GE Bets On IIoT with Brilliant Factories

GE aims to become the connected factory solution provider. The company is launching Brilliant Factories, a mix of hardware, software, and consultation services (image courtesy of GE).
Latest News
October 16, 2017
GE, the brand that gives you your refrigerators and washers, is now gearing up to give you manufacturing plants, complete with industrial IoT (IIoT) setups. In doing so, GE moves into the territories of manufacturing giants like Siemens AG, the parent company of Siemens PLM Software.
“We’re manufacturers ourselves, so we have manufacturing capacity,” said Robert McKeel, president and CEO of GE Automation & Controls. “We also sell our technologies to other manufacturers to automate their plants and processes.”
This led to the launch of Brilliant Factories, a combination of hardware assets, software, and consultation services to upgrade your factories into IIoT powerhouses.
IIoT is not a replacement for the existing data management systems, McKeel pointed out. “This works with concert with your existing systems. You’ll still need your CAD and PLM. Our approach is largely based on gaining additional information from your existing assets.”

The Brilliant Factory offerings include, among others, Plant Applications for data management and data analysis, Product Manager Software for manufacturing execution, and Tracker Software for monitoring and executing orders, all from GE Digital.
“There’s a lot of capability in machines having knowledge about processes, just like people do,” noted McKeel. “We also start to invest in areas we see new opportunities, like additive manufacturing (AM). We did acquisitions in this space to expand our portfolio.”
AM and Machine Learning in Connected Factories
In April GE pumped U.S. $109 million (100 million Euros) into its AM business section. The year before, it snatched up the Swedish 3D printer maker Arcam for U.S. $1.3 billion. Arcam is now rebranded as a GE Additive Company.
The transaction gives GE the technology for metal-based AM, a distinct advantage in the aerospace and automotive spaces where manufacturers are looking for ways to consolidate multiple metal-part assemblies into lighter, smaller 3D-printed AM parts.
At the same time, GE is also bolstering its AI and machine learning functions in GE Predix, the company’s IIoT platform.
Predix, GE says on its product home page, “lets you deploy processing and analytics power to control edge assets in real time or analyze big data in the cloud using the secure Predix connectivity and execution environment.” It also allows you to deploy and manage digital twins.—data-driven representations of real products.
Wind Turbines That Know Which Way the Wind Blows
With an eye toward renewable energy, GE got into the wind farm business, dubbed the Digital Wind Farm, build on top of GE’s Predix.
“When we monitored the wind turbines’ performance, we noticed different performances across the wind farm,” McKeel pointed out. “So we started using data analytics and connectivity. In other words, each of the wind turbine is connected to the rest now. Now, whichever wind turbine is getting the best wind output, can communicate its pitch, blade angle, and position to the rest. The other turbines can in turn adjust their own setups to maximize wind output.”
Fleet analysis like this, McKeel proposes, can give connected factory operators and manufacturers insights that lead to dramatic productivity gains.
Enterprise IIoT sales cycles are much longer, and they’re driven by consultative relationships as well as technology. “We usually like to see a customer’s processes,” explained McKeel. “We can then let them know how we have solved similar issues, so the same approaches may work for them.”
IIoT Transformation Pain
Manufacturers of any size can benefit from such asset-management and AI-like automation functions, but technology maturity may determine whether they’re in a position to implement IIoT, McKeel observed. “The best candidates for Brilliant Factories are those with a specific problem to solve,” he added. “We work with them to achieve their goals.”
Part of the pain of such IIoT transformations may be workforce retraining. “It means someone who used to be part of the group that manually do assembly work, may have to be retrained to maintain the automation equipment instead,” said McKeel.
It might also mean retraining CAD operators to design for 3D printing instead of machining. “It takes a different kind of thinking to engineer something for additive manufacturing,” said McKeel.
Subscribe to our FREE magazine,
FREE email newsletters or both!Latest News
About the Author

Kenneth Wong is Digital Engineering’s resident blogger and senior editor. Email him at [email protected] or share your thoughts on this article at digitaleng.news/facebook.
Follow DE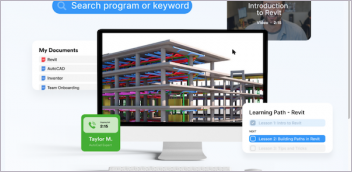

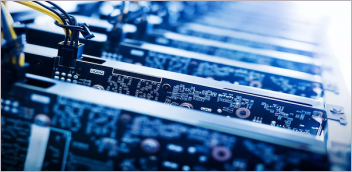
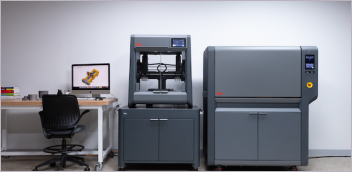