Fixing Smiles with Custom Orthodontics
Latest News
July 1, 2006
By Todd Grimm
Precision in lingual orthodontic appliances guaranteed to 5 microns (0.00019 in.).
In the past, the path to perfectly aligned teeth meant a smile marred by a mouthful of metal brackets and wire. For many adults, the stigma discourages them from undergoing orthodontic care. A solution to this problem is to hide the braces on the inside of the teeth. However, this simple idea poses unique challenges and difficulties.
^ ^ A German company designs and positions custom lingual brackets using CAD software before manufacturing metal brackets with rapid manufacturing equipment.
T.O.P. Service für Lingualtechnik in Bad Essen, Germany, has overcome the challenges and introduced its Incognito system. The company’s approach to positioning, optimizing results, and improving patient comfort relies heavily on custom appliances produced using rapid manufacturing technology.
Hidden Braces
Lingual (tongue side) orthodontic appliances (see Figure 1, below) are mounted on the inner surfaces of the teeth. Like those on the outside, the brackets are bonded to dental surfaces and an arch wire connects the brackets. Unlike traditional appliances for correcting a misaligned bite or malocclusion, lingual braces require precise bracket positioning and precise placement of each bracket’s arch wire slot. And, since they are mounted behind the teeth, the brackets must be small to avoid discomfort or impaired speech.
‹ ‹ Figure 1: Custom lingual brackets have a profile of 2 mm (0.08 in.) and an archwire slot guaranteed at 5 micron (0.00019 in.) precision.
T.O.P. (transfer optimized positioning) Service’s early success is due to its innovations in bracket placement. The T.O.P. system improved positional accuracy and reduced the patient’s time in the orthodontist’s chair. However, T.O.P. Service determined that it needed further improvements to decrease treatment times, optimize results, and relieve patient discomfort. In 2001, T.O.P. reinvented its processes and introduced custom lingual brackets. Designed patient-by-patient and tooth-by-tooth, these brackets deliver precise control for better results and a small profile that minimizes tongue irritation.
Custom Lingual Brackets
Each orthodontic appliance requires up to 16 brackets. T.O.P. Service begins with a malocclusion model (see Figure 2, below), which is used to digitally design brackets, and finishes with investment cast brackets made using dental gold.
^ ^ Figure 2: White-light scanning captures a digital representation of the malocclusion model for later placement of the brackets.
The lingual brackets measure 5 x 3 x 2 mm (0.200 x 0.118 x 0.079 in.), and they have only a 0.4 mm (0.016 in.) wall thickness. Producing these is complicated by the slots for the arch wire, which measure only 0.46 x 0.64 mm (0.018 x 0.025 in.). According to T.O.P. Service’s head of research and development, Ralf Paehl, Dipl.-Ing, “To impart multi-directional forces to the bracket, the rectangular slot must hold the arch wire, which can be round or rectangular, without any slippage.” This precision is so critical that T.O.P. Service guarantees ±5 micron (±0.00019 in.) slot tolerances for each of the custom brackets that it makes.
In its reinvention of the process, T.O.P. Service faced the challenge of developing a method to manufacture the customized brackets. After evaluating all possibilities, the company selected a Solidscape ModelMaker II system for creation of investment-cast patterns. According to Paehl, the key criteria in the evaluation were resolution, surface finish, castability, and precision.
“The biggest advantage of the Solidscape technology is the precision of the layer thickness,” said Dirk Wiechmann, T.O.P.’s CEO and founder. “To yield the ±5 micron precision, our only other option would be to wire EDM each bracket slot.”
Over the past four years, the company has expanded its operations to include eight Solidscape T66 Benchtop systems, enabling it to deliver 150 customized appliances a week.
The Manufacturing Process
Once malocclusion models of the patient’s teeth are cast from impressions taken by the orthodontist, they are manipulated to align the teeth to the target positions. This setup is reverse engineered with a white-light scanner (see Figure 2 above) to create a digital model that is loaded into T.O.P. Service’s design software. Selecting from a library of brackets, T.O.P. Service technicians position the brackets and adjust their features for optimal results (see page 28). The bracket design is output as an STL file for building patterns for investment casting.
^ ^ Figure 3: Bracket patterns are built with proprietary thermoplastic ink-jetting technology. The thermoplastic is deposited in droplets.
The T66 Benchtop, which can build with 13 micron (0.0005 in.) layers, constructs the bracket patterns (see Figure 3 above) with proprietary thermoplastic ink-jetting technology. The thermoplastic, which has wax-like properties, is deposited as small droplets. For precise layer thickness and flatness, a cutter mills the horizontal plane. When complete, the patterns are postprocessed by dissolving the support material and wiping off any debris.
^^ Custom lingual brackets bonded to malocclusion model prior to casting of transfer tray.
The next step is to attach cast pipes to the patterns and assemble them to make the casting tree. The tree is then embedded in a “speed plaster” to create the investment casting shell. The shell is heated to 690° C (1,274° F) to burn out the patterns before dental gold is cast into the investment. This process, which is computer-controlled, takes only two hours. Paehl said that he has 100 percent casting yield. “Short duration, low temperature burnout, and no residual ash are critical in our process. The Solidscape patterns give us all three,” said Paehl.
After cooling, the shell is broken away to yield the metal brackets. The runners (cast pipes) are then removed, and the brackets are tumbled in a polishing compound to smooth the surfaces.
^^ Investment cast lingual brackets after shell removal.
To complete the process, the brackets are mounted to the malocclusion model and a transfer tray, which captures the brackets, is cast. T.O.P. Service’s rapid manufacturing process, from treatment planning to shipment of the lingual appliance, takes only 10 to 15 days.
Continuous Improvement
In one year, T.O.P. Service has increased its production volume by 400 percent. Some of the increase is from the addition of more T66 Benchtop systems, more operating hours, and more technicians, but much of the throughput gain has resulted from improvements in Solidscape’s technology, process, and pattern material.
The most recent developments for the T66 Benchtop and the introduction of the InduraCast material have increased the company’s pattern production by 33 percent. Since T.O.P. Service runs its machines around the clock, this speed improvement has increased throughput without additional capital expenditures.
^^ T.O.P. Service now operates 8 T66 Benchtop systems.
Following the adoption of InduraCast, T.O.P. Service’s scrap rate for patterns has plummeted to a negligible amount. “The material has improved the quality of the bracket patterns and increased its durability. With walls of just 0.4 mm (0.016 in.), our technicians used to damage the patterns while preparing them for investment casting. Now, we have a pattern yield rate of 99.0 to 99.8 percent,” said Paehl. Since the investment casting yield rate is 100 percent, T.O.P. Service has a net bracket-casting yield that exceeds 99 brackets for every hundred patterns. This is nearly a 20 percent improvement in casting throughput.
Combined, the improvements have delivered a 55 percent increase in output from each of the company’s eight T66 Benchtop systems. This productivity gain has improved T.O.P. Service’s profitability by increasing capacity and decreasing staffing demands. “Prior to the latest developments, I had planned to add four casting technicians. Now I find that I only need two new employees to keep up with the demand,” said Paehl.
“We are using the Solidscape systems for mass production,” said Wiechmann, “and we find that they are producing quality devices.”
While he expects substantial growth in the coming years, Wiechmann says T.O.P. Service’s new challenge is gaining acceptance: “The potential market is huge. Our biggest hurdle is to convince the orthodontists that Incognito is not a difficult treatment process and that it is a better solution.”
Todd Grimm is president of T. A. Grimm & Associates, a consulting firm that focuses on rapid prototyping and reverse engineering. He is the author of Users Guide to Rapid Prototyping. Contact him at [email protected] or send an e-mail about this article by clicking here. Please reference “RP Smiles, August 2006” in your message.
Merrimack, NH
Incognito
T.O.P. Service fur Lingualtechnik
Bad Essen, Germany
Subscribe to our FREE magazine,
FREE email newsletters or both!Latest News
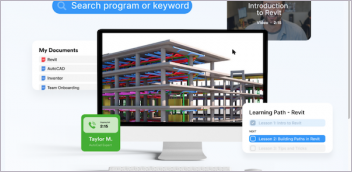

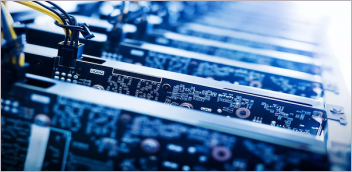
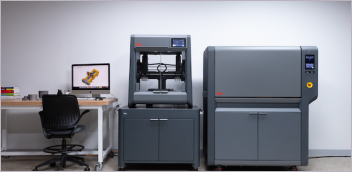