Latest News
December 30, 2013
New functionalities in ANSYS 15.0 provide enhancements to its computational fluid dynamics (CFD) offerings. Thanks to smart optimization technologies, faster solver speed, improved parallel scalability, intuitive geometry functionality and parallel meshing technologies, users of ANSYS 15.0 for fluid dynamics will be able to design new products faster and more accurately, the company says.
The adjoint solver now supports larger problems with meshes up to 30 million cells. The core functionality of the adjoint energy equation has been implemented in a way that observables can be defined as various integrals of heat flux and temperature, including averages and variances. As a result, the adjoint solver can now be used in problems where heat exchange maximization or heat loss reduction is a key design goal.
ANSYS 15.0 provides numerous solver speed improvements. For example, simulations of immiscible fluid using the volume-of-fluid model are up to 36 percent faster. Transient Eulerian multiphase flow simulations are also accelerated thanks to adaptive time-stepping support. Dynamic combustion mechanism reduction can lead to simulation up to seven times faster with large chemical mechanisms, the company says.
ANSYS 15.0 multi-layer shell conduction simplifies thermal management simulations and speeds up the overall workflow, avoiding the need to volume-mesh very thin material surfaces, the company says. Anisotropic thermal conductivity behavior for solid materials can also now be modeled. The surface-to-surface radiation model supports non-conformal meshes. This provides more flexibility in meshing both large fluid volumes together with thin fabricated structures, also helping to speed up the time to solution.
Multiphysics simulations are easier to setup and run thanks to the introduction of 2-way thermal and 2-way thermal with force/displacement with ANSYS Fluent and ANSYS Mechanical via system coupling, the company says. This solution fully automates simulations that were previously extremely time consuming to setup and perform.
Pre-processing complex CAD geometry is faster via the introduction of advanced diagnostic and repair tools that guide the user when dealing with problematic geometries. Geometry problems like holes and gaps are automatically detected and can be remedied with limited manual intervention. Major speed and memory use improvements have been implemented for all meshing methods. In addition, parallel meshing delivers reductions in mesh generation time.
ANSYS also announced improvements in its electronics offerings in release 15.0
“At ANSYS, we predict real-world product performance using fast, accurate and reliable simulation,” said Larry Williams, director of product management. “Our new release allows engineers to analyze electrical performance of smartphone circuit boards, stealth aircraft, and even the noise made by a washing machine.”
The solution includes new multiphysics analysis for noise, vibration and harshness (NVH) for electric machines and other electromechanical devices.
For high-frequency electromagnetics, advanced phi meshing for 3D electrical CAD/layout is optimized for meshing silicon substrates, redistribution layers, electronic packages, and printed circuit boards and advances the ANSYS HFSS 3D electrical layout design. This customized environment automates the process of preparing electrical layout data of printed circuit board (PCB), electronic packages and custom integrated circuits for analysis using HFSS. The Phi meshing technology augments this design flow by creating initial 3D meshes up to 30 times faster than previous releases while increasing capacity and reliability of meshing very complex ECAD geometry, the company says.
A new product, SIWave-DC, targeting the DC analysis of low-voltage, high-current PCB and IC packages, allows critical end-to-end voltage margins to be assessed to ensure reliable power delivery. It quickly identifies areas of excess current density and thermal hot spots to reduce risk of field failure. SIwave-DC is the first product to be released in an ongoing development project to deliver complete signal integrity and power integrity solutions. Additional products will be released with ANSYS 15.1 in early 2014.
A new multiphysics work flow that couples ANSYS Maxwell with ANSYS Mechanical allows electromagnetic force calculated by Maxwell to ANSYS Mechanical’s Structural Dynamic solver to evaluate the frequency spectrum of displacements and further compute the Acoustic Field.
Datakit Added to ANSYS Translation Suite
In addition, ANSYS has licensed the Datakit translation technology in its ANSYS translation products.
ANSYS is using Datakit technology to extend the range of CAD formats supported and to improve translation capabilities in the ANSYS geometry interface offerings. New geometry interfaces for JT and Catia V6 leveraging Datakit technology were introduced with the ANSYS 15.0 release in December. These are standalone interfaces that may be used without a locally installed CAD system.
“We’re very excited to have ANSYS license our data exchange technology,” said Francis Cadin, CEO of Datakit. “Datakit is committed to providing the best in translation technology for CAD/CAM/CAE software vendors and ANSYS’ selection of Datakit technology reflects the quality of technology and support we have achieved based on this commitment.”
For more information, visit ANSYS and Datakit.
Sources: Press materials received from the company and additional information gleaned from the company’s website.
Subscribe to our FREE magazine,
FREE email newsletters or both!Latest News
About the Author

DE’s editors contribute news and new product announcements to Digital Engineering.
Press releases may be sent to them via [email protected].
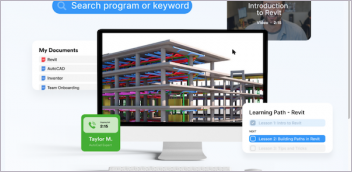

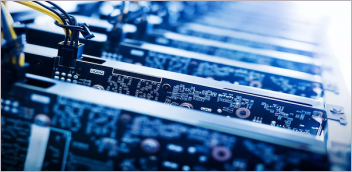
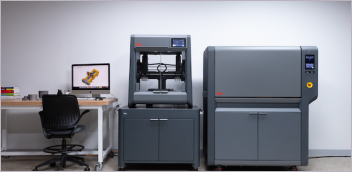