Following the Path of 3DP
The evolution of 3D printing mirrors the development of the 3D MCAD market--it'sready for you.
Latest News
March 1, 2005
By Jon Hirschtick
Over the course of my 20-year career, I have been fortunate enough tohave a front-row seat at the evolution of 3D MCAD technology, watchingits initial development, and following its mainstream adoption and use.From my early days with Computervision through the founding and growthof SolidWorks, I have devoted myself to addressing factors that havedriven today’s widespread adoption of 3D MCAD as the primary platformfor product development. Simply put, from its first rough attempts inthe 1970s, 3D MCAD needed to become affordable, easy to use, andpowerful enough to produce the commercially viable design applicationsthat are currently supplanting 2D design systems.
To get to this point, 3D MCAD had to evolve from the expensive,nonintuitive systems of the 1980s to those that were “ready foreveryone.” That breakthrough came during the 1990s, and today 3D MCADsystems have become the norm, representing a large and growingpercentage of all installed MCAD systems.
Barriers Give Way to BenefitsThe development of rapid prototyping (RP) technology, culminating intoday’s 3D printing systems, has followed a similar evolutionary path.In his bestseller, Crossing the Chasm, Geoffrey A. Moore describes thestages of the technology adoption lifecycle, which he applies to allnew technologies. There are early adopters, those who are so enamoredwith the technology that they are willing to accept a degree of riskand disruption in exchange for the potential benefits of the solution,and then there are mainstream users who wait and take a more cautiousapproach, weighing the benefits of a new solution against the impact ofchange. Early adopters handle the difficulties inherent in immaturetechnology while mainstream users wait until a certain level ofmaturity supports proven, tangible results. Before a technology goesmainstream, it must cross the chasm between something that’s new, niceto have, and used occasionally to something that’s established, readyfor everyone, and used heavily for definite benefits.
The initial rough attempts at RP appeared in the 1980s and the firstworkable systems followed in the 1990s. Early RP systems, such asstereolithography, were slow, expensive (both in machinery andprototype materials), and required specialized operating environmentsand expertise. With the advent of 3D printing technology in recentyears, developers have overcome many of the barriers to widespreadadoption of RP technology.
Just as 3D MCAD has crossed the chasm and become the norm, 3D printingis now making the same journey and is currently addressing the criticalissues that will drive large-scale adoption of the technology. And, as3D printing becomes the norm for RP, the technology will enhance thebenefits of 3D MCAD throughout manufacturing organizations bysupporting faster times to market, improving communication, reducingproduction costs, instilling better quality, and increasing innovation.
Fast, Affordable, and Easy to UseThe key factors supporting widespread use of 3D printing are speed,affordability, and ease of use; the same factors tackled by 3D MCADbefore manufacturers fully embraced that technology. And currently,developers of 3D printing technology are addressing the performance,cost, and usability issues that impeded widespread use of the firstworkable rapid prototyping systems.
Creating a prototype using one of those early systems ranged from daysto overnight which, while representing a vast improvement over the claymodeling-machining era, was still much too slow to provide maximumbenefits throughout the product development process. For physicalprototypes to provide real value to engineers during upfront conceptualdesign, as well as during design verification and production, timespent on their creation had to be condensed substantially. Engineersneed to be able to rattle off many design concepts in a short amount oftime to condense design cycles, cut manufacturing costs, improveproduct quality, and stimulate innovation. With 3D printing,performance has improved dramatically: what once took days can now bedone in a couple of hours, and improvements will continue.
Early RP systems were also cost-prohibitive; many systems were pricedat more than $100,000. The materials used to produce prototypes werealso somewhat exotic and expensive, discouraging widespread adoptionand everyday use. With the introduction of 3D printers using moreaffordable materials, system costs have fallen dramatically. Today, arobust 3D printing system can be purchased for an investment of around$30,000, and using less-expensive materials means prototypes can beproduced for $10 to $20 per piece.
Finally, while early rapid prototyping systems required a high level oftraining and expertise, as well as specialized operating environmentslike a laboratory or machine shop, 3D printers can now be used in anyoffice, with little training. And, they constitute a natural outputdevice for 3D MCAD systems. Just as 2D printers support physical outputof 2D documents from word-processing and 2D drafting applications, 3Dprinters provide physical output of 3D MCAD models right there in theoffice. Manufacturers no longer need a designated prototyping expertbecause anyone who can use a 3D MCAD system can operate a 3D printer.
Improving Model QualityAnother important development driving the widespread adoption of 3Dprinting technology is the improved quality of the physical models.Early RP systems had limited output options; older machines could onlycreate low-resolution models without the small, intricate details nowavailable. The parts were also often fragile and easily damaged, andonly available in a single color. When was the last time you saw ablack-and-white 3D MCAD model?
With the introduction of high-resolution, color 3D printingcapabilities developed by Z Corporation, model quality has reached anew plateau. The ability to touch, feel, and hold a robust 3D prototypeimparts much more information than an engineer can gain from a MCADimage on a computer screen. When color is added to the mix, engineerscan use sight and touch to interrogate and understand a designprototype fully. In the case of machine design, color is imperative fordistinguishing various parts of a complex assembly; it’s the reasonMCAD systems employ color. Color controls for 3D prints have become soprecise that an engineer can set a 24-bit color for each 3D pixel in amodel.
Logo placement, overlay of color-coded analysis results, and annotationare just a few of the other advantages of high-resolution, color 3Dprints. They provide benefits beyond engineering, including theopportunity for field testing, customer feedback, and sales andmarketing input. Combined with heightened performance, lower cost, andenhanced ease of use, improved prototype model quality makes thebenefits of 3D printing more obvious, tangible, and real.
Driving 2D-to-3D-MCAD MigrationInterestingly enough, though 3D printing has followed the sameevolutionary path to widespread adoption as 3D MCAD, the separatetechnologies are now feeding off one another: 3D printing technology isproviding a compelling rationale for transitioning from 2D MCAD to a 3Ddesign application.
Despite the proven benefits of 3D MCAD, many manufacturers continue touse 2D systems. One reason for this is that the final design output formany organizations, including those using 3D MCAD, is a 2D engineeringdrawing. Many manufacturers choose to maintain the status quo becauseit enables them to reach the same destination—albeit lessefficiently—rather than manage the change associated with a2D-to-3D-MCAD migration.
Now that 3D printing technology has matured to a point where it is moreusable, proven, and cost-effective, many of these organizationsperceive 3D printing as the impetus for making the transition to 3DMCAD. When 2D MCAD users realize that a 3D MCAD system will give themthe drawings they are used to and, when combined with 3D printing, letthem hold the part in their hands, they might finally be compelled tomove to 3D. The enhanced visualization and greater utility provided by3D MCAD might be interesting to them, but the combination of 3D MCADand 3D printing opens up a whole new world of possibilities. For manyorganizations, 3D printing represents the biggest advantage of makingthe move to 3D MCAD.
Something for Everyone3D printing is as close to magic as possible with technology;reminiscent of the replicator on the U.S.S. Enterprise of Star Trekfame. In addition to the cool factor, 3D printing has maturedsufficiently to cross the chasm between being an interesting infanttechnology to existing as a proven, beneficial application ready forprime time. It is finally ready for everyone. In a few short years, 3Dprinting will be widespread, giving engineers a valuable tool to gainthe insights they need to create a little magic of their own andproviding manufacturers a solution that improves their position in anincreasingly competitive global marketplace.
Jon Hirschtick, who has worked in mechanical engineering and MCAD for20 years, has a master’s degree in mechanical engineering from MIT andis a group executive with Dassault Systemes. He is a founder and formerCEO of SolidWorks Corporation and is on the board of directors of ZCorporation. To comment on this article, please write to[email protected].
Subscribe to our FREE magazine,
FREE email newsletters or both!Latest News
About the Author

DE’s editors contribute news and new product announcements to Digital Engineering.
Press releases may be sent to them via [email protected].
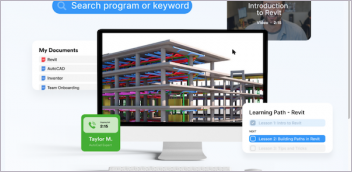

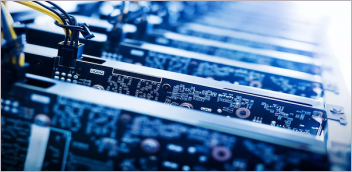
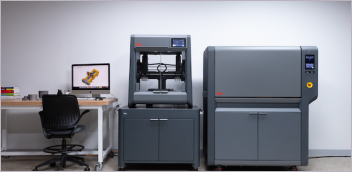