GE Aviation Invests in Five M Line Systems
During 2022 GE Additive to deliver systems to GE Aviation’s Additive Technology Center in West Chester, Ohio, and to Avio Aero in Turin, Italy.

L-R: Benito Trevino, general manager – additive integrated product team, GE Aviation and Chris Philp, ATC site leader, GE Aviation. Image courtesy of GE Aviation.
Latest News
February 10, 2022
GE Aviation is acquiring five GE Additive Concept Laser M Line systems. The first four M Line systems will be installed at GE Aviation’s Additive Technology Center (ATC) in West Chester, Ohio, during 2022. A fifth M Line system will be installed at Avio Aero’s Turin site in Italy to support serial production of additive components for the GE Catalystturboprop engine during 2022.
Customer-Centric Innovation
Throughout the M Line’s three-year maturation phase, GE Additive teams have worked collaboratively with GE Aviation and a small cohort of other aerospace and medical sector customers who are already in serial additive production to beta test the M Line system.
This phase has resulted in more than 300 design improvements with additional safety and software features incorporated into the system.
Continuous improvement and input from GE Aviation informed the most fundamental change to the system—an increase to the build envelope by 54% to 500mm x 500mm x 400mm—to enable GE Aviation’s progression to the serial production of larger additive parts, the company reports.
Over the past 18 months, attention has shifted to materials development for aerospace applications with some of the highest requirements in the industry for part quality in material properties, as well as build-to-build and machine-to-machine stability.
GE Additive and GE Aviation ATC teams have partnered to accelerate locking down the materials parameters for aluminum, cobalt chrome and nickel alloy 718, GE reports.
“The time and work we have collectively invested with our GE Additive colleagues to define, shape and then iron out the specification and functionality of the M Line means we now have a scalable solution that can build large components in a high-volume production environment, while meeting our cost entitlement goals,” says Chris Philp, site leader for GE Aviation’s ATC.
High-Rate Additive Production
Once installed at the GE Aviation ATC, two M Line systems will be dedicated to aluminum alloy, and one each of the two other systems to cobalt chrome and nickel alloy 718, adding additional manufacturing capacity to GE Aviation’s existing additive infrastructure in its development facility.
“Our goal is to realize the aviation additive industry’s first automation-ready production environment,” says Benito Trevino, general manager - additive integrated product team at GE Aviation. “Once installed, we envisage that our multi-machine approach, with the M Line platform at the heart of production, will help us reduce our lead and print times by over 50%.”
“At GE Aviation, we are continually developing more additive content for new engines, and the size and complexity of the parts increases with every generation of products developed,” said Philp.
Delivering Parts at Scale
The M Line is an advanced, industrialized production system that is suited to metal additive users who have started to scale production volumes. Its stitching capability enables customers with large part size demand to increase productivity and reduce cost for additive production, GE reports.
The M Line offers a new type of machine architecture that delivers modularity and automation (automation future release) and enables economical series production on an industrial scale. The system decouples the machine units used for part production and for set-up and dismantling processes.
The M Line’s flexible architecture also reduces costs as production grows. Users have the ability to independently add Laser Process Stations or Material Handling Stations based on capacity needs.
Sources: Press materials received from the company and additional information gleaned from the company’s website.
Subscribe to our FREE magazine,
FREE email newsletters or both!Latest News
About the Author

DE’s editors contribute news and new product announcements to Digital Engineering.
Press releases may be sent to them via [email protected].
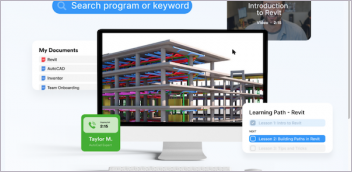

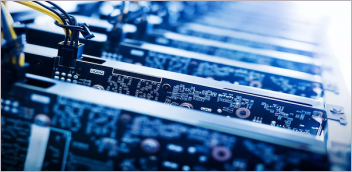
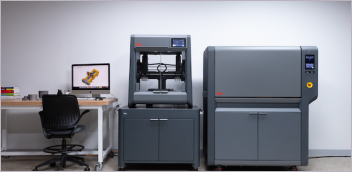