulation tools must also contend with “data blind spots.”
“Current modeling and simulation tools work best at scales where well-established methods can be applied, such as finite element analysis,” says Tony Rollett, professor of materials science and engineering at Carnegie Mellon University and faculty co-director of the Next Manufacturing Center.
“Even here, the tools depend on material models that often lack data,” he says. “For example, modeling 3D printing requires defining material properties all the way up to the melting point, but the mesoscale is often less well developed because microstructural evolution at the scale of defects and grains is notoriously hard to perform. This means that many microstructure-dependent properties are challenging to simulate.”
Handling Composites
Just as modeling and simulation software developers’ efforts continue to improve multiscale tools’ ability to manage heterogeneous data, changing market conditions have also provided the means to handle a growing variety of materials.
Many simulation software packages are tailored to handle homogeneous materials, such as plastics and metals. Composite materials, however, sometimes pose problems for multiscale modeling and simulation tools. This forces scientists and engineers to push the limits of the tools when implementing the integrative approach to multiscale modeling, which uses lower-scale information to solve larger-scale problems.
“Although such technology is already available to support design engineers and help them to maximize the benefit of using composite materials, the computational cost of the integrative approach has exceeded the design-cycle bandwidth for widespread use,” says Savoyat. “But with increasingly accessible computing power, integrated computational materials engineering has moved from theory to practice, with the approach being deployed to design advanced and highly optimized structures by accounting for their complexity at lower material scales.”
Just Getting Started
The rise of advanced materials seems poised to make fundamental changes in the way engineers design, enhance and test products. Work on atomic and molecular levels promises to become an integral aspect of product development.
Design software providers contend that the answer lies in specialized modeling and simulation tools. “Multiscale modeling promises to provide the right answer from the first simulation, to reduce errors and then possibly avoid expensive and time-wasting validation, prototyping, and testing procedures,” says Antoine Guiu, R&D manager, engineering plastics, at Solvay Performance Polyamides.
Although these tools have seen impressive advances and enjoyed significant success in the past decade, engineers and scientists still must come to terms with gaps in the technology’s capabilities. It’s clear that a number of issues critical for the tools’ development have yet to be addressed.
More Ansys Coverage
More COMSOL Coverage
More Hexagon Manufacturing Intelligence Coverage
Subscribe to our FREE magazine,
FREE email newsletters or both!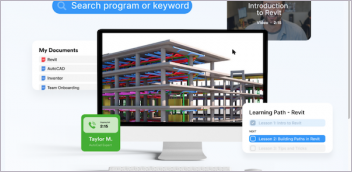

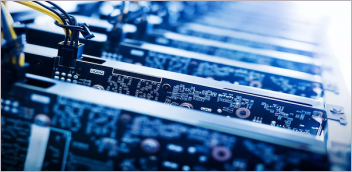
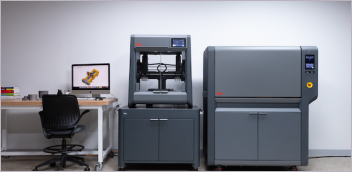